在铸造行业中,熔炼是整个生产工艺的核心环节之一。熔炼的质量直接关系到铸件的化学成分、微观组织和力学性能,进而影响最终产品的质量和可靠性。本文将详细探讨在铸造生产中影响熔炼的主要因素,并提供相应的应对策略,帮助读者全面理解这一复杂而又重要的过程。
一、影响熔炼的主要因素
(一)原材料质量
1、生铁和废钢的选择
生铁:生铁是铸铁件的主要原料之一,其品质直接影响到铸铁件的质量。应选择含碳量适中、杂质少的优质生铁,以保证熔炼过程中金属液的纯净度。
废钢:废钢作为补充材料,可以调节铸铁中的碳当量和其他合金元素含量。选用清洁、无油污、无锈蚀的废钢,有助于减少夹渣和气孔等缺陷。
合金添加剂:根据产品需求,适量添加锰、铬、镍等合金元素,以改善铸铁件的耐磨性、耐腐蚀性和强度等性能。
2、原材料的配比
精确计算各种原材料的比例,确保熔炼后的金属液化学成分符合标准。使用自动配料系统或人工称重方式将各组分均匀混合,避免因比例失调而导致质量问题。
(二)熔炼设备与工艺参数
1、熔炼设备类型
冲天炉:传统熔炼设备,适用于大批量生产普通灰铸铁件。具有成本低、操作简单的特点,但环保性能较差。
感应电炉:现代高效熔炼设备,广泛应用于中小型铸铁件生产。它通过电磁感应原理加热金属,具有升温快、温度均匀、能耗低等优点。
电阻炉:适合小批量、多品种铸铁件试制及科研实验。结构简单、操作方便,能够实现精准控温。
2、熔炼温度与时间
合理的温度和时间设置对铸件的质量至关重要。过高的温度会导致合金元素烧损,影响铸件性能;而过低的温度则可能使金属液流动性不足,造成浇注困难。
引入自动控制系统,实现对熔炼过程的精确控制,确保每一批次铸件的一致性和稳定性。
3、熔炼速度
熔炼速度过快可能导致金属液不充分融化,残留未熔化的颗粒;过慢则会增加氧化夹杂物,影响金属液纯净度。合理控制熔炼速度,确保金属液完全融化且成分均匀。
(三)熔炼环境与气氛控制
1、空气湿度与温度
空气湿度和温度的变化会影响熔炼过程中的水分蒸发和氧化反应。高温高湿环境下,金属液容易吸收水分,导致氢气析出,形成气孔;低温干燥环境下,金属液流动性变差,影响填充效果。
在熔炼车间内安装温湿度控制系统,保持适宜的工作环境,减少外界因素对熔炼过程的影响。
2、保护气体与还原剂
在某些特殊合金的熔炼过程中,需要使用保护气体(如氩气、氮气)或还原剂(如铝、锰)来防止金属液氧化,保持其纯净度。
使用合适的保护气体和还原剂,可以有效降低氧化夹杂物的生成,提高金属液的流动性和铸造质量。
(四)熔炼过程中的搅拌与除渣
1、搅拌的作用
搅拌可以使金属液中的合金元素充分溶解,促进气体排出,减少缩孔、缩松等缺陷。对于感应电炉,还可以通过调整频率和功率,使金属液保持适当的搅拌状态。
定期取样分析金属液成分,及时调整配方,确保最终产品符合质量要求。
2、除渣的重要性
金属液中的渣滓会严重影响铸件的质量,导致夹渣、气孔等缺陷。采用专用工具将浮在金属液表面的渣滓清除干净,防止其混入铸件内部。
常用的除渣方法包括扒渣、过滤网过滤等,确保金属液纯净度。
(五)熔炼后的保温与冷却
1、保温处理
熔化完成后,将金属液转入保温炉或浇包中,维持一定温度范围(一般为1350-1450℃),以便后续工序使用。
保温期间,定期取样分析金属液成分,及时调整配方,确保最终产品符合质量要求。
2、冷却速度
冷却速度对铸件显微组织有重要影响。合理的冷却速度可以优化铸件的微观结构,提高其力学性能。根据铸件的具体需求,选择适当的冷却介质(如空气、水、油等)和冷却方式(如强制风冷、砂型自冷等)。
冷却过程中,注意监控铸件温度变化,及时采取措施防止开裂和变形。
(六)熔炼人员的技术水平
1、专业技能与经验
熔炼操作人员的专业技能和经验直接影响到熔炼质量。熟练掌握熔炼设备的操作规程和技术要点,能够及时发现并解决熔炼过程中出现的问题。
定期组织员工参加专业技能培训和技术交流活动,提高其业务水平和操作技能。
2、责任心与工作态度
操作人员的责任心和工作态度也非常重要。严格遵守操作规程,认真记录每次熔炼的数据信息,确保每一项工作都做到位。
建立激励机制,鼓励员工提出改进建议,共同推动企业技术创新和发展。
二、应对策略与最佳实践
(一)标准化操作流程
1、制定详细的工艺文件
编制涵盖从原材料准备到成品入库全过程的工艺文件,明确每个环节的操作步骤和技术要求,确保员工严格按照标准执行。
定期更新和完善工艺文件,结合实际生产情况和客户需求,不断优化工艺参数,提高产品质量。
2、加强员工培训
组织员工参加专业技能培训和技术交流活动,提高其业务水平和操作技能。特别是对于新入职员工,应进行系统的岗前培训,使其尽快熟悉生产工艺和操作规程。
建立激励机制,鼓励员工提出改进建议,共同推动企业技术创新和发展。
(二)严格的质量控制体系
1、建立质量检验制度
设立专门的质量检验部门,负责对原材料、半成品和成品进行全面检查。制定严格的检验标准和流程,确保每一个环节都符合质量要求。
引入第三方检测机构,对关键零部件进行抽样检测,进一步提高产品的可信度和可靠性。
2、实施持续改进计划
定期召开质量分析会议,总结生产过程中存在的问题,分析原因,制定整改措施。通过PDCA循环(计划执行检查行动)不断优化生产流程,提高产品质量。
加强与客户的沟通与合作,及时反馈产品质量信息,根据客户需求调整生产工艺,确保产品始终处于领先地位。
(三)信息化管理系统
1、引入ERP系统
利用企业资源计划(ERP)系统,实现对生产计划、库存管理、采购订单等业务流程的全面集成和优化。通过信息化手段提高企业管理效率,降低运营成本。
ERP系统可以实时监控生产进度,自动预警异常情况,帮助管理层及时做出决策,确保生产任务按时完成。
2、应用MES系统
制造执行系统(MES)可以实现对生产现场的实时监控和数据采集,为管理层提供准确的生产信息。通过MES系统,可以更好地协调各部门之间的协作,提高生产效率和产品质量。
MES系统还可以记录每个铸件的生产历史,包括原材料来源、加工工艺、检测结果等信息,形成完整的质量追溯体系,便于后续问题的查找和解决。
三、总结
在铸造生产中,影响熔炼的因素众多,涵盖了从原材料选择到最终冷却的各个环节。通过对这些因素的深入理解和科学管理,铸造厂可以有效提升熔炼质量,确保铸件的化学成分、微观组织和力学性能达到预期标准。希望本文提供的分析和建议能够为相关从业者提供有价值的参考,共同推动我国铸造行业的健康发展。
通过以上详细解析,相信读者对铸造生产中影响熔炼的关键因素有了更全面的认识。如有任何疑问或需要进一步的技术支持,请随时联系我们。
一、影响熔炼的主要因素
(一)原材料质量
1、生铁和废钢的选择
生铁:生铁是铸铁件的主要原料之一,其品质直接影响到铸铁件的质量。应选择含碳量适中、杂质少的优质生铁,以保证熔炼过程中金属液的纯净度。
废钢:废钢作为补充材料,可以调节铸铁中的碳当量和其他合金元素含量。选用清洁、无油污、无锈蚀的废钢,有助于减少夹渣和气孔等缺陷。
合金添加剂:根据产品需求,适量添加锰、铬、镍等合金元素,以改善铸铁件的耐磨性、耐腐蚀性和强度等性能。
2、原材料的配比
精确计算各种原材料的比例,确保熔炼后的金属液化学成分符合标准。使用自动配料系统或人工称重方式将各组分均匀混合,避免因比例失调而导致质量问题。
(二)熔炼设备与工艺参数
1、熔炼设备类型
冲天炉:传统熔炼设备,适用于大批量生产普通灰铸铁件。具有成本低、操作简单的特点,但环保性能较差。
感应电炉:现代高效熔炼设备,广泛应用于中小型铸铁件生产。它通过电磁感应原理加热金属,具有升温快、温度均匀、能耗低等优点。
电阻炉:适合小批量、多品种铸铁件试制及科研实验。结构简单、操作方便,能够实现精准控温。
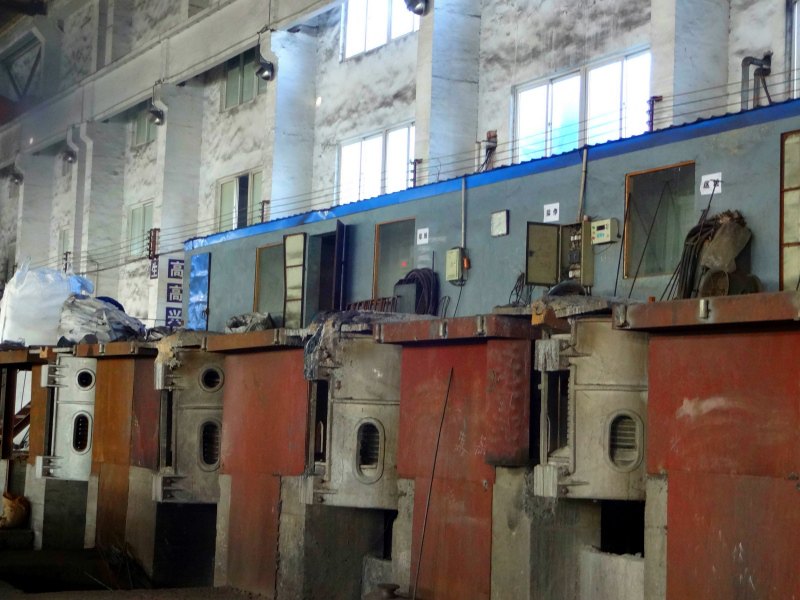
合理的温度和时间设置对铸件的质量至关重要。过高的温度会导致合金元素烧损,影响铸件性能;而过低的温度则可能使金属液流动性不足,造成浇注困难。
引入自动控制系统,实现对熔炼过程的精确控制,确保每一批次铸件的一致性和稳定性。
3、熔炼速度
熔炼速度过快可能导致金属液不充分融化,残留未熔化的颗粒;过慢则会增加氧化夹杂物,影响金属液纯净度。合理控制熔炼速度,确保金属液完全融化且成分均匀。
(三)熔炼环境与气氛控制
1、空气湿度与温度
空气湿度和温度的变化会影响熔炼过程中的水分蒸发和氧化反应。高温高湿环境下,金属液容易吸收水分,导致氢气析出,形成气孔;低温干燥环境下,金属液流动性变差,影响填充效果。
在熔炼车间内安装温湿度控制系统,保持适宜的工作环境,减少外界因素对熔炼过程的影响。
2、保护气体与还原剂
在某些特殊合金的熔炼过程中,需要使用保护气体(如氩气、氮气)或还原剂(如铝、锰)来防止金属液氧化,保持其纯净度。
使用合适的保护气体和还原剂,可以有效降低氧化夹杂物的生成,提高金属液的流动性和铸造质量。
(四)熔炼过程中的搅拌与除渣
1、搅拌的作用
搅拌可以使金属液中的合金元素充分溶解,促进气体排出,减少缩孔、缩松等缺陷。对于感应电炉,还可以通过调整频率和功率,使金属液保持适当的搅拌状态。
定期取样分析金属液成分,及时调整配方,确保最终产品符合质量要求。
2、除渣的重要性
金属液中的渣滓会严重影响铸件的质量,导致夹渣、气孔等缺陷。采用专用工具将浮在金属液表面的渣滓清除干净,防止其混入铸件内部。
常用的除渣方法包括扒渣、过滤网过滤等,确保金属液纯净度。
(五)熔炼后的保温与冷却
1、保温处理
熔化完成后,将金属液转入保温炉或浇包中,维持一定温度范围(一般为1350-1450℃),以便后续工序使用。
保温期间,定期取样分析金属液成分,及时调整配方,确保最终产品符合质量要求。
2、冷却速度
冷却速度对铸件显微组织有重要影响。合理的冷却速度可以优化铸件的微观结构,提高其力学性能。根据铸件的具体需求,选择适当的冷却介质(如空气、水、油等)和冷却方式(如强制风冷、砂型自冷等)。
冷却过程中,注意监控铸件温度变化,及时采取措施防止开裂和变形。
(六)熔炼人员的技术水平
1、专业技能与经验
熔炼操作人员的专业技能和经验直接影响到熔炼质量。熟练掌握熔炼设备的操作规程和技术要点,能够及时发现并解决熔炼过程中出现的问题。
定期组织员工参加专业技能培训和技术交流活动,提高其业务水平和操作技能。
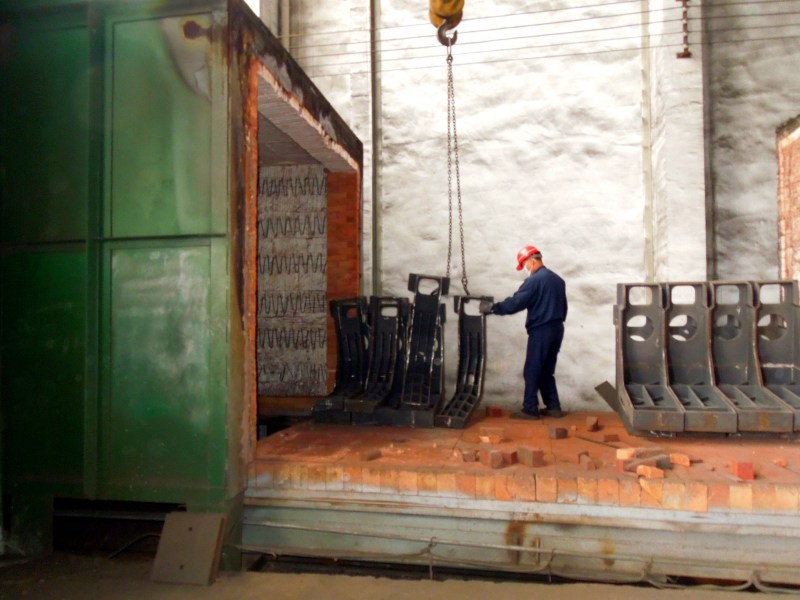
操作人员的责任心和工作态度也非常重要。严格遵守操作规程,认真记录每次熔炼的数据信息,确保每一项工作都做到位。
建立激励机制,鼓励员工提出改进建议,共同推动企业技术创新和发展。
二、应对策略与最佳实践
(一)标准化操作流程
1、制定详细的工艺文件
编制涵盖从原材料准备到成品入库全过程的工艺文件,明确每个环节的操作步骤和技术要求,确保员工严格按照标准执行。
定期更新和完善工艺文件,结合实际生产情况和客户需求,不断优化工艺参数,提高产品质量。
2、加强员工培训
组织员工参加专业技能培训和技术交流活动,提高其业务水平和操作技能。特别是对于新入职员工,应进行系统的岗前培训,使其尽快熟悉生产工艺和操作规程。
建立激励机制,鼓励员工提出改进建议,共同推动企业技术创新和发展。
(二)严格的质量控制体系
1、建立质量检验制度
设立专门的质量检验部门,负责对原材料、半成品和成品进行全面检查。制定严格的检验标准和流程,确保每一个环节都符合质量要求。
引入第三方检测机构,对关键零部件进行抽样检测,进一步提高产品的可信度和可靠性。
2、实施持续改进计划
定期召开质量分析会议,总结生产过程中存在的问题,分析原因,制定整改措施。通过PDCA循环(计划执行检查行动)不断优化生产流程,提高产品质量。
加强与客户的沟通与合作,及时反馈产品质量信息,根据客户需求调整生产工艺,确保产品始终处于领先地位。
(三)信息化管理系统
1、引入ERP系统
利用企业资源计划(ERP)系统,实现对生产计划、库存管理、采购订单等业务流程的全面集成和优化。通过信息化手段提高企业管理效率,降低运营成本。
ERP系统可以实时监控生产进度,自动预警异常情况,帮助管理层及时做出决策,确保生产任务按时完成。
2、应用MES系统
制造执行系统(MES)可以实现对生产现场的实时监控和数据采集,为管理层提供准确的生产信息。通过MES系统,可以更好地协调各部门之间的协作,提高生产效率和产品质量。
MES系统还可以记录每个铸件的生产历史,包括原材料来源、加工工艺、检测结果等信息,形成完整的质量追溯体系,便于后续问题的查找和解决。
三、总结
在铸造生产中,影响熔炼的因素众多,涵盖了从原材料选择到最终冷却的各个环节。通过对这些因素的深入理解和科学管理,铸造厂可以有效提升熔炼质量,确保铸件的化学成分、微观组织和力学性能达到预期标准。希望本文提供的分析和建议能够为相关从业者提供有价值的参考,共同推动我国铸造行业的健康发展。
通过以上详细解析,相信读者对铸造生产中影响熔炼的关键因素有了更全面的认识。如有任何疑问或需要进一步的技术支持,请随时联系我们。