在中锰抗磨球墨铸铁件生产中,常见的铸件缺陷除有灰铸铁件和球墨铸铁件的一般缺陷外,还有碳化物量过高或连续网状分布、索氏体量和奥氏体量过高等。通常,产生这些缺陷的原因不单是化学成分中Si/Mn比的选择问题,有时还有造型制芯、熔炼浇注、配砂质量、落砂清理等许多生产工序的问题,因此必须具体分析,以便采取相应的合理措施加以解决。
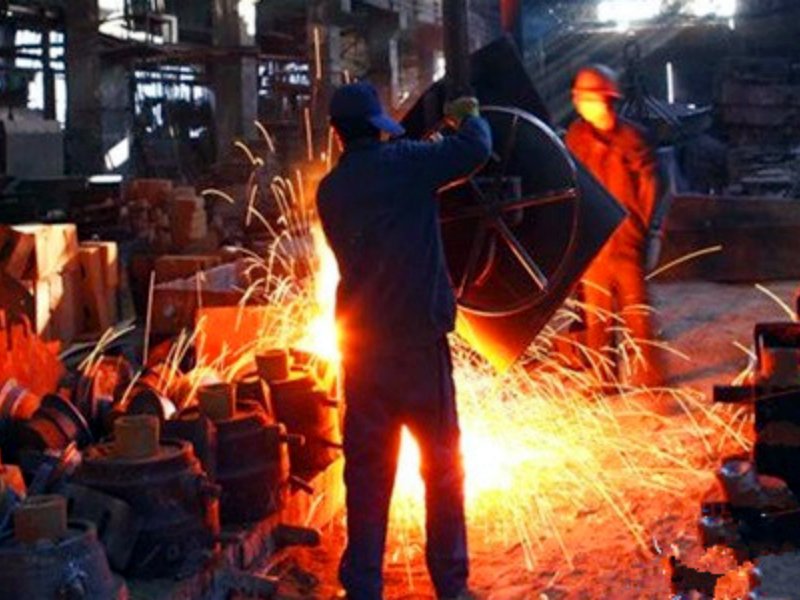
生产中锰抗磨球墨铸铁件时,除常见的一般(包括球化处理方面的)外,属于中锰抗磨球墨铸铁件特有的一些缺陷及其原因分析与防止方法可参见如下。
特征:
1.脆性大、冲击韧度αk<4.0J/cm2
2.试片断口齐平,颜色灰白,或者白而发亮
3.三角试片白口过大
原因分析:
1.Si/Mn低或Mn是过高
2.冷却速度过快,或打箱太早
3.ω(RE+Mg残留量)>0.1%或球化剂加入最过多
4.孕育剂加入量不够或效果不佳
5.碳化物的质量分数>40%
防止方法:
1.进行护前快速分析,正确控制Si、Mn含量
2.控制球化剂加入量,在保证球化的前提下,尽量减少球化剂加入量
3.球化剂加入量过多时,应及时补加原铁液。一般补加10%-15%,原铁液可使白口宽度减少1-2mm
4.减少RE+Mg残留量中的RE 量,使RE<Mg量,ω(RE+Mg)<0.09%
5.适当增加Si量或Si/Mn比
6.加强孕育,增加一次孕育量和进行二次孕育或瞬时孕育
7.炉前补加质量分数0.2%~0.3%的FeSi75可降低三角试片白口宽度1-2mm
8.减少冷却速度,提高金属型顶热温度,采用隔热涂料
索氏体或奥氏体量过高特征:
1.冲击韧度αk和硬度HRC低
2.脆性增加,抗磨性能不好
3.试片断口呈深灰色,敲击声发哑
原因分析:
1.在800~500℃冷却过程中冷却速度太低。奥氏体易于转变成索氏体、托氏体,索氏体量φ>40%
2.Si/Mn过大,Si量过高,共析转变温度区扩大,有利于形成索氏体
3.Mn量过高,或者Si/Mn太小,共析温度低下,奥氏体量过多(φ>50%)
防止方法:
1.控制冷却速度,ωSi3.4%~4.5%,ωMn5.5%~6.5%时,在750~500℃范围内。冷却速度应>20℃/min,控翻在18~36℃/min为宜。<18℃/min易产生索氏体。>36℃/min易形成奥氏体
2.根据铸件壁厚、铸型工艺等影响冷却速度的因素,选择合适的Si/Mn控制奥氏体转变成索氏体的数量。一般Si/Mn<0.6时即Si低Mn高,奥氏体量增多,Si/Mn>0.75时。即Si高Mn低,索氏体量增高,在冷却速度一定条件下,Si/Mn是控制奥氏体和索氏体t的重要手段
气孔、夹渣、缩孔特征:
1.铸件产生皮下气孔;
2.铸件内部有集中或分散气孔;
3.冒口下或周围出现集中或分散性气孔或缩孔且深浅不一;
4.铸件内或热节处产生密集蜂窝状气孔
原因分析:
1.出温度低于1400℃浇注温度过低
2.球化反应不充分,搅拌扒渣不够
3.渣气孔层取样分析结果(质量分数)如下:C4.98%,Mn4.67%,P0.088%,S0.128%,RExOy:0.663%, Mg0.203%。
分析表明:渣气孔主要是稀土镁的氧化物和石墨,当铁液温度低或浇注温度过低,此类夹渣不易排出
防止方法:
1.提高出铁温度,出铁槽中铁液温度应>1450℃
2.采用半封闭式浇注系统直浇道断面:横浇道断面:溢流口:内浇道=1.2:2:1=1.4。直浇道>溢流口有利于缓流。溢流口<横浇道有利于撇渣。内浇道溢流口有利于排气
3.炉前球化处理后,加人冰晶石(NaAlF2)。它易与MgS化合成低溶点易凝聚的MgF2、Na2S、NaO等化合物,从溶渣中排出。加入冰晶石后应静置,有益于上述反应充分进行
4.金属型需预热至200~300℃时浇注,刷涂料要及时烤干。湿砂造型时型砂水分应<4%(质量分教)
5.厚大铸件浇注应采用一快、二慢、三冲。中小件采用一快、二慢的浇注方法。
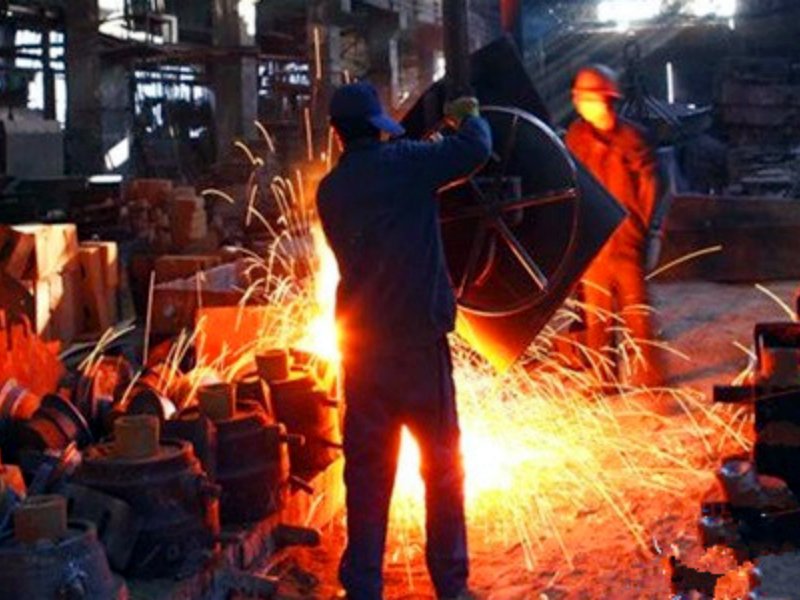
生产中锰抗磨球墨铸铁件时,除常见的一般(包括球化处理方面的)外,属于中锰抗磨球墨铸铁件特有的一些缺陷及其原因分析与防止方法可参见如下。
碳化物过量或呈连续网状分布
特征:
1.脆性大、冲击韧度αk<4.0J/cm2
2.试片断口齐平,颜色灰白,或者白而发亮
3.三角试片白口过大
原因分析:
1.Si/Mn低或Mn是过高
2.冷却速度过快,或打箱太早
3.ω(RE+Mg残留量)>0.1%或球化剂加入最过多
4.孕育剂加入量不够或效果不佳
5.碳化物的质量分数>40%
防止方法:
1.进行护前快速分析,正确控制Si、Mn含量
2.控制球化剂加入量,在保证球化的前提下,尽量减少球化剂加入量
3.球化剂加入量过多时,应及时补加原铁液。一般补加10%-15%,原铁液可使白口宽度减少1-2mm
4.减少RE+Mg残留量中的RE 量,使RE<Mg量,ω(RE+Mg)<0.09%
5.适当增加Si量或Si/Mn比
6.加强孕育,增加一次孕育量和进行二次孕育或瞬时孕育
7.炉前补加质量分数0.2%~0.3%的FeSi75可降低三角试片白口宽度1-2mm
8.减少冷却速度,提高金属型顶热温度,采用隔热涂料
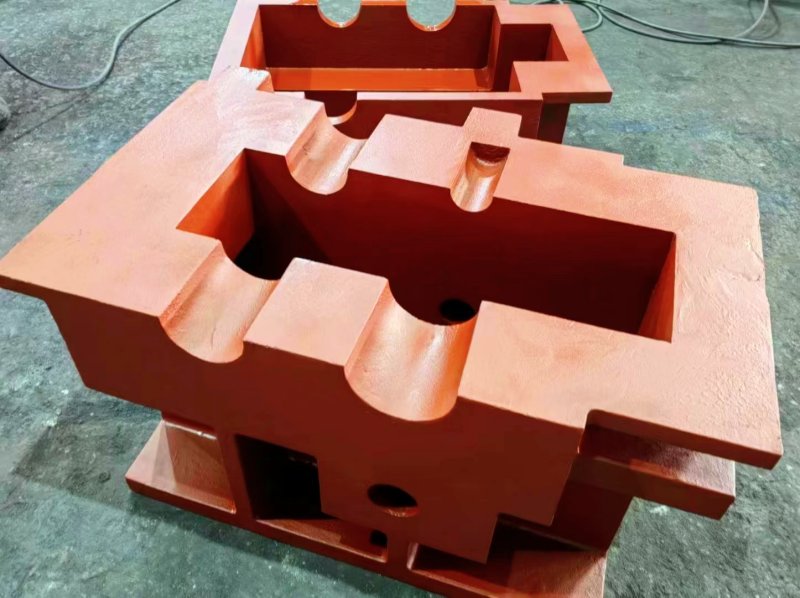
1.冲击韧度αk和硬度HRC低
2.脆性增加,抗磨性能不好
3.试片断口呈深灰色,敲击声发哑
原因分析:
1.在800~500℃冷却过程中冷却速度太低。奥氏体易于转变成索氏体、托氏体,索氏体量φ>40%
2.Si/Mn过大,Si量过高,共析转变温度区扩大,有利于形成索氏体
3.Mn量过高,或者Si/Mn太小,共析温度低下,奥氏体量过多(φ>50%)
防止方法:
1.控制冷却速度,ωSi3.4%~4.5%,ωMn5.5%~6.5%时,在750~500℃范围内。冷却速度应>20℃/min,控翻在18~36℃/min为宜。<18℃/min易产生索氏体。>36℃/min易形成奥氏体
2.根据铸件壁厚、铸型工艺等影响冷却速度的因素,选择合适的Si/Mn控制奥氏体转变成索氏体的数量。一般Si/Mn<0.6时即Si低Mn高,奥氏体量增多,Si/Mn>0.75时。即Si高Mn低,索氏体量增高,在冷却速度一定条件下,Si/Mn是控制奥氏体和索氏体t的重要手段
气孔、夹渣、缩孔特征:
1.铸件产生皮下气孔;
2.铸件内部有集中或分散气孔;
3.冒口下或周围出现集中或分散性气孔或缩孔且深浅不一;
4.铸件内或热节处产生密集蜂窝状气孔
原因分析:
1.出温度低于1400℃浇注温度过低
2.球化反应不充分,搅拌扒渣不够
3.渣气孔层取样分析结果(质量分数)如下:C4.98%,Mn4.67%,P0.088%,S0.128%,RExOy:0.663%, Mg0.203%。
分析表明:渣气孔主要是稀土镁的氧化物和石墨,当铁液温度低或浇注温度过低,此类夹渣不易排出
防止方法:
1.提高出铁温度,出铁槽中铁液温度应>1450℃
2.采用半封闭式浇注系统直浇道断面:横浇道断面:溢流口:内浇道=1.2:2:1=1.4。直浇道>溢流口有利于缓流。溢流口<横浇道有利于撇渣。内浇道溢流口有利于排气
3.炉前球化处理后,加人冰晶石(NaAlF2)。它易与MgS化合成低溶点易凝聚的MgF2、Na2S、NaO等化合物,从溶渣中排出。加入冰晶石后应静置,有益于上述反应充分进行
4.金属型需预热至200~300℃时浇注,刷涂料要及时烤干。湿砂造型时型砂水分应<4%(质量分教)
5.厚大铸件浇注应采用一快、二慢、三冲。中小件采用一快、二慢的浇注方法。