在风力发电设备中,轴承座作为关键部件之一,其铸造质量直接关系到整个风电机组的运行稳定性和寿命。然而,在实际生产过程中,风电轴承座铸造可能会遇到多种问题,影响产品质量和性能。本文将详细分析这些常见问题及其成因,并提供针对性的预防措施,帮助铸造企业提升产品质量,确保风电机组的安全可靠运行。
一、风电轴承座铸造常见问题
(一)缩孔与缩松
1、现象描述:缩孔和缩松是由于铸件冷却凝固时金属液收缩而形成的孔洞或疏松区域,通常出现在铸件厚大部位或最后凝固的地方。
2、对产品的影响:这些缺陷会导致铸件强度下降,局部应力集中,容易引发裂纹或断裂,严重影响轴承座的使用寿命和安全性。
(二)气孔
1、现象描述:气孔是指铸件内部或表面存在的气体孔洞,形状多为圆形或椭圆形,大小不一。
2、对产品的影响:气孔不仅降低铸件的致密度,还会削弱其机械性能,特别是抗疲劳强度和耐腐蚀性,从而影响轴承座的工作可靠性。
(三)夹渣
1、现象描述:夹渣是指在铸造过程中混入铸件中的非金属杂质,如氧化物、硫化物等,通常呈片状或点状分布。
2、对产品的影响:夹渣会破坏铸件基体的连续性,形成薄弱环节,导致应力集中,进而影响轴承座的力学性能和使用安全。
(四)裂纹
1、现象描述:裂纹是在铸造或后续加工过程中产生的细微裂缝,可能贯穿整个铸件或仅限于局部区域。
2、对产品的影响:裂纹是铸件最严重的缺陷之一,它会显著降低铸件的承载能力和韧性,增加失效风险,甚至可能导致风电机组停机检修。
(五)尺寸偏差
1、现象描述:尺寸偏差是指铸件的实际尺寸与设计要求不符,包括尺寸过大、过小或形状失真等情况。
2、对产品的影响:尺寸偏差会影响轴承座与其他零部件的装配精度,造成配合不良,进而影响风电机组的整体性能和工作效率。
二、风电轴承座铸造问题的成因分析
(一)熔炼过程控制不当
1、原材料选择不合理:选用低品质的废钢、铁合金等原材料,含有较多有害元素(如磷、硫),容易产生夹渣和气孔。
2、熔炼温度不稳定:熔炉温度过高或过低都会影响金属液的流动性,导致缩孔、缩松等问题;同时,温度波动还可能引入气体,形成气孔。
(二)模具设计与制造缺陷
1、浇注系统设计不合理:浇道、冒口位置不当或尺寸不合适,不能有效补缩,使得铸件厚大部位易出现缩孔、缩松。
2、排气系统不完善:模具排气不良会导致气体滞留,形成气孔;此外,砂型透气性差也会加剧这一问题。
3、模具材质选择不当:导热性能差的模具材料会使铸件冷却不均匀,增加裂纹和变形的风险。
(三)工艺参数设置错误
1、浇注速度控制不当:浇注速度过快或过慢都会影响金属液填充效果,导致冷隔、未完全融合等缺陷;同时,浇注速度不一致还可能引起铸件内部应力不均,形成裂纹。
2、冷却速度不合理:冷却速度过快或过慢都会影响铸件显微组织转变,使硬度、强度等性能指标达不到要求;极端情况下,还可能导致铸件开裂或变形。
(四)后处理工艺不到位
1、清理不彻底:铸件表面残留的砂子、氧化皮等杂物若未清除干净,会影响后续加工质量和外观美观度。
2、热处理工艺不规范:退火、正火等热处理工序如果操作不当,会导致铸件内部组织不均匀,影响力学性能和尺寸稳定性。
三、风电轴承座铸造问题的预防要点
(一)优化熔炼工艺
1、严格筛选原材料:优先选择高纯度、低杂质的优质原材料,确保金属成分符合标准要求,减少夹渣和气孔的产生。
2、精确控制熔炼温度:根据具体铸件材料特性,设定合理的熔炼温度范围,保持熔炉温度稳定,避免因温度波动引起的质量问题。
3、加强熔炼过程监控:采用先进的熔炼设备和技术手段,实时监测金属液成分和温度变化,及时调整工艺参数,确保熔炼质量。
(二)改进模具设计与制造
1、科学设计浇注系统:合理布置浇道、冒口的位置和尺寸,确保金属液能够充分填充型腔,实现良好的补缩效果,减少缩孔、缩松的发生。
2、完善排气系统:通过优化砂型透气性和增设排气通道等方式,保证气体顺畅排出,防止气孔形成。
3、选用优质模具材料:优先考虑具有良好导热性和耐磨性的模具材料,如高铬合金钢等,确保铸件冷却均匀,硬度分布合理,降低裂纹和变形风险。
(三)规范工艺参数设置
1、合理确定浇注速度:根据铸件壁厚和复杂程度,制定适宜的浇注速度,确保金属液平稳、均匀地填充型腔,避免冷隔、未完全融合等缺陷。
2、调整冷却速度:根据不同铸件的需求,选择适当的冷却介质(如空气、水、油等),调节冷却速度,使铸件各部分冷却均匀一致,确保显微组织转变良好,达到预期的力学性能和尺寸精度。
(四)强化后处理工艺
1、彻底清理铸件表面:采用抛丸、喷砂等高效清理方法,去除铸件表面的砂子、氧化皮等杂物,确保后续加工质量和外观美观度。
2、严格执行热处理工艺:按照标准要求进行退火、正火等热处理工序,确保铸件内部组织均匀一致,提高力学性能和尺寸稳定性;同时,定期校准热处理设备,保证工作参数准确可靠。
四、总结
风电轴承座铸造过程中可能出现的问题涉及多个方面,从原材料选择到最终成品的每一个环节都至关重要。通过对熔炼工艺、模具设计、工艺参数和后处理工艺的全面优化,可以有效预防和解决这些问题,提高风电轴承座的铸造质量,确保风电机组的安全可靠运行。希望本文提供的分析和建议能够为相关从业者提供有益参考,共同推动我国风电行业的健康发展。
通过以上详细分析和预防措施,相信读者对风电轴承座铸造常见问题有了更深入的理解。如有任何疑问或需要进一步的技术支持,请随时联系我们。
一、风电轴承座铸造常见问题
(一)缩孔与缩松
1、现象描述:缩孔和缩松是由于铸件冷却凝固时金属液收缩而形成的孔洞或疏松区域,通常出现在铸件厚大部位或最后凝固的地方。
2、对产品的影响:这些缺陷会导致铸件强度下降,局部应力集中,容易引发裂纹或断裂,严重影响轴承座的使用寿命和安全性。
(二)气孔
1、现象描述:气孔是指铸件内部或表面存在的气体孔洞,形状多为圆形或椭圆形,大小不一。
2、对产品的影响:气孔不仅降低铸件的致密度,还会削弱其机械性能,特别是抗疲劳强度和耐腐蚀性,从而影响轴承座的工作可靠性。
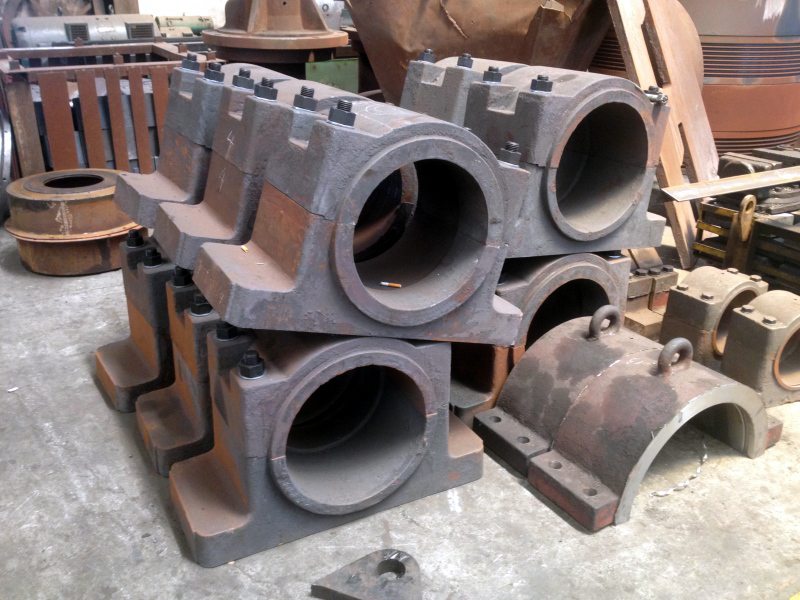
1、现象描述:夹渣是指在铸造过程中混入铸件中的非金属杂质,如氧化物、硫化物等,通常呈片状或点状分布。
2、对产品的影响:夹渣会破坏铸件基体的连续性,形成薄弱环节,导致应力集中,进而影响轴承座的力学性能和使用安全。
(四)裂纹
1、现象描述:裂纹是在铸造或后续加工过程中产生的细微裂缝,可能贯穿整个铸件或仅限于局部区域。
2、对产品的影响:裂纹是铸件最严重的缺陷之一,它会显著降低铸件的承载能力和韧性,增加失效风险,甚至可能导致风电机组停机检修。
(五)尺寸偏差
1、现象描述:尺寸偏差是指铸件的实际尺寸与设计要求不符,包括尺寸过大、过小或形状失真等情况。
2、对产品的影响:尺寸偏差会影响轴承座与其他零部件的装配精度,造成配合不良,进而影响风电机组的整体性能和工作效率。
二、风电轴承座铸造问题的成因分析
(一)熔炼过程控制不当
1、原材料选择不合理:选用低品质的废钢、铁合金等原材料,含有较多有害元素(如磷、硫),容易产生夹渣和气孔。
2、熔炼温度不稳定:熔炉温度过高或过低都会影响金属液的流动性,导致缩孔、缩松等问题;同时,温度波动还可能引入气体,形成气孔。
(二)模具设计与制造缺陷
1、浇注系统设计不合理:浇道、冒口位置不当或尺寸不合适,不能有效补缩,使得铸件厚大部位易出现缩孔、缩松。
2、排气系统不完善:模具排气不良会导致气体滞留,形成气孔;此外,砂型透气性差也会加剧这一问题。
3、模具材质选择不当:导热性能差的模具材料会使铸件冷却不均匀,增加裂纹和变形的风险。
(三)工艺参数设置错误
1、浇注速度控制不当:浇注速度过快或过慢都会影响金属液填充效果,导致冷隔、未完全融合等缺陷;同时,浇注速度不一致还可能引起铸件内部应力不均,形成裂纹。
2、冷却速度不合理:冷却速度过快或过慢都会影响铸件显微组织转变,使硬度、强度等性能指标达不到要求;极端情况下,还可能导致铸件开裂或变形。
(四)后处理工艺不到位
1、清理不彻底:铸件表面残留的砂子、氧化皮等杂物若未清除干净,会影响后续加工质量和外观美观度。
2、热处理工艺不规范:退火、正火等热处理工序如果操作不当,会导致铸件内部组织不均匀,影响力学性能和尺寸稳定性。
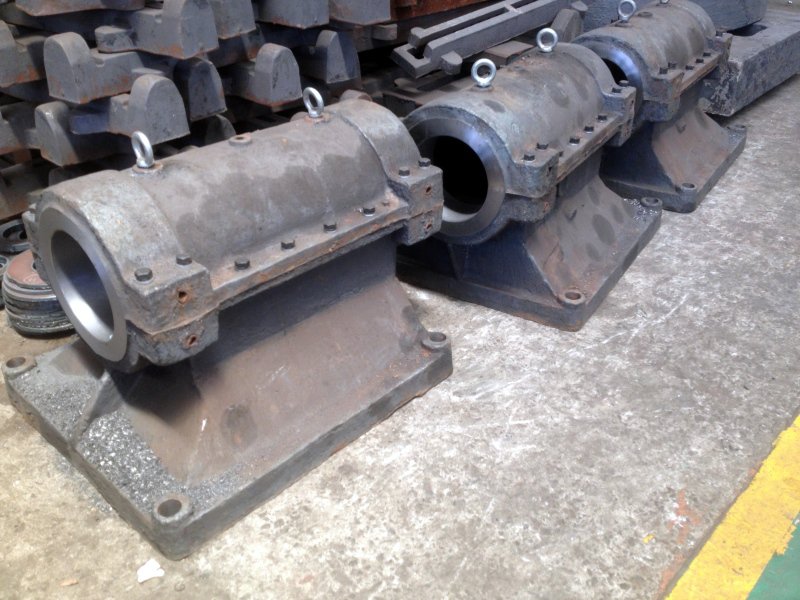
(一)优化熔炼工艺
1、严格筛选原材料:优先选择高纯度、低杂质的优质原材料,确保金属成分符合标准要求,减少夹渣和气孔的产生。
2、精确控制熔炼温度:根据具体铸件材料特性,设定合理的熔炼温度范围,保持熔炉温度稳定,避免因温度波动引起的质量问题。
3、加强熔炼过程监控:采用先进的熔炼设备和技术手段,实时监测金属液成分和温度变化,及时调整工艺参数,确保熔炼质量。
(二)改进模具设计与制造
1、科学设计浇注系统:合理布置浇道、冒口的位置和尺寸,确保金属液能够充分填充型腔,实现良好的补缩效果,减少缩孔、缩松的发生。
2、完善排气系统:通过优化砂型透气性和增设排气通道等方式,保证气体顺畅排出,防止气孔形成。
3、选用优质模具材料:优先考虑具有良好导热性和耐磨性的模具材料,如高铬合金钢等,确保铸件冷却均匀,硬度分布合理,降低裂纹和变形风险。
(三)规范工艺参数设置
1、合理确定浇注速度:根据铸件壁厚和复杂程度,制定适宜的浇注速度,确保金属液平稳、均匀地填充型腔,避免冷隔、未完全融合等缺陷。
2、调整冷却速度:根据不同铸件的需求,选择适当的冷却介质(如空气、水、油等),调节冷却速度,使铸件各部分冷却均匀一致,确保显微组织转变良好,达到预期的力学性能和尺寸精度。
(四)强化后处理工艺
1、彻底清理铸件表面:采用抛丸、喷砂等高效清理方法,去除铸件表面的砂子、氧化皮等杂物,确保后续加工质量和外观美观度。
2、严格执行热处理工艺:按照标准要求进行退火、正火等热处理工序,确保铸件内部组织均匀一致,提高力学性能和尺寸稳定性;同时,定期校准热处理设备,保证工作参数准确可靠。
四、总结
风电轴承座铸造过程中可能出现的问题涉及多个方面,从原材料选择到最终成品的每一个环节都至关重要。通过对熔炼工艺、模具设计、工艺参数和后处理工艺的全面优化,可以有效预防和解决这些问题,提高风电轴承座的铸造质量,确保风电机组的安全可靠运行。希望本文提供的分析和建议能够为相关从业者提供有益参考,共同推动我国风电行业的健康发展。
通过以上详细分析和预防措施,相信读者对风电轴承座铸造常见问题有了更深入的理解。如有任何疑问或需要进一步的技术支持,请随时联系我们。