工艺在铸件生产过程中占有十分重要的地位,它直接影响铸件的质量水平、生产成本、生产效率及环境污染程度。砂型铸造方法可分为物理硬化造型方法和化学造型方法两大类。物理硬化造型方法主要有粘土砂型、实型铸造、V法造型法、冷冻造型法等。其中粘土砂型又分为湿型、干型和表干型。实型造型和V法造型法属于无粘结剂方法(干砂),采用负压成型。冷冻造型法则以水为粘结剂。化学造型方法主要有:水玻璃砂型、树脂砂型等。它们又都可分为加热硬化、自硬、吹气硬化等三种。水玻璃为无机粘结剂,树脂为有机粘结剂,选择砂型造型工艺时,应遵循以下几项原则:
1.应能保证铸件质量要求
表1~3列出了砂型铸造各类合金铸件的质量公差、尺寸公差和表面粗糙度范围。
表1 砂型铸造的铸件质量公差等级/MT
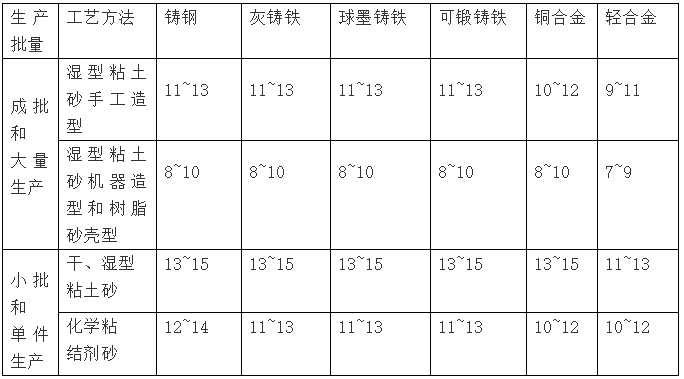
表2 砂型铸造的铸件尺寸公差等级/CT
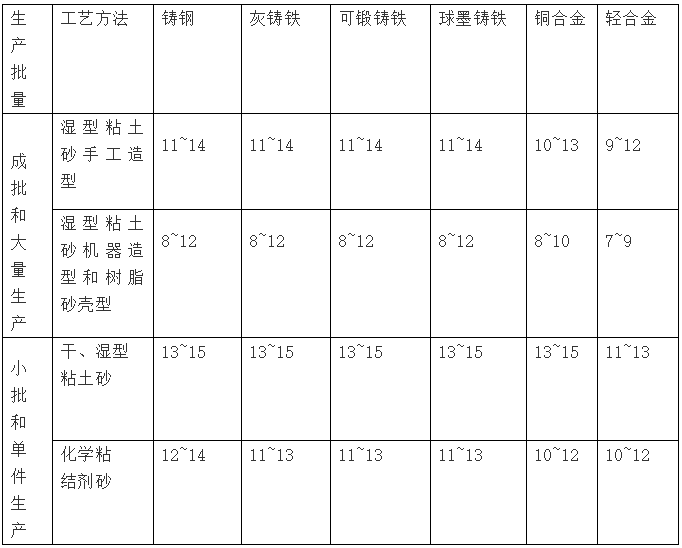
表3 砂型铸造各类合金铸件的表面粗糙度范围
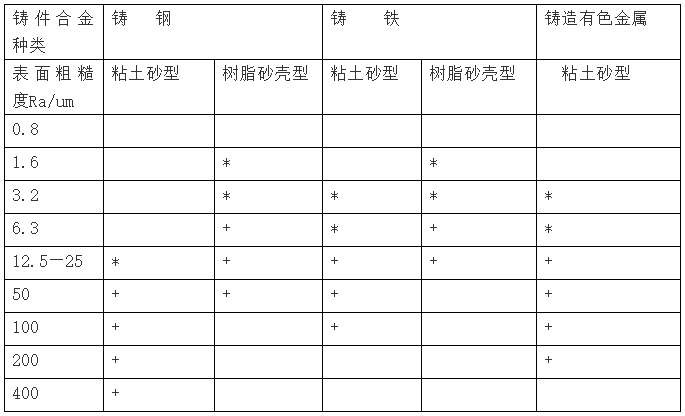
注:“+”为可以达到的粗糙度,“*”为采取特殊措施后方能达到的粗糙度。
目前广泛应用的造型工艺主要有粘土湿型砂工艺、CO2吹气硬化水玻璃砂工艺、有机酯自硬水玻璃砂工艺、酸自硬呋喃树脂砂工艺等。近年来,酯硬化酚醛树脂自硬砂造型工艺也得到了一定程度的推广应用。这些造型工艺的特点、对铸件质量的影响和适用范围分别简介如下:
(1)粘土湿型砂工艺
粘土湿型砂工艺的优点是:
①所用原材料价格便宜,来源丰富。
②造型方便,砂型不必烘干,铸型生产周期短,效率高,易于实现大批量生产。
③回用砂中未脱水失效的膨润土与水混合后即能恢复强度,旧砂回用性好,回用设备投资少。
④经过长期应用,已经发展了一系列造型设备。
⑤一般造型所生产铸件的尺寸精度不亚于化学自硬砂,射压造型、气冲造型和静压造型等高压造型方法所生产的铸件尺寸精度可与熔模铸造相媲美。
粘土湿型砂不同机器造型方法所生产的铸件尺寸精度和表面粗糙度见表4。
表4 粘土湿型砂不同造型方法的铸件尺寸精度和表面粗糙度
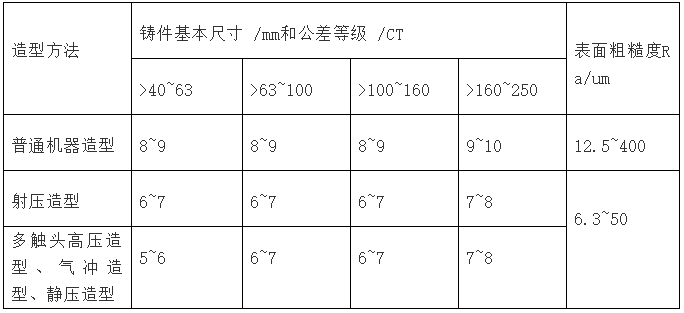
由于上述优点,粘土湿型砂工艺在小型铸件特别是汽车、发动机、纺织机等各种大规模生产的铸铁件上得到了广泛的应用,其所占比例居各种铸型之首。但是,粘土湿砂型在浇注时,砂型表面产生水分的汽化和迁移,使铸件容易产生气孔、夹砂、砂眼、胀砂、粘砂等缺陷。
(2)CO2吹气硬化水玻璃砂工艺
普通CO2吹气硬化水玻璃砂工艺是水玻璃粘结剂领域里应用最早的一种快速成型工艺。
其优点主要有:
①设备简单,操作方便,使用灵活。
②粘结剂无毒无味,成本低廉。
③砂型高温退让性好,铸件的收缩应力小。
④粘结剂系统不含S、P、N,铸件表面无增硫现象。
CO2吹气硬化水玻璃砂工艺在国内外大多数的铸钢件生产中得到了广泛的应用,主要用于中、小型铸钢件生产。但是,CO2吹气硬化水玻璃砂工艺的缺点也非常明显:
①砂型(芯)强度低,水玻璃加入量高。
②含水量大,易吸潮,冬季硬透性差。
③砂型(芯)溃散性差,旧砂再生困难,大量旧砂被废弃。
过去由于溃散性和旧砂回用问题未很好解决,在一定程度上影响了水玻璃砂的扩大应用。近年来,人们对于水玻璃的基本组成和“老化”现象实质的认识深化和新型硬化工艺(如真空置换CO2气体硬化水玻璃砂工艺)等两方面均取得了突破性进展,在型芯砂保持足够的工艺强度的条件下,采用低含量泥量的优质天然硅砂,水玻璃加入量可降至4.0%,从而使水玻璃砂长期存在的溃散性差、旧砂不能回用问题地,得到了较好的解决。水玻璃旧砂再生成套设备也趋于成熟,水玻璃砂出现了良好的发展势头。
(3)有机酯自硬水玻璃砂工艺
有机酯自硬水玻璃砂在铸钢方面应用十分广泛,在铸铁方面也有一定的应用。这种硬化工艺的主要优点是:
①型砂具有很高的强度,水玻璃加入量可低至2.5-3.5%。
②砂型(芯)溃散性较好,旧砂干法再生回用率≥80%。
③砂型热塑性好,发气量低,可克服呋喃树脂砂生产铸钢件时易出现的裂纹、气孔等缺陷,铸件质量和尺寸精度可与树脂砂相媲美。
④在所有自硬砂工艺中生产成本最低,劳动条件好。
该硬化工艺尚存在以下不足:型芯砂硬化速度慢,脆性大,流动性较差。
(4) 酸自硬呋喃树脂砂工艺
酸自硬呋喃树脂砂、有机酯自硬水玻璃砂分别是有机粘结剂化学自硬砂和无机粘结剂化学自硬砂的典型代表,化学自硬砂工艺的共同特点是:
①砂型硬化后起模,因此型砂不需要高的湿强度,型砂流动性好,砂型强度高,变形小,工装简化,造型简单,砂型不必烘干,铸件尺寸精度显著提高,可以达到CT8~10级,铸件缺陷也较少。
②化学硬化砂一般都采用液态的能够自硬的粘结剂。因此,它对原砂的质量要求较高,以尽量减少粘结剂的加入量。
③由于粘结剂的硬化属不可逆的化学反应,不能像粘土砂那样简单地加水重新回用,大批量使用时必须要有比较完善的旧砂再生系统。
④模型结构和表面质量等方面的要求较高,以便脱模。
自硬砂工艺主要适用于大型铸件小批或批量生产,与粘土湿型砂工艺不存在竞争或替代关系。
酸自硬呋喃树脂砂工艺是在铸铁方面应用比较广泛的一种自硬砂工艺,其突出优点是砂型(芯)溃散性好,旧砂再生回用率高。
铸造生产中所使用的呋喃树脂都需要经过脲醛改性,并根据改性后树脂的含氮量分别应用于有色合金、灰铸铁、球墨铸铁和铸钢等方面。
酸自硬呋喃树脂工艺的缺点是:
①树脂粘结剂和固化剂高温分解后所产生的N、S、P等气体会使球铁铸件和铸钢件表面严重渗硫,产生气孔和裂纹等缺陷。
②砂型高温热膨胀率大,产生的热应力大,高温退让性差,铸件的收缩应力大,铸件容易出现裂纹和毛刺。
③树脂粘结剂价格较贵,而且分解后所产生的呋喃环对人体健康十分有害。
(5)酯硬化酚醛树脂自硬砂
酯硬化酚醛树脂自硬砂工艺是英国波顿公司开发的,称为a-set工艺,于1981年获得专利,1984年已广泛地应用于欧洲,最先用于铸钢生产,现已扩大到铸铁和非铁合金铸件。
此种酚醛树脂的碱性较强,PH值为11-13.5。树脂中含有机溶剂,闪点低,易燃,而且能溶于水,保存期短,在20℃下可存放6个月,30℃下为2-3个月,40℃下仅为1-2个月。
此种自硬砂的硬化剂是有机酯,可根据硬化速度的要求选用。硬化剂用量大约是树脂的20~30%(质量分数),而酚醛树脂加入量为原砂的1.5~2.5%。其混砂工艺与酸自硬呋喃树脂相同。砂温通常控制在20~30%,型(芯)砂可使用时间为5~30min,脱模时间为15~60min。
酯硬化酚醛树脂自硬砂的主要特点有:
①在硬化剂作用下只发生部分反应,铸型或型芯硬化后有一定的热塑性,浇注金属后还有一短暂的、因受热而完全硬化的过程。这也是与酸自硬呋喃树脂砂的不同之处。因此,用此工艺制成的铸型(芯),硬化后强度并不很高,抗压强度只有2~4MPa,但是,由于浇注初期还将进一步硬化,铸型的尺寸稳定性和热稳定性都好,制得的铸件尺寸精度高,表面质量好。
②由于不含N、P、S,所以特别适合于铸钢件、球墨铸铁件生产。
③不会产生脉纹毛刺缺陷。其它自硬树脂铸型,在浇注和凝固过程中,在铸型/金属界面会出现裂纹。而酯硬化酚醛树脂自硬砂在浇注和凝固过程中,表层出现可避免开裂的短暂的热塑性阶段,因而可得到无脉毛刺纹缺陷的光洁铸件。
④碱性酚醛树脂对原砂的适应性广,不仅适用于硅砂,也适用于需酸值高的镁砂、镁橄榄石砂、铬铁矿砂等特种砂。
2.应与生产批量相适应
大批量生产时,应优先考虑机械化、自动化的粘土湿型砂造型生产线和树脂砂制芯生产线。对于粘土湿型砂铸造小型铸件,可以采用水平分型或垂直分型的无箱高压造型生产线,造型生产效率高,占地面积也小;对于中件(大于10kg),可选用各种有箱高压造型生产线,气冲造型线,以适应快速、高精度造型生产线的要求。老式的震击式或震压式造型机生产线生产率低,工人劳动强度大,噪声大,不适应大量生产的要求,应逐步淘汰。
中等批量生产时,可以考虑应用树脂自硬砂、CO2吹气硬化水玻璃砂、真空置换吹气硬化水玻璃砂造型和造芯。
单件小批量生产时,手工造型仍是重要的方法。手工造型能适应各种复杂的要求,比较灵活,不要求很多工艺装备,可以应用树脂自硬砂型、CO2吹气硬化水玻璃砂型、真空置换吹气硬化水玻璃砂型、有机酯水玻璃自硬砂型、粘土干型及水泥砂型等。对于单件生产的重型铸件,采用地坑造型法成本低,投产快。
批量生产或长期生产的定型产品采用多箱造型、劈箱造型法比较适宜,虽然模具、砂箱等初期投资高,但可从节约造型工时,提高产品质量方面得到补偿。
3.应适应企业自身条件
不同企业的生产条件(包括设备、场地、员工素质等)、生产习惯、所积累的经验各不一样,应该根据这些条件考虑适合采用什么造型方法。适用的就是最好的。当前各种工艺技术竞相发展,每项技术都有其优点,也都有一定的局限性和适用范围。先进的、技术含量高的工艺并不一定是适用的。根据企业自身条件选用技术上适用、经济上合理的工艺,注重技术与经济的结合,才能作出切合实际的选择。
例如:生产大型机床床身等铸件时,可采用组芯造型法,不制作模样和砂箱,在地坑中组芯;而另外的工厂则采用砂箱造型法,制作模样。
4.要兼顾铸件的质量和成本
各种铸造工艺所获得的铸件质量不同,初期投资和生产效率也不一致,最终的经济效益也有差异。因此,要做到多、快、好、省,就应当兼顾到各个方面。应对所选用的铸造方法进行成本估算,以保证经济效率和铸件质量的双重要求。
几种常用的化学硬化砂的成分分析列于表5,它们的工艺性能对比情况列于表6,从质量和成本的角度综合考虑,应该更加注意水玻璃自硬砂的发展。
表5 几种自硬砂在旧砂再生回用时的型(芯)砂成本分析(配制1t型砂所需费用)
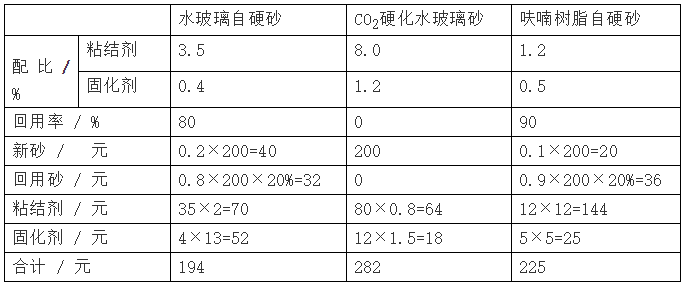
注:①再生砂的成本为新砂的20%;每吨砂耗用CO2气体12Kg。
表6 几种化学硬化砂的工艺性能对比

5.要重视造型工艺的环境保护特性
铸造生产历来以环境污染严重而著称,其污染形式主要是由钢铁熔化和造型材料带来的空气污染和废渣污染,其中由造型材料带来的空气污染和废渣污染最为严重。
根据统计生产1t铸件需耗约1t新砂,同时废弃约1t旧砂。目前我国年生产铸件约2800万吨,年排放的旧砂量也约2800万吨,这不仅占去了大量的自然资源,而且造成了严重的环境污染。要消减旧砂排放量,必须尽量采用旧砂回用率高的铸造工艺,粘土湿型砂、树脂砂工艺等。
但是,粘土湿型砂存在较大的粉尘污染和煤粉黑色污染,煤粉在浇注过程中的燃烧和分解产生的有害气体还导致严重的空气污染;而树脂砂生产现场的空气中游离着许多有机废气(SO2、甲醛、苯、甲基等),浇注后会产生大量有害气体,对人类的健康非常有害。水玻璃砂由硅砂、无机水玻璃粘结剂等组成,采用CO2气体或有机酯(如乙二醇二乙酸脂等)作固化剂,生产环境友好,不产生有害气体。与粘土砂和树脂砂相比,水玻璃砂工艺是最可能实现绿色清洁铸造生产的造型制芯工艺。
6. 结 论
铸造的产品多种多样,造型的工艺也是千变万化。我们在选择自己产品的生产工艺时必须要有科学的态度,要从实际出发,要根据铸件的材质、结构特点和质量要求进行综合考虑。
覆膜砂铸造砂眼_气孔_粘砂_的等缺陷原因及解决方法
传统的铸造涂料只是在铸件和铸型中间起到阻挡隔离作用,达到防粘砂目的,但普通铸造涂料高温下由于附着力差、强度低、耐火差、发气量大,容易造成铸件产生粘砂、砂眼、气孔、碳渣等缺陷。铸件粘砂是因为涂料没有有效起到阻挡隔离作用,或涂料与高温金属液体发生化学反映。
1.涂料附着力差:填砂震动时造成涂料剥落,引起铸件粘砂,
2.涂料膨胀系数大:与高温金属液体接触时涂料受热体积膨胀脱离铸型导致铸件粘砂。
3.高温液体金属被氧化与涂料和铸型发生化学反应生成金属氧化物,对涂料和型砂都有极强的粘结性,能够将型砂牢固粘附在铸件表面上形成一系列的低熔点化合物〔在铸件厚壁及转角处等,低熔点物更多,粘砂层更后),造成铸件粘砂,有时虽未产生粘砂,但在铸件表面粘附上一层难以清除的涂料,及产生粘灰。
铸件砂眼:
1.铸型内有掉入的砂子。
2,涂料强度低,耐火差,经不住高温金属液体的冲刷,型砂被卷入铸件。铸件气孔产生的原因很多,最常见的就是因为铸型中存在较多发气量大的物质,发气速度快,涂料或被砂透气性差,气体未及时排除所致。研制的新型铸造涂料是在传统铸造涂料基础上加以改进,调整,高温下不开裂,不脱落,强度高,并且能有效防止高温液体金属氧化,与铸型和高温液体金属接触过程中不起化学反应。同时能预防氮、硫、碳等气体的产生。从而彻底解决:铸件粘砂,铸件砂眼,铸件粗糙,铸件气孔,铸件夹杂〔渣〕,球磨铁变异,铸钢渗硫裂纹,增碳缺陷等。
壳型铸造方法生产的铸件尺寸精度高,表面粗糙度低,可节省大量的金属切削消耗和机加工工时,并且由于型砂用量和造型方法的改变,为铸造生产的机械化和自动化创造了条件,因而特别适用于生产批量较大、精度要求较高的铸件。
用热芯盒覆膜砂工艺做壳形铸造不锈钢铸件跟铸铁的工艺区别在于覆膜砂工艺做壳形铸造不锈钢铸件跟铸铁的工艺区别是原砂SiO2含量不同,铸铁为SiO2含量90%,铸钢为大于95%。壳形铸造铸件精度低于腊模精铸。
1.应能保证铸件质量要求
表1~3列出了砂型铸造各类合金铸件的质量公差、尺寸公差和表面粗糙度范围。
表1 砂型铸造的铸件质量公差等级/MT
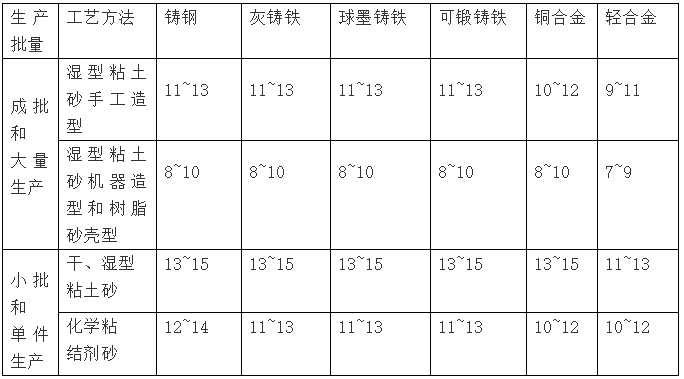
表2 砂型铸造的铸件尺寸公差等级/CT
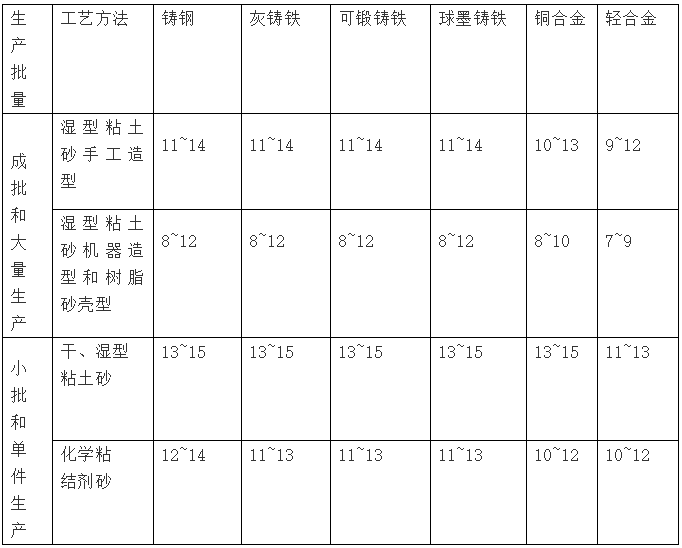
表3 砂型铸造各类合金铸件的表面粗糙度范围
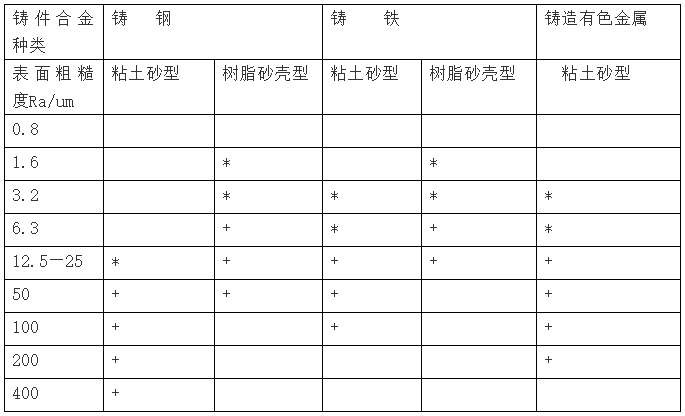
注:“+”为可以达到的粗糙度,“*”为采取特殊措施后方能达到的粗糙度。
目前广泛应用的造型工艺主要有粘土湿型砂工艺、CO2吹气硬化水玻璃砂工艺、有机酯自硬水玻璃砂工艺、酸自硬呋喃树脂砂工艺等。近年来,酯硬化酚醛树脂自硬砂造型工艺也得到了一定程度的推广应用。这些造型工艺的特点、对铸件质量的影响和适用范围分别简介如下:
(1)粘土湿型砂工艺
粘土湿型砂工艺的优点是:
①所用原材料价格便宜,来源丰富。
②造型方便,砂型不必烘干,铸型生产周期短,效率高,易于实现大批量生产。
③回用砂中未脱水失效的膨润土与水混合后即能恢复强度,旧砂回用性好,回用设备投资少。
④经过长期应用,已经发展了一系列造型设备。
⑤一般造型所生产铸件的尺寸精度不亚于化学自硬砂,射压造型、气冲造型和静压造型等高压造型方法所生产的铸件尺寸精度可与熔模铸造相媲美。
粘土湿型砂不同机器造型方法所生产的铸件尺寸精度和表面粗糙度见表4。
表4 粘土湿型砂不同造型方法的铸件尺寸精度和表面粗糙度
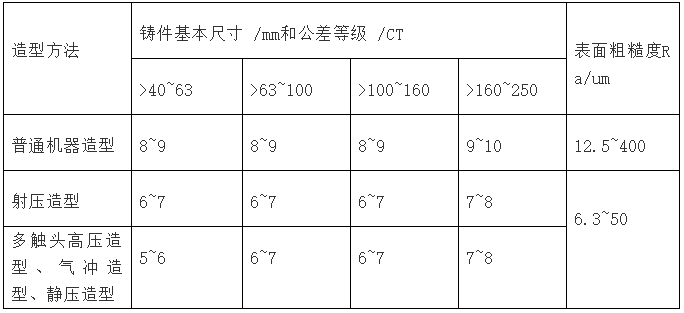
由于上述优点,粘土湿型砂工艺在小型铸件特别是汽车、发动机、纺织机等各种大规模生产的铸铁件上得到了广泛的应用,其所占比例居各种铸型之首。但是,粘土湿砂型在浇注时,砂型表面产生水分的汽化和迁移,使铸件容易产生气孔、夹砂、砂眼、胀砂、粘砂等缺陷。
(2)CO2吹气硬化水玻璃砂工艺
普通CO2吹气硬化水玻璃砂工艺是水玻璃粘结剂领域里应用最早的一种快速成型工艺。
其优点主要有:
①设备简单,操作方便,使用灵活。
②粘结剂无毒无味,成本低廉。
③砂型高温退让性好,铸件的收缩应力小。
④粘结剂系统不含S、P、N,铸件表面无增硫现象。
CO2吹气硬化水玻璃砂工艺在国内外大多数的铸钢件生产中得到了广泛的应用,主要用于中、小型铸钢件生产。但是,CO2吹气硬化水玻璃砂工艺的缺点也非常明显:
①砂型(芯)强度低,水玻璃加入量高。
②含水量大,易吸潮,冬季硬透性差。
③砂型(芯)溃散性差,旧砂再生困难,大量旧砂被废弃。
过去由于溃散性和旧砂回用问题未很好解决,在一定程度上影响了水玻璃砂的扩大应用。近年来,人们对于水玻璃的基本组成和“老化”现象实质的认识深化和新型硬化工艺(如真空置换CO2气体硬化水玻璃砂工艺)等两方面均取得了突破性进展,在型芯砂保持足够的工艺强度的条件下,采用低含量泥量的优质天然硅砂,水玻璃加入量可降至4.0%,从而使水玻璃砂长期存在的溃散性差、旧砂不能回用问题地,得到了较好的解决。水玻璃旧砂再生成套设备也趋于成熟,水玻璃砂出现了良好的发展势头。
(3)有机酯自硬水玻璃砂工艺
有机酯自硬水玻璃砂在铸钢方面应用十分广泛,在铸铁方面也有一定的应用。这种硬化工艺的主要优点是:
①型砂具有很高的强度,水玻璃加入量可低至2.5-3.5%。
②砂型(芯)溃散性较好,旧砂干法再生回用率≥80%。
③砂型热塑性好,发气量低,可克服呋喃树脂砂生产铸钢件时易出现的裂纹、气孔等缺陷,铸件质量和尺寸精度可与树脂砂相媲美。
④在所有自硬砂工艺中生产成本最低,劳动条件好。
该硬化工艺尚存在以下不足:型芯砂硬化速度慢,脆性大,流动性较差。
(4) 酸自硬呋喃树脂砂工艺
酸自硬呋喃树脂砂、有机酯自硬水玻璃砂分别是有机粘结剂化学自硬砂和无机粘结剂化学自硬砂的典型代表,化学自硬砂工艺的共同特点是:
①砂型硬化后起模,因此型砂不需要高的湿强度,型砂流动性好,砂型强度高,变形小,工装简化,造型简单,砂型不必烘干,铸件尺寸精度显著提高,可以达到CT8~10级,铸件缺陷也较少。
②化学硬化砂一般都采用液态的能够自硬的粘结剂。因此,它对原砂的质量要求较高,以尽量减少粘结剂的加入量。
③由于粘结剂的硬化属不可逆的化学反应,不能像粘土砂那样简单地加水重新回用,大批量使用时必须要有比较完善的旧砂再生系统。
④模型结构和表面质量等方面的要求较高,以便脱模。
自硬砂工艺主要适用于大型铸件小批或批量生产,与粘土湿型砂工艺不存在竞争或替代关系。
酸自硬呋喃树脂砂工艺是在铸铁方面应用比较广泛的一种自硬砂工艺,其突出优点是砂型(芯)溃散性好,旧砂再生回用率高。
铸造生产中所使用的呋喃树脂都需要经过脲醛改性,并根据改性后树脂的含氮量分别应用于有色合金、灰铸铁、球墨铸铁和铸钢等方面。
酸自硬呋喃树脂工艺的缺点是:
①树脂粘结剂和固化剂高温分解后所产生的N、S、P等气体会使球铁铸件和铸钢件表面严重渗硫,产生气孔和裂纹等缺陷。
②砂型高温热膨胀率大,产生的热应力大,高温退让性差,铸件的收缩应力大,铸件容易出现裂纹和毛刺。
③树脂粘结剂价格较贵,而且分解后所产生的呋喃环对人体健康十分有害。
(5)酯硬化酚醛树脂自硬砂
酯硬化酚醛树脂自硬砂工艺是英国波顿公司开发的,称为a-set工艺,于1981年获得专利,1984年已广泛地应用于欧洲,最先用于铸钢生产,现已扩大到铸铁和非铁合金铸件。
此种酚醛树脂的碱性较强,PH值为11-13.5。树脂中含有机溶剂,闪点低,易燃,而且能溶于水,保存期短,在20℃下可存放6个月,30℃下为2-3个月,40℃下仅为1-2个月。
此种自硬砂的硬化剂是有机酯,可根据硬化速度的要求选用。硬化剂用量大约是树脂的20~30%(质量分数),而酚醛树脂加入量为原砂的1.5~2.5%。其混砂工艺与酸自硬呋喃树脂相同。砂温通常控制在20~30%,型(芯)砂可使用时间为5~30min,脱模时间为15~60min。
酯硬化酚醛树脂自硬砂的主要特点有:
①在硬化剂作用下只发生部分反应,铸型或型芯硬化后有一定的热塑性,浇注金属后还有一短暂的、因受热而完全硬化的过程。这也是与酸自硬呋喃树脂砂的不同之处。因此,用此工艺制成的铸型(芯),硬化后强度并不很高,抗压强度只有2~4MPa,但是,由于浇注初期还将进一步硬化,铸型的尺寸稳定性和热稳定性都好,制得的铸件尺寸精度高,表面质量好。
②由于不含N、P、S,所以特别适合于铸钢件、球墨铸铁件生产。
③不会产生脉纹毛刺缺陷。其它自硬树脂铸型,在浇注和凝固过程中,在铸型/金属界面会出现裂纹。而酯硬化酚醛树脂自硬砂在浇注和凝固过程中,表层出现可避免开裂的短暂的热塑性阶段,因而可得到无脉毛刺纹缺陷的光洁铸件。
④碱性酚醛树脂对原砂的适应性广,不仅适用于硅砂,也适用于需酸值高的镁砂、镁橄榄石砂、铬铁矿砂等特种砂。
2.应与生产批量相适应
大批量生产时,应优先考虑机械化、自动化的粘土湿型砂造型生产线和树脂砂制芯生产线。对于粘土湿型砂铸造小型铸件,可以采用水平分型或垂直分型的无箱高压造型生产线,造型生产效率高,占地面积也小;对于中件(大于10kg),可选用各种有箱高压造型生产线,气冲造型线,以适应快速、高精度造型生产线的要求。老式的震击式或震压式造型机生产线生产率低,工人劳动强度大,噪声大,不适应大量生产的要求,应逐步淘汰。
中等批量生产时,可以考虑应用树脂自硬砂、CO2吹气硬化水玻璃砂、真空置换吹气硬化水玻璃砂造型和造芯。
单件小批量生产时,手工造型仍是重要的方法。手工造型能适应各种复杂的要求,比较灵活,不要求很多工艺装备,可以应用树脂自硬砂型、CO2吹气硬化水玻璃砂型、真空置换吹气硬化水玻璃砂型、有机酯水玻璃自硬砂型、粘土干型及水泥砂型等。对于单件生产的重型铸件,采用地坑造型法成本低,投产快。
批量生产或长期生产的定型产品采用多箱造型、劈箱造型法比较适宜,虽然模具、砂箱等初期投资高,但可从节约造型工时,提高产品质量方面得到补偿。
3.应适应企业自身条件
不同企业的生产条件(包括设备、场地、员工素质等)、生产习惯、所积累的经验各不一样,应该根据这些条件考虑适合采用什么造型方法。适用的就是最好的。当前各种工艺技术竞相发展,每项技术都有其优点,也都有一定的局限性和适用范围。先进的、技术含量高的工艺并不一定是适用的。根据企业自身条件选用技术上适用、经济上合理的工艺,注重技术与经济的结合,才能作出切合实际的选择。
例如:生产大型机床床身等铸件时,可采用组芯造型法,不制作模样和砂箱,在地坑中组芯;而另外的工厂则采用砂箱造型法,制作模样。
4.要兼顾铸件的质量和成本
各种铸造工艺所获得的铸件质量不同,初期投资和生产效率也不一致,最终的经济效益也有差异。因此,要做到多、快、好、省,就应当兼顾到各个方面。应对所选用的铸造方法进行成本估算,以保证经济效率和铸件质量的双重要求。
几种常用的化学硬化砂的成分分析列于表5,它们的工艺性能对比情况列于表6,从质量和成本的角度综合考虑,应该更加注意水玻璃自硬砂的发展。
表5 几种自硬砂在旧砂再生回用时的型(芯)砂成本分析(配制1t型砂所需费用)
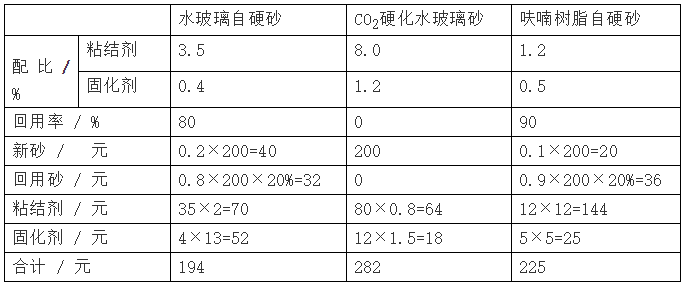
注:①再生砂的成本为新砂的20%;每吨砂耗用CO2气体12Kg。
表6 几种化学硬化砂的工艺性能对比

5.要重视造型工艺的环境保护特性
铸造生产历来以环境污染严重而著称,其污染形式主要是由钢铁熔化和造型材料带来的空气污染和废渣污染,其中由造型材料带来的空气污染和废渣污染最为严重。
根据统计生产1t铸件需耗约1t新砂,同时废弃约1t旧砂。目前我国年生产铸件约2800万吨,年排放的旧砂量也约2800万吨,这不仅占去了大量的自然资源,而且造成了严重的环境污染。要消减旧砂排放量,必须尽量采用旧砂回用率高的铸造工艺,粘土湿型砂、树脂砂工艺等。
但是,粘土湿型砂存在较大的粉尘污染和煤粉黑色污染,煤粉在浇注过程中的燃烧和分解产生的有害气体还导致严重的空气污染;而树脂砂生产现场的空气中游离着许多有机废气(SO2、甲醛、苯、甲基等),浇注后会产生大量有害气体,对人类的健康非常有害。水玻璃砂由硅砂、无机水玻璃粘结剂等组成,采用CO2气体或有机酯(如乙二醇二乙酸脂等)作固化剂,生产环境友好,不产生有害气体。与粘土砂和树脂砂相比,水玻璃砂工艺是最可能实现绿色清洁铸造生产的造型制芯工艺。
6. 结 论
铸造的产品多种多样,造型的工艺也是千变万化。我们在选择自己产品的生产工艺时必须要有科学的态度,要从实际出发,要根据铸件的材质、结构特点和质量要求进行综合考虑。
覆膜砂铸造砂眼_气孔_粘砂_的等缺陷原因及解决方法
传统的铸造涂料只是在铸件和铸型中间起到阻挡隔离作用,达到防粘砂目的,但普通铸造涂料高温下由于附着力差、强度低、耐火差、发气量大,容易造成铸件产生粘砂、砂眼、气孔、碳渣等缺陷。铸件粘砂是因为涂料没有有效起到阻挡隔离作用,或涂料与高温金属液体发生化学反映。
1.涂料附着力差:填砂震动时造成涂料剥落,引起铸件粘砂,
2.涂料膨胀系数大:与高温金属液体接触时涂料受热体积膨胀脱离铸型导致铸件粘砂。
3.高温液体金属被氧化与涂料和铸型发生化学反应生成金属氧化物,对涂料和型砂都有极强的粘结性,能够将型砂牢固粘附在铸件表面上形成一系列的低熔点化合物〔在铸件厚壁及转角处等,低熔点物更多,粘砂层更后),造成铸件粘砂,有时虽未产生粘砂,但在铸件表面粘附上一层难以清除的涂料,及产生粘灰。
铸件砂眼:
1.铸型内有掉入的砂子。
2,涂料强度低,耐火差,经不住高温金属液体的冲刷,型砂被卷入铸件。铸件气孔产生的原因很多,最常见的就是因为铸型中存在较多发气量大的物质,发气速度快,涂料或被砂透气性差,气体未及时排除所致。研制的新型铸造涂料是在传统铸造涂料基础上加以改进,调整,高温下不开裂,不脱落,强度高,并且能有效防止高温液体金属氧化,与铸型和高温液体金属接触过程中不起化学反应。同时能预防氮、硫、碳等气体的产生。从而彻底解决:铸件粘砂,铸件砂眼,铸件粗糙,铸件气孔,铸件夹杂〔渣〕,球磨铁变异,铸钢渗硫裂纹,增碳缺陷等。
壳型铸造方法生产的铸件尺寸精度高,表面粗糙度低,可节省大量的金属切削消耗和机加工工时,并且由于型砂用量和造型方法的改变,为铸造生产的机械化和自动化创造了条件,因而特别适用于生产批量较大、精度要求较高的铸件。
用热芯盒覆膜砂工艺做壳形铸造不锈钢铸件跟铸铁的工艺区别在于覆膜砂工艺做壳形铸造不锈钢铸件跟铸铁的工艺区别是原砂SiO2含量不同,铸铁为SiO2含量90%,铸钢为大于95%。壳形铸造铸件精度低于腊模精铸。