在现代铸造行业中,铸造造型是将液态金属浇注到预先准备好的铸型中,待其冷却凝固后形成所需形状的铸件。选择合适的铸造造型方法对铸件的质量和生产效率有着至关重要的影响。本文将详细探讨常见的铸造造型方法,帮助读者全面了解这些技术,并为相关企业提供有效的指导。
一、铸造造型方法概述
铸造造型是指根据设计要求,通过特定的工艺手段制作出能够容纳液态金属的铸型的过程。不同的造型方法适用于不同类型的铸件,具有各自的特点和优势。合理选择造型方法可以提高铸件质量、降低成本并缩短生产周期。
二、常见的铸造造型方法
(一)砂型铸造
1、手工造型
定义与特点:手工造型是最传统的砂型铸造方法之一,由工人使用工具(如刮板、拍板等)将型砂填入木模中,然后压实、修整,最后取出木模得到铸型。
适用范围:适用于单件或小批量生产,特别是对于形状复杂、尺寸较大的铸件。
优点:设备简单、成本低;灵活性高,适合多品种小批量生产。
缺点:劳动强度大、生产效率低;尺寸精度和表面质量相对较差。
2、机械化造型
定义与特点:机械化造型是利用专用设备(如震实台、射压造型机等)代替手工操作完成造型过程。它可以实现快速、高效、精确的造型。
适用范围:适用于大批量生产的中小型铸件,尤其是几何形状较为规则的产品。
优点:生产效率高、尺寸精度好;减轻了工人的劳动强度,提高了产品质量。
缺点:初期投资较大;对于复杂结构的铸件适应性较差。
3、树脂砂造型
定义与特点:树脂砂造型采用热固性或冷固性树脂作为粘结剂,将石英砂颗粒粘结在一起形成铸型。它具有高强度、高精度、透气性好等特点。
适用范围:广泛应用于汽车、航空航天、工程机械等领域,特别适合于高精度、复杂结构的铸件生产。
优点:尺寸精度高、表面光洁度好;减少了后续加工量,提高了成品率。
缺点:成本较高;需要专门的制芯设备和技术支持。
4、水玻璃砂造型
定义与特点:水玻璃砂造型以水玻璃(硅酸钠溶液)为粘结剂,通过加入硬化剂使其固化成形。该方法具有成本低、操作简便的优点。
适用范围:适用于一般中小型铸铁件、铸钢件的生产,特别是在一些对尺寸精度要求不高的场合。
优点:成本低廉、操作简单;环保性能较好,废弃物易于处理。
缺点:尺寸精度和表面质量不如树脂砂;硬化时间较长,生产效率较低。
(二)金属型铸造
1、重力铸造
定义与特点:重力铸造是将液态金属倒入金属模具中,在重力作用下填充型腔,冷却凝固后形成铸件。常用的金属模具材料包括灰铸铁、球墨铸铁、铝合金等。
适用范围:适用于中小型铸件的大批量生产,特别是对于几何形状简单、壁厚均匀的产品。
优点:生产效率高、尺寸精度好;铸件表面光洁度高,减少了后续加工量。
缺点:模具制造成本高;不适合复杂结构或大型铸件的生产。
2、压力铸造
定义与特点:压力铸造是在高压下将液态金属高速注入金属模具中,通过快速凝固形成铸件。这种工艺通常使用铝合金、锌合金等轻合金材料。
适用范围:广泛应用于汽车零部件、电子外壳等薄壁、复杂结构的小型铸件生产。
优点:生产效率极高,可实现自动化流水线作业;铸件尺寸精度高、表面光洁度好。
缺点:设备投资大;不适合大型或厚壁铸件;容易产生气孔、缩松等缺陷。
3、低压铸造
定义与特点:低压铸造是将液态金属在低压气体(如压缩空气)的作用下缓慢上升进入金属模具中,经过一定时间的保压后凝固成型。这种方法结合了重力铸造和压力铸造的优点。
适用范围:适用于中小型铸件的大批量生产,特别是对于铝合金、镁合金等有色金属铸件。
优点:铸件内部组织致密、力学性能好;减少了气孔、缩松等缺陷的发生。
缺点:设备复杂、操作难度较大;生产效率低于压力铸造。
(三)特种铸造
1、熔模铸造
定义与特点:熔模铸造也称为失蜡铸造,是先用蜡料制成与铸件相同的模型,然后在其表面涂覆耐火材料形成壳体,再将蜡模熔化排出,最后将液态金属注入壳体内凝固成型。
适用范围:广泛应用于航空发动机叶片、涡轮盘等精密零件的生产,以及艺术雕塑等领域。
优点:铸件尺寸精度极高、表面光洁度好;可以生产形状复杂、壁厚极薄的铸件。
缺点:工艺复杂、生产周期长;成本较高,主要用于高附加值产品。
2、离心铸造
定义与特点:离心铸造是将液态金属倒入旋转的金属模具中,在离心力的作用下使金属液沿型腔壁分布并凝固成型。根据旋转轴的方向不同,可分为立式离心铸造和卧式离心铸造。
适用范围:适用于生产圆筒形、环形等回转体铸件,如轧辊、管材、套筒等。
优点:铸件内部组织致密、力学性能好;减少了缩孔、缩松等缺陷的发生。
缺点:仅限于特定形状的铸件;设备成本较高。
3、消失模铸造
定义与特点:消失模铸造是以泡沫塑料为模型材料,将其放入干砂中振动紧实后形成铸型,然后将液态金属直接浇入,泡沫模型受热气化消失,最终形成铸件。
适用范围:适用于中小型铸件的大批量生产,特别是对于形状复杂、壁厚差异大的铸件。
优点:无需分型面,铸件整体性好;减少了后续加工量,提高了生产效率。
缺点:设备和技术要求较高;对于某些特殊合金材料的应用有限。
4、连续铸造
定义与特点:连续铸造是将液态金属连续不断地注入运动中的金属模具中,通过冷却凝固形成铸件。根据模具的运动方式不同,可分为水平连铸和垂直连铸。
适用范围:主要用于生产长条形、板状等规则形状的铸件,如铜杆、铝棒等。
优点:生产效率极高;铸件内部组织均匀,力学性能好。
缺点:设备投资大;只适用于特定形状的铸件。
5、真空密封铸造
定义与特点:真空密封铸造是在真空条件下进行的铸造工艺,通过抽真空排除型腔内的空气和气体,确保铸件内部无气孔、夹渣等缺陷。
适用范围:适用于高精度、高性能要求的铸件生产,如航空航天、医疗设备等领域。
优点:铸件内部质量好,减少了气孔、夹渣等缺陷;提高了铸件的力学性能和可靠性。
缺点:设备复杂、操作难度大;成本较高,主要用于高端产品。
三、铸造造型方法的选择依据
(一)铸件类型与结构
不同类型的铸件对造型方法有不同的要求。例如,形状复杂的铸件更适合采用树脂砂造型或熔模铸造;而规则形状的铸件则可以选择重力铸造或连续铸造。
(二)生产规模与批量
大规模生产的铸件应优先考虑机械化造型、压力铸造等高效工艺;而对于小批量或多品种生产,则可以采用手工造型或特种铸造方法。
(三)材料特性
不同材料的铸造性能差异较大,需根据材料特性选择合适的造型方法。例如,铝合金铸件适合采用压力铸造或低压铸造;而铸铁件则更多地使用砂型铸造。
(四)成本与经济效益
选择造型方法时还需综合考虑设备投资、原材料消耗、劳动力成本等因素,以实现最佳的经济效益。对于低成本、大批量生产的铸件,应优先选择自动化程度高、生产效率快的工艺;而对于高附加值、小批量生产的铸件,则可以适当放宽成本限制,追求更高的质量和精度。
(五)环境与安全因素
随着环保要求的日益严格,选择造型方法时还应考虑其对环境的影响。例如,水玻璃砂造型和消失模铸造相对环保,而传统砂型铸造则需要注意粉尘治理和废砂处理问题。
四、实际应用案例分析
(一)汽车发动机缸体制造
某汽车制造企业引入树脂砂铸造工艺后,成功解决了传统砂型铸造存在的尺寸偏差大、表面粗糙等问题。新工艺生产的发动机缸体尺寸精度提高了20%,表面光洁度提升了30%,废品率从原来的8%降至2%以下。同时,生产周期缩短了40%,综合成本降低了15%。
(二)航空航天零部件生产
某航空航天企业采用熔模铸造生产涡轮叶片等关键零部件。相比传统砂型铸造,新产品开发周期缩短了6个月,市场响应速度明显加快。此外,涡轮叶片的抗疲劳性能提高了15%,使用寿命延长了20%,产品质量显著提升。
(三)矿山机械设备齿轮箱体
某矿山设备制造商对大型破碎机的齿轮箱进行了低压铸造处理。处理后的齿轮箱体硬度达到了HRC60以上,耐磨性提高了50%,使用寿命延长了2倍以上。这大大减少了设备的维护成本,提高了生产效率。
五、总结
铸造造型方法的选择直接影响到铸件的质量、生产效率和经济效益。通过对砂型铸造、金属型铸造和特种铸造等常见工艺的理解,以及结合铸件类型、生产规模、材料特性、成本效益和环境安全等因素的综合考量,铸造企业可以选出最适合自身的造型方法,全面提升产品质量和竞争力。
一、铸造造型方法概述
铸造造型是指根据设计要求,通过特定的工艺手段制作出能够容纳液态金属的铸型的过程。不同的造型方法适用于不同类型的铸件,具有各自的特点和优势。合理选择造型方法可以提高铸件质量、降低成本并缩短生产周期。
二、常见的铸造造型方法
(一)砂型铸造
1、手工造型
定义与特点:手工造型是最传统的砂型铸造方法之一,由工人使用工具(如刮板、拍板等)将型砂填入木模中,然后压实、修整,最后取出木模得到铸型。
适用范围:适用于单件或小批量生产,特别是对于形状复杂、尺寸较大的铸件。
优点:设备简单、成本低;灵活性高,适合多品种小批量生产。
缺点:劳动强度大、生产效率低;尺寸精度和表面质量相对较差。
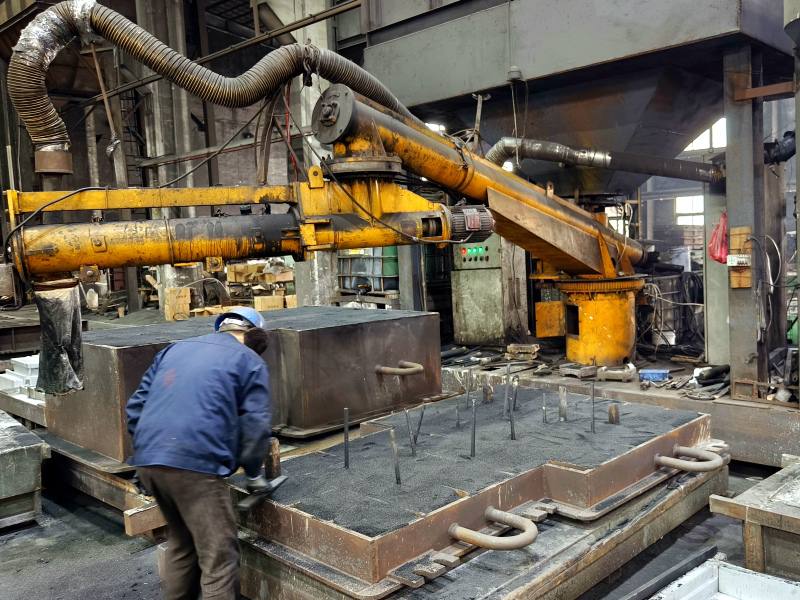
定义与特点:机械化造型是利用专用设备(如震实台、射压造型机等)代替手工操作完成造型过程。它可以实现快速、高效、精确的造型。
适用范围:适用于大批量生产的中小型铸件,尤其是几何形状较为规则的产品。
优点:生产效率高、尺寸精度好;减轻了工人的劳动强度,提高了产品质量。
缺点:初期投资较大;对于复杂结构的铸件适应性较差。
3、树脂砂造型
定义与特点:树脂砂造型采用热固性或冷固性树脂作为粘结剂,将石英砂颗粒粘结在一起形成铸型。它具有高强度、高精度、透气性好等特点。
适用范围:广泛应用于汽车、航空航天、工程机械等领域,特别适合于高精度、复杂结构的铸件生产。
优点:尺寸精度高、表面光洁度好;减少了后续加工量,提高了成品率。
缺点:成本较高;需要专门的制芯设备和技术支持。
4、水玻璃砂造型
定义与特点:水玻璃砂造型以水玻璃(硅酸钠溶液)为粘结剂,通过加入硬化剂使其固化成形。该方法具有成本低、操作简便的优点。
适用范围:适用于一般中小型铸铁件、铸钢件的生产,特别是在一些对尺寸精度要求不高的场合。
优点:成本低廉、操作简单;环保性能较好,废弃物易于处理。
缺点:尺寸精度和表面质量不如树脂砂;硬化时间较长,生产效率较低。
(二)金属型铸造
1、重力铸造
定义与特点:重力铸造是将液态金属倒入金属模具中,在重力作用下填充型腔,冷却凝固后形成铸件。常用的金属模具材料包括灰铸铁、球墨铸铁、铝合金等。
适用范围:适用于中小型铸件的大批量生产,特别是对于几何形状简单、壁厚均匀的产品。
优点:生产效率高、尺寸精度好;铸件表面光洁度高,减少了后续加工量。
缺点:模具制造成本高;不适合复杂结构或大型铸件的生产。
2、压力铸造
定义与特点:压力铸造是在高压下将液态金属高速注入金属模具中,通过快速凝固形成铸件。这种工艺通常使用铝合金、锌合金等轻合金材料。
适用范围:广泛应用于汽车零部件、电子外壳等薄壁、复杂结构的小型铸件生产。
优点:生产效率极高,可实现自动化流水线作业;铸件尺寸精度高、表面光洁度好。
缺点:设备投资大;不适合大型或厚壁铸件;容易产生气孔、缩松等缺陷。
3、低压铸造
定义与特点:低压铸造是将液态金属在低压气体(如压缩空气)的作用下缓慢上升进入金属模具中,经过一定时间的保压后凝固成型。这种方法结合了重力铸造和压力铸造的优点。
适用范围:适用于中小型铸件的大批量生产,特别是对于铝合金、镁合金等有色金属铸件。
优点:铸件内部组织致密、力学性能好;减少了气孔、缩松等缺陷的发生。
缺点:设备复杂、操作难度较大;生产效率低于压力铸造。
(三)特种铸造
1、熔模铸造
定义与特点:熔模铸造也称为失蜡铸造,是先用蜡料制成与铸件相同的模型,然后在其表面涂覆耐火材料形成壳体,再将蜡模熔化排出,最后将液态金属注入壳体内凝固成型。
适用范围:广泛应用于航空发动机叶片、涡轮盘等精密零件的生产,以及艺术雕塑等领域。
优点:铸件尺寸精度极高、表面光洁度好;可以生产形状复杂、壁厚极薄的铸件。
缺点:工艺复杂、生产周期长;成本较高,主要用于高附加值产品。
2、离心铸造
定义与特点:离心铸造是将液态金属倒入旋转的金属模具中,在离心力的作用下使金属液沿型腔壁分布并凝固成型。根据旋转轴的方向不同,可分为立式离心铸造和卧式离心铸造。
适用范围:适用于生产圆筒形、环形等回转体铸件,如轧辊、管材、套筒等。
优点:铸件内部组织致密、力学性能好;减少了缩孔、缩松等缺陷的发生。
缺点:仅限于特定形状的铸件;设备成本较高。
3、消失模铸造
定义与特点:消失模铸造是以泡沫塑料为模型材料,将其放入干砂中振动紧实后形成铸型,然后将液态金属直接浇入,泡沫模型受热气化消失,最终形成铸件。
适用范围:适用于中小型铸件的大批量生产,特别是对于形状复杂、壁厚差异大的铸件。
优点:无需分型面,铸件整体性好;减少了后续加工量,提高了生产效率。
缺点:设备和技术要求较高;对于某些特殊合金材料的应用有限。
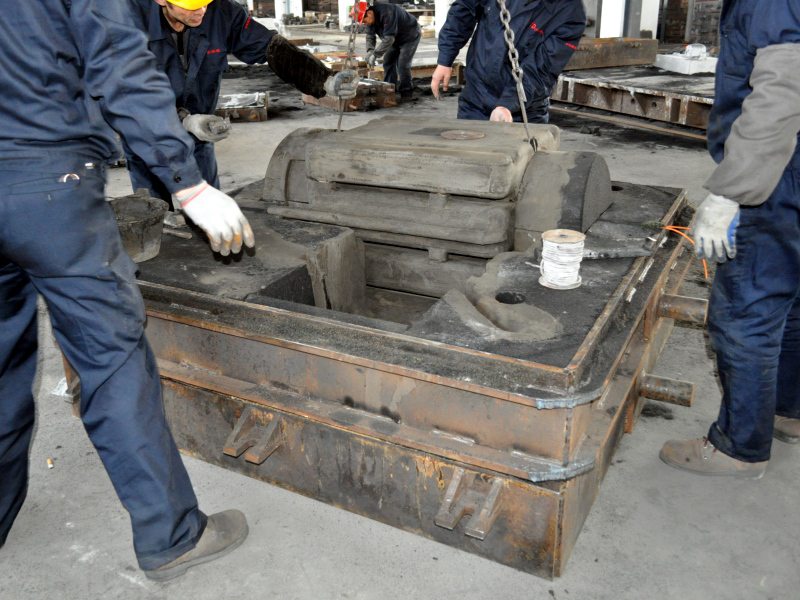
定义与特点:连续铸造是将液态金属连续不断地注入运动中的金属模具中,通过冷却凝固形成铸件。根据模具的运动方式不同,可分为水平连铸和垂直连铸。
适用范围:主要用于生产长条形、板状等规则形状的铸件,如铜杆、铝棒等。
优点:生产效率极高;铸件内部组织均匀,力学性能好。
缺点:设备投资大;只适用于特定形状的铸件。
5、真空密封铸造
定义与特点:真空密封铸造是在真空条件下进行的铸造工艺,通过抽真空排除型腔内的空气和气体,确保铸件内部无气孔、夹渣等缺陷。
适用范围:适用于高精度、高性能要求的铸件生产,如航空航天、医疗设备等领域。
优点:铸件内部质量好,减少了气孔、夹渣等缺陷;提高了铸件的力学性能和可靠性。
缺点:设备复杂、操作难度大;成本较高,主要用于高端产品。
三、铸造造型方法的选择依据
(一)铸件类型与结构
不同类型的铸件对造型方法有不同的要求。例如,形状复杂的铸件更适合采用树脂砂造型或熔模铸造;而规则形状的铸件则可以选择重力铸造或连续铸造。
(二)生产规模与批量
大规模生产的铸件应优先考虑机械化造型、压力铸造等高效工艺;而对于小批量或多品种生产,则可以采用手工造型或特种铸造方法。
(三)材料特性
不同材料的铸造性能差异较大,需根据材料特性选择合适的造型方法。例如,铝合金铸件适合采用压力铸造或低压铸造;而铸铁件则更多地使用砂型铸造。
(四)成本与经济效益
选择造型方法时还需综合考虑设备投资、原材料消耗、劳动力成本等因素,以实现最佳的经济效益。对于低成本、大批量生产的铸件,应优先选择自动化程度高、生产效率快的工艺;而对于高附加值、小批量生产的铸件,则可以适当放宽成本限制,追求更高的质量和精度。
(五)环境与安全因素
随着环保要求的日益严格,选择造型方法时还应考虑其对环境的影响。例如,水玻璃砂造型和消失模铸造相对环保,而传统砂型铸造则需要注意粉尘治理和废砂处理问题。
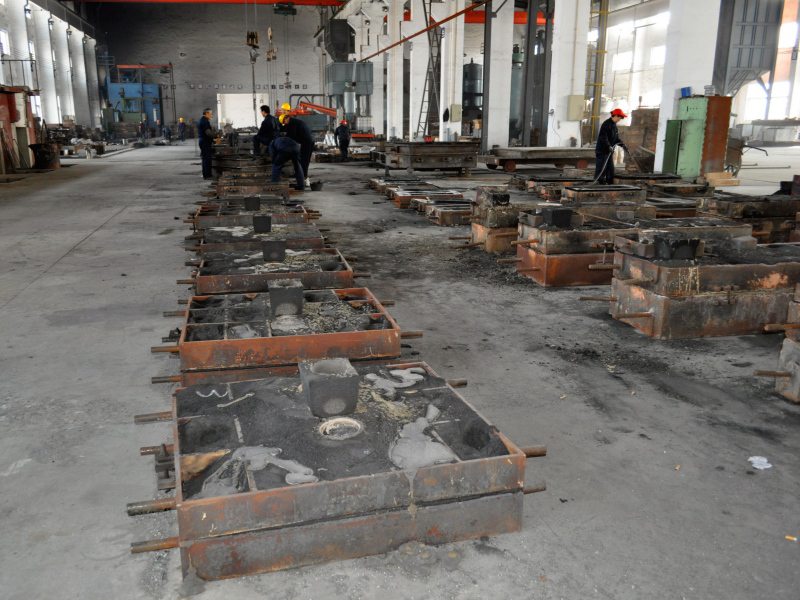
(一)汽车发动机缸体制造
某汽车制造企业引入树脂砂铸造工艺后,成功解决了传统砂型铸造存在的尺寸偏差大、表面粗糙等问题。新工艺生产的发动机缸体尺寸精度提高了20%,表面光洁度提升了30%,废品率从原来的8%降至2%以下。同时,生产周期缩短了40%,综合成本降低了15%。
(二)航空航天零部件生产
某航空航天企业采用熔模铸造生产涡轮叶片等关键零部件。相比传统砂型铸造,新产品开发周期缩短了6个月,市场响应速度明显加快。此外,涡轮叶片的抗疲劳性能提高了15%,使用寿命延长了20%,产品质量显著提升。
(三)矿山机械设备齿轮箱体
某矿山设备制造商对大型破碎机的齿轮箱进行了低压铸造处理。处理后的齿轮箱体硬度达到了HRC60以上,耐磨性提高了50%,使用寿命延长了2倍以上。这大大减少了设备的维护成本,提高了生产效率。
五、总结
铸造造型方法的选择直接影响到铸件的质量、生产效率和经济效益。通过对砂型铸造、金属型铸造和特种铸造等常见工艺的理解,以及结合铸件类型、生产规模、材料特性、成本效益和环境安全等因素的综合考量,铸造企业可以选出最适合自身的造型方法,全面提升产品质量和竞争力。