在现代机械制造业中,齿轮箱体作为传动系统的关键部件之一,其质量和性能直接影响到整个设备的运行效率和可靠性。本文将详细探讨齿轮箱体铸件的制造工艺、技术要求及其广泛应用,帮助读者全面了解这一重要零部件,并为相关企业提供有效的指导。
一、齿轮箱体铸件的重要性
(一)支撑与保护作用
齿轮箱体不仅起到支撑齿轮、轴等传动部件的作用,还提供了封闭空间,防止灰尘、水分等外界因素对内部零件的影响,确保传动系统的正常运行。
(二)承载能力
齿轮箱体需要承受来自齿轮啮合时产生的巨大切削力和振动。因此,它必须具备足够的强度和刚性,以保证长期稳定的工作性能。
(三)密封性要求
良好的密封性可以防止润滑油泄漏,保持内部润滑条件,延长齿轮和其他部件的使用寿命。同时,密封性也关系到设备的安全性和环保性能。
二、齿轮箱体铸件的制造工艺
(一)原材料选择
1、生铁和废钢
选用含碳量适中、杂质少的优质生铁和清洁无油污的废钢,以保证熔炼过程中金属液的纯净度。
2、合金添加剂
根据产品需求,适量添加锰、铬、镍等合金元素,以改善铸件的耐磨性、耐腐蚀性和强度等性能。
(二)熔炼与浇注
1、熔炼设备选择
感应电炉:广泛应用于中小型铸铁件生产。它通过电磁感应原理加热金属,具有升温快、温度均匀、能耗低等优点。
电阻炉:适合小批量、多品种铸铁件试制及科研实验。结构简单、操作方便,能够实现精准控温。
2、熔炼工艺控制
精确控制化学成分:通过光谱分析仪等设备实时监测金属液成分,及时调整配方,确保每一批次铸件的化学成分稳定一致。
优化熔炼温度和时间:合理的温度和时间设置对铸件的质量至关重要。过高的温度会导致合金元素烧损,影响铸件性能;而过低的温度则可能使金属液流动性不足,造成浇注困难。
3、浇注系统设计
浇道的设计直接影响到金属液的填充效果和铸件的内部质量。科学合理地布置浇道,可以使金属液平稳、均匀地流入型腔,减少气孔、缩松等缺陷。
4、浇注速度控制
浇注速度过快或过慢都会影响铸件的质量。过快的速度容易引发冷隔、未完全融合等问题;而过慢的速度则可能导致铸件内部出现疏松、缩孔等缺陷。通过引入自动化控制系统,实现对浇注速度的精确控制,确保每一件铸件都能获得最佳的成型效果。
(三)模具设计与制造
1、高精度模具材料选择
模具材料的选择直接影响到铸件的尺寸精度和表面质量。选用具有良好导热性和耐磨性的模具材料(如高铬合金钢),可以有效提高铸件的成型质量和使用寿命。
2、先进的模具制造技术
利用数控机床、3D打印等先进技术进行模具加工,可以显著提高模具的精度和一致性。特别是对于形状复杂的铸件,3D打印技术可以在短时间内完成模具制作,缩短开发周期。
3、定期维护和校准模具
定期维护和校准模具,确保其始终保持最佳状态,减少因模具磨损或变形导致的尺寸偏差。
(四)冷却与凝固
1、冷却介质选择
冷却介质的选择对铸件的显微组织和力学性能有重要影响。根据铸件的具体需求,选择适当的冷却介质(如空气、水、油等),调节冷却速度,使铸件各部分冷却均匀一致。
2、控制凝固顺序
合理安排铸件的凝固顺序,可以有效防止缩孔、缩松等缺陷的产生。通过设置冷铁、冒口等辅助装置,引导金属液从厚大部位向薄壁处流动,实现定向凝固。
3、利用计算机模拟技术
提前预测铸件的凝固过程,优化冷铁和冒口的布置方案,确保铸件内部无缺陷。
(五)清理与后处理
1、去除表面杂质
使用砂轮、刮刀等工具清除铸件表面的氧化皮、油污、锈蚀等杂质,确保焊补面干净平整。
2、表面修整与抛光
使用砂轮、锉刀等工具对焊缝进行打磨,使其与铸件表面平滑过渡,保证外观美观和尺寸精度。
对有特殊要求的铸件,可进行抛光处理,提高表面光洁度,增强耐磨性和抗腐蚀能力。
3、检测与验收
在生产线上安装在线检测设备(如超声波探伤仪、磁粉探伤仪等),可以实时监控铸件的质量状况,及时发现潜在问题,避免不合格品流入下一道工序。
配备高精度的测量工具(如三坐标测量机、激光测距仪等),对铸件的尺寸精度进行严格把关。定期校准测量仪器,确保其准确性,避免因测量误差导致的质量问题。
三、齿轮箱体铸件的技术要求
(一)尺寸精度
1、几何尺寸
包括齿轮箱体的高度、宽度、厚度等关键尺寸。确保这些尺寸在规定的公差范围内。
2、形状精度
包括齿轮箱体的平面度、圆柱度、圆锥度、垂直度、平行度等。确保齿轮箱体的形状符合设计要求。
3、位置精度
包括齿轮箱体上各部分之间的相对位置关系,如孔距、中心距、同轴度等。确保各部分的位置准确无误。
(二)表面质量
1、表面粗糙度
表面粗糙度是指齿轮箱体表面微观不平的程度。通过检测表面粗糙度,可以评估齿轮箱体的外观质量和加工性能。
2、表面缺陷
检测齿轮箱体表面是否存在裂纹、气孔、夹渣、砂眼等缺陷。这些缺陷会影响齿轮箱体的强度和使用寿命。
(三)内部质量
1、内部缺陷
检测齿轮箱体内部是否存在缩孔、缩松、气孔、夹渣等缺陷。这些缺陷会削弱齿轮箱体的力学性能,影响其使用安全性。
2、组织结构
分析齿轮箱体内部的显微组织,包括晶粒大小、分布、相组成等。合理的显微组织可以提高齿轮箱体的强度、硬度和耐磨性。
四、齿轮箱体铸件的应用实例
(一)风力发电齿轮箱
某风力发电设备制造商采用高精度树脂砂铸造工艺生产齿轮箱体铸件。新工艺生产的齿轮箱体尺寸精度提高了20%,表面光洁度提升了30%,废品率从原来的8%降至2%以下。同时,生产周期缩短了40%,综合成本降低了15%。此外,经过调质处理后的齿轮箱体硬度达到了HRC35-40,抗拉强度提高了20%,疲劳寿命延长了30%,大大提高了风力发电机组的可靠性和耐用性。
(二)矿山机械设备齿轮箱
某矿山设备制造商对大型破碎机的齿轮箱进行了淬火和低温回火处理。处理后的齿轮箱体硬度达到了HRC60以上,耐磨性提高了50%,使用寿命延长了2倍以上。这大大减少了设备的维护成本,提高了生产效率。
(三)船舶推进系统齿轮箱
某船舶制造企业在生产船舶推进系统齿轮箱时,采用了正火和高温回火相结合的热处理工艺。处理后的齿轮箱体强度和韧性得到了显著提升,能够承受海洋环境中巨大的冲击力和腐蚀,确保了船舶的安全航行。
五、总结
齿轮箱体铸件作为传动系统的关键部件,其制造工艺和技术要求直接关系到设备的性能和可靠性。通过对原材料选择、熔炼与浇注、模具设计与制造、冷却与凝固、清理与后处理等环节的严格把控,以及遵循严格的尺寸精度、表面质量和内部质量标准,铸造企业可以全面提升产品质量,满足客户日益增长的需求。希望本文提供的分析和建议能够为相关从业者提供有价值的参考,共同推动我国铸造行业的健康发展。
通过以上详细解析,相信读者对齿轮箱体铸件有了更全面的认识。如有任何疑问或需要进一步的技术支持,请随时联系我们。
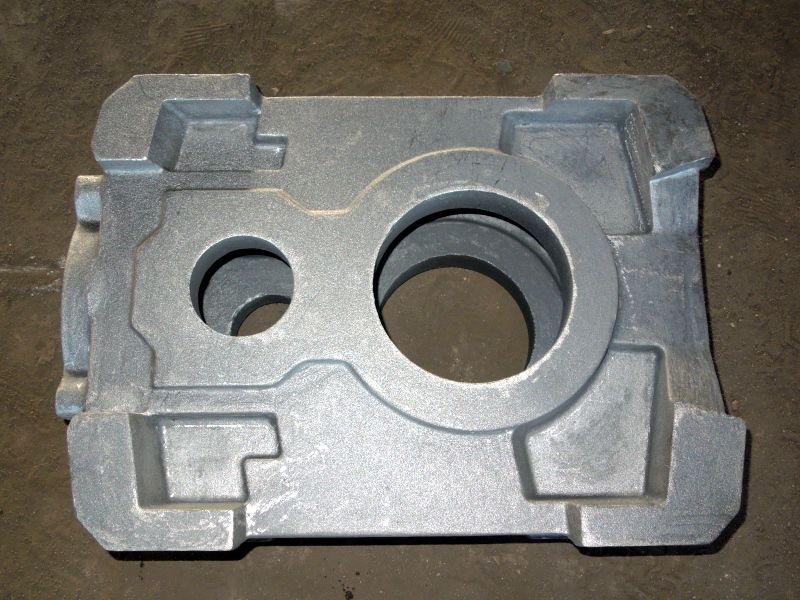
一、齿轮箱体铸件的重要性
(一)支撑与保护作用
齿轮箱体不仅起到支撑齿轮、轴等传动部件的作用,还提供了封闭空间,防止灰尘、水分等外界因素对内部零件的影响,确保传动系统的正常运行。
(二)承载能力
齿轮箱体需要承受来自齿轮啮合时产生的巨大切削力和振动。因此,它必须具备足够的强度和刚性,以保证长期稳定的工作性能。
(三)密封性要求
良好的密封性可以防止润滑油泄漏,保持内部润滑条件,延长齿轮和其他部件的使用寿命。同时,密封性也关系到设备的安全性和环保性能。
二、齿轮箱体铸件的制造工艺
(一)原材料选择
1、生铁和废钢
选用含碳量适中、杂质少的优质生铁和清洁无油污的废钢,以保证熔炼过程中金属液的纯净度。
2、合金添加剂
根据产品需求,适量添加锰、铬、镍等合金元素,以改善铸件的耐磨性、耐腐蚀性和强度等性能。
(二)熔炼与浇注
1、熔炼设备选择
感应电炉:广泛应用于中小型铸铁件生产。它通过电磁感应原理加热金属,具有升温快、温度均匀、能耗低等优点。
电阻炉:适合小批量、多品种铸铁件试制及科研实验。结构简单、操作方便,能够实现精准控温。
2、熔炼工艺控制
精确控制化学成分:通过光谱分析仪等设备实时监测金属液成分,及时调整配方,确保每一批次铸件的化学成分稳定一致。
优化熔炼温度和时间:合理的温度和时间设置对铸件的质量至关重要。过高的温度会导致合金元素烧损,影响铸件性能;而过低的温度则可能使金属液流动性不足,造成浇注困难。
3、浇注系统设计
浇道的设计直接影响到金属液的填充效果和铸件的内部质量。科学合理地布置浇道,可以使金属液平稳、均匀地流入型腔,减少气孔、缩松等缺陷。
4、浇注速度控制
浇注速度过快或过慢都会影响铸件的质量。过快的速度容易引发冷隔、未完全融合等问题;而过慢的速度则可能导致铸件内部出现疏松、缩孔等缺陷。通过引入自动化控制系统,实现对浇注速度的精确控制,确保每一件铸件都能获得最佳的成型效果。
(三)模具设计与制造
1、高精度模具材料选择
模具材料的选择直接影响到铸件的尺寸精度和表面质量。选用具有良好导热性和耐磨性的模具材料(如高铬合金钢),可以有效提高铸件的成型质量和使用寿命。
2、先进的模具制造技术
利用数控机床、3D打印等先进技术进行模具加工,可以显著提高模具的精度和一致性。特别是对于形状复杂的铸件,3D打印技术可以在短时间内完成模具制作,缩短开发周期。
3、定期维护和校准模具
定期维护和校准模具,确保其始终保持最佳状态,减少因模具磨损或变形导致的尺寸偏差。
(四)冷却与凝固
1、冷却介质选择
冷却介质的选择对铸件的显微组织和力学性能有重要影响。根据铸件的具体需求,选择适当的冷却介质(如空气、水、油等),调节冷却速度,使铸件各部分冷却均匀一致。
2、控制凝固顺序
合理安排铸件的凝固顺序,可以有效防止缩孔、缩松等缺陷的产生。通过设置冷铁、冒口等辅助装置,引导金属液从厚大部位向薄壁处流动,实现定向凝固。
3、利用计算机模拟技术
提前预测铸件的凝固过程,优化冷铁和冒口的布置方案,确保铸件内部无缺陷。
(五)清理与后处理
1、去除表面杂质
使用砂轮、刮刀等工具清除铸件表面的氧化皮、油污、锈蚀等杂质,确保焊补面干净平整。
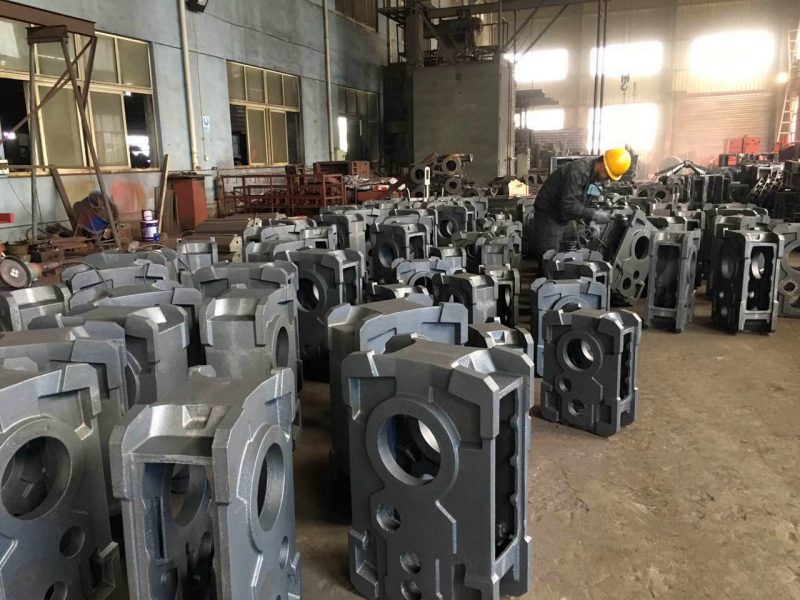
使用砂轮、锉刀等工具对焊缝进行打磨,使其与铸件表面平滑过渡,保证外观美观和尺寸精度。
对有特殊要求的铸件,可进行抛光处理,提高表面光洁度,增强耐磨性和抗腐蚀能力。
3、检测与验收
在生产线上安装在线检测设备(如超声波探伤仪、磁粉探伤仪等),可以实时监控铸件的质量状况,及时发现潜在问题,避免不合格品流入下一道工序。
配备高精度的测量工具(如三坐标测量机、激光测距仪等),对铸件的尺寸精度进行严格把关。定期校准测量仪器,确保其准确性,避免因测量误差导致的质量问题。
三、齿轮箱体铸件的技术要求
(一)尺寸精度
1、几何尺寸
包括齿轮箱体的高度、宽度、厚度等关键尺寸。确保这些尺寸在规定的公差范围内。
2、形状精度
包括齿轮箱体的平面度、圆柱度、圆锥度、垂直度、平行度等。确保齿轮箱体的形状符合设计要求。
3、位置精度
包括齿轮箱体上各部分之间的相对位置关系,如孔距、中心距、同轴度等。确保各部分的位置准确无误。
(二)表面质量
1、表面粗糙度
表面粗糙度是指齿轮箱体表面微观不平的程度。通过检测表面粗糙度,可以评估齿轮箱体的外观质量和加工性能。
2、表面缺陷
检测齿轮箱体表面是否存在裂纹、气孔、夹渣、砂眼等缺陷。这些缺陷会影响齿轮箱体的强度和使用寿命。
(三)内部质量
1、内部缺陷
检测齿轮箱体内部是否存在缩孔、缩松、气孔、夹渣等缺陷。这些缺陷会削弱齿轮箱体的力学性能,影响其使用安全性。
2、组织结构
分析齿轮箱体内部的显微组织,包括晶粒大小、分布、相组成等。合理的显微组织可以提高齿轮箱体的强度、硬度和耐磨性。
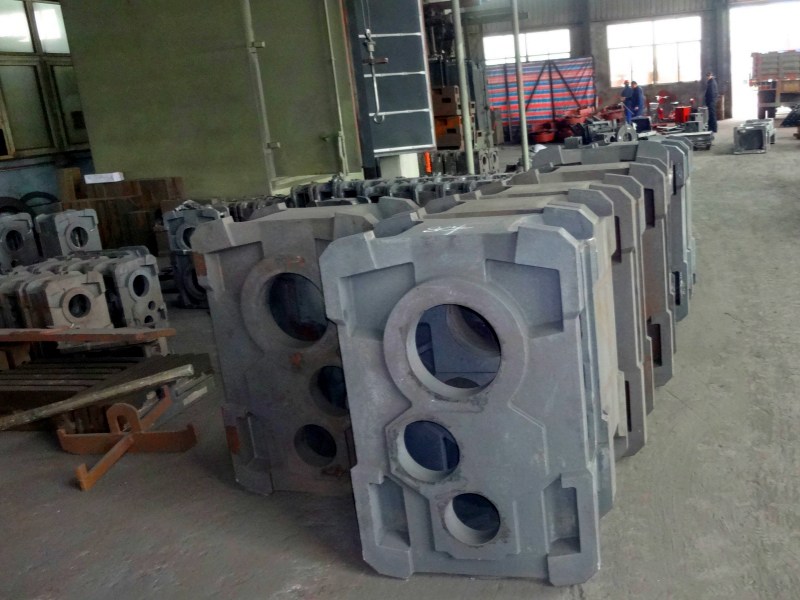
(一)风力发电齿轮箱
某风力发电设备制造商采用高精度树脂砂铸造工艺生产齿轮箱体铸件。新工艺生产的齿轮箱体尺寸精度提高了20%,表面光洁度提升了30%,废品率从原来的8%降至2%以下。同时,生产周期缩短了40%,综合成本降低了15%。此外,经过调质处理后的齿轮箱体硬度达到了HRC35-40,抗拉强度提高了20%,疲劳寿命延长了30%,大大提高了风力发电机组的可靠性和耐用性。
(二)矿山机械设备齿轮箱
某矿山设备制造商对大型破碎机的齿轮箱进行了淬火和低温回火处理。处理后的齿轮箱体硬度达到了HRC60以上,耐磨性提高了50%,使用寿命延长了2倍以上。这大大减少了设备的维护成本,提高了生产效率。
(三)船舶推进系统齿轮箱
某船舶制造企业在生产船舶推进系统齿轮箱时,采用了正火和高温回火相结合的热处理工艺。处理后的齿轮箱体强度和韧性得到了显著提升,能够承受海洋环境中巨大的冲击力和腐蚀,确保了船舶的安全航行。
五、总结
齿轮箱体铸件作为传动系统的关键部件,其制造工艺和技术要求直接关系到设备的性能和可靠性。通过对原材料选择、熔炼与浇注、模具设计与制造、冷却与凝固、清理与后处理等环节的严格把控,以及遵循严格的尺寸精度、表面质量和内部质量标准,铸造企业可以全面提升产品质量,满足客户日益增长的需求。希望本文提供的分析和建议能够为相关从业者提供有价值的参考,共同推动我国铸造行业的健康发展。
通过以上详细解析,相信读者对齿轮箱体铸件有了更全面的认识。如有任何疑问或需要进一步的技术支持,请随时联系我们。