铸造生产中所使用的型砂,有的是由回用砂加适量的新砂、粘土和水经混合均匀配制成的,有的全部是由新的材料配制成的。型砂的配制包括三个方面,即原材料的准备、型砂的混制和将混制好的型砂调匀及松砂等工艺环节。为了确保新砂质量,所有的原材料都须根据技术要求经验收合格后才能使用。为此,在配砂前都必须进行加工准备。
(1)粘土
刚开采的粘土往往含有较多的水分具多为块状,因此使用前必须烘干、破碎并磨成粘土粉,主要由专门的工厂进行加工,包装万袋供应。有的工厂事先将膨润土或粘土与煤粉按比例制成粘土—煤粉粉浆,使粘土充分吸水膨胀,混砂时与原砂一起加入到混砂机里混合均匀。这种做法可简化混砂操作,便于运输,改善劳动条件,提高型砂质量。但必须严格控制粉浆的含水量,否则会影响型砂性能。
(2)新砂
新砂在采购、运输过程中常混有草根、煤屑及泥块等杂物,同时含有一定数量的分分。潮湿的原砂不易过筛,配砂时不便于控制型砂的水分。因此,除含水量低、用于手工造型的湿型砂可直接配制外,新砂在使用前必须进行烘干和过筛。新砂的烘干用立式或卧式烘干滚筒,也可采用气流烘干的办法。常用的筛砂设备有手工筛、滚筒筛和振动筛等。
(3)旧砂
为了节省造型材料,降低铸件成本,旧砂应回用。旧砂在型砂所占比例很大,它对型砂的成分及性能有着很大的影响。旧砂中常混有各种杂物,如钉子、铁块和砂团等,在回用前必须进行处理,包括将砂块粉碎,用电磁分离器除去其中的铁质杂物然后过筛,必要时进行冷却。
在机械化程度高的铸造车间,型砂需求量大,周转速度很快,往往旧砂的温度还比较高,有的回用砂温度高达60摄氏度以上,如果采用这种型砂造型,容易粘附模样、芯盒及砂斗。由于型砂温度过高,会使水分蒸发太快,使型砂性能不稳定,同时影响铸件表面质量,影响造型劳动生产率。因此必须在铸件落砂、旧砂过筛、运输和混砂过程中加强通风冷却,降低型砂温度。
(4)附加物
煤粉、硼配、氟化物和硫黄等附加物都必须粉碎、过筛后再使用。
(5) 混砂
混砂的任务是将各种原材料混合均匀,使粘结剂包覆在砂粒表面上,混砂的质量主要取决于混砂工艺和混砂机的形式。
01、混砂机的形式。生产中常用的混砂设备有辗轮式、摆轮式和叶片式混砂机。
辗轮式混砂机除有搅拌作用外,还有辗压搓揉作用,型砂的质量较好,但生产效率较低,主要用来混制面砂和单一砂。摆式混砂机的生产效率比辗轮式高几倍,且可边混砂边鼓风冷却,并有一定的搓揉作用,但型砂质量不如辗轮式混砂好,主要用于机械化程度高、生产量大的铸造车间混制单一砂及背砂。叶片式混砂机是一种连续作业式的设备,各种原是否无误混砂机的一端进入,混好的型砂从混砂机的另一端出来,生产效率高。叶片式混砂机有混合作用,但搓揉作用很差,主要用于混制背砂和粘土含量低的单一砂。
02、加料顺序与混砂时间。混制粘土型砂的加顺序一般是先加回用砂、原砂、粘土粉和附加物等干料,干混均匀后再加水湿混,均匀后即可使用。
为了使各种原材料混合均匀,混砂时间不能太短,否则影响型砂性能,但混砂时间也不宜过长。否则将使型砂温度升高,水分过多挥发,型砂结成块状,性能变坏且生产效率低。混砂时间主要根据混砂机的形式、粘土含量、对型砂性能要求等来决定。一般来说,粘土含量越多,对型砂质量要求越高,混砂时间越长。采用辗轮式混砂机混制面砂时,混砂时间一般为6—12分钟,北砂为3—6分钟,单一砂为4—8分钟。
如果型砂中含有渣油液以及其他液态粘结剂,则应先加水将型砂混合均匀后再加入油类粘结剂。这种先加干粉后加水的混砂加料顺序存在的缺点是,在混砂机的辗盘边缘遗留一些粉料,这些粉料吸水后粘附在混砂机壁上,直到混辗后期或卸砂时才脱落下来,使型砂里含有混合不均匀的粘土或煤粉团块,恶化了型砂性能。同时干混时粉尘飞扬,劳动条件差。因此,有的工厂采用先在回用砂里加水混合,然后加粘土及煤粉混合均匀,最后再加少量水分调节到所需要的含水量的混砂工艺。试验结果表明,后面这种加料顺序可缩短混砂时间,提高型砂质量,改善劳动条件。
(6)调匀
型砂的调匀又称回性、渗匀,是指将混好的型砂在不失去水分的条件下放置一段时间,使水分均匀渗透到型砂中,让粘土充分吸水膨胀,以提高型砂的强度和透气性等性能。调匀时间主要根据粘土种类及加入量而定。型砂中粘土含量越多,原砂的颗粒越细,调匀时间越长。调匀时间应适当,否则型砂性能难以满足要注。单一砂一般为2—3小时,面砂为4—5小时。机械化铸造厂间型砂调匀是在型砂调匀斗里进行,非机械化的手工造型车间是将混好的型砂堆放在轩间地面上,并用湿麻袋覆盖进行调匀。
型砂经混辗和调匀后会被压实,有的被压成团块。如果采用这种型砂直接造型,型砂的坚实度不均匀,透气性等性能差。因此,调匀后的型砂必须经松砂或过筛才能使用。在机械化的铸造车间一般采用圆棒式或叶片式松砂机进行松砂处理。在百机械化的手工造型车间,常用移动式松砂机或用筛孔为5—8毫米的筛子过筛。
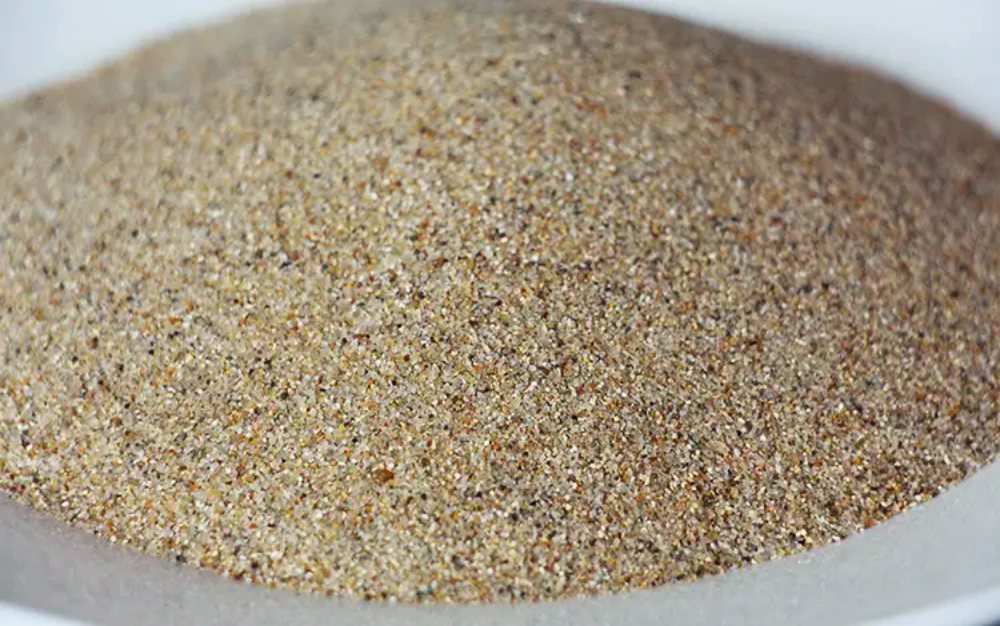
(1)粘土
刚开采的粘土往往含有较多的水分具多为块状,因此使用前必须烘干、破碎并磨成粘土粉,主要由专门的工厂进行加工,包装万袋供应。有的工厂事先将膨润土或粘土与煤粉按比例制成粘土—煤粉粉浆,使粘土充分吸水膨胀,混砂时与原砂一起加入到混砂机里混合均匀。这种做法可简化混砂操作,便于运输,改善劳动条件,提高型砂质量。但必须严格控制粉浆的含水量,否则会影响型砂性能。
(2)新砂
新砂在采购、运输过程中常混有草根、煤屑及泥块等杂物,同时含有一定数量的分分。潮湿的原砂不易过筛,配砂时不便于控制型砂的水分。因此,除含水量低、用于手工造型的湿型砂可直接配制外,新砂在使用前必须进行烘干和过筛。新砂的烘干用立式或卧式烘干滚筒,也可采用气流烘干的办法。常用的筛砂设备有手工筛、滚筒筛和振动筛等。
(3)旧砂
为了节省造型材料,降低铸件成本,旧砂应回用。旧砂在型砂所占比例很大,它对型砂的成分及性能有着很大的影响。旧砂中常混有各种杂物,如钉子、铁块和砂团等,在回用前必须进行处理,包括将砂块粉碎,用电磁分离器除去其中的铁质杂物然后过筛,必要时进行冷却。
在机械化程度高的铸造车间,型砂需求量大,周转速度很快,往往旧砂的温度还比较高,有的回用砂温度高达60摄氏度以上,如果采用这种型砂造型,容易粘附模样、芯盒及砂斗。由于型砂温度过高,会使水分蒸发太快,使型砂性能不稳定,同时影响铸件表面质量,影响造型劳动生产率。因此必须在铸件落砂、旧砂过筛、运输和混砂过程中加强通风冷却,降低型砂温度。
(4)附加物
煤粉、硼配、氟化物和硫黄等附加物都必须粉碎、过筛后再使用。
(5) 混砂
混砂的任务是将各种原材料混合均匀,使粘结剂包覆在砂粒表面上,混砂的质量主要取决于混砂工艺和混砂机的形式。
01、混砂机的形式。生产中常用的混砂设备有辗轮式、摆轮式和叶片式混砂机。
辗轮式混砂机除有搅拌作用外,还有辗压搓揉作用,型砂的质量较好,但生产效率较低,主要用来混制面砂和单一砂。摆式混砂机的生产效率比辗轮式高几倍,且可边混砂边鼓风冷却,并有一定的搓揉作用,但型砂质量不如辗轮式混砂好,主要用于机械化程度高、生产量大的铸造车间混制单一砂及背砂。叶片式混砂机是一种连续作业式的设备,各种原是否无误混砂机的一端进入,混好的型砂从混砂机的另一端出来,生产效率高。叶片式混砂机有混合作用,但搓揉作用很差,主要用于混制背砂和粘土含量低的单一砂。
02、加料顺序与混砂时间。混制粘土型砂的加顺序一般是先加回用砂、原砂、粘土粉和附加物等干料,干混均匀后再加水湿混,均匀后即可使用。
为了使各种原材料混合均匀,混砂时间不能太短,否则影响型砂性能,但混砂时间也不宜过长。否则将使型砂温度升高,水分过多挥发,型砂结成块状,性能变坏且生产效率低。混砂时间主要根据混砂机的形式、粘土含量、对型砂性能要求等来决定。一般来说,粘土含量越多,对型砂质量要求越高,混砂时间越长。采用辗轮式混砂机混制面砂时,混砂时间一般为6—12分钟,北砂为3—6分钟,单一砂为4—8分钟。
如果型砂中含有渣油液以及其他液态粘结剂,则应先加水将型砂混合均匀后再加入油类粘结剂。这种先加干粉后加水的混砂加料顺序存在的缺点是,在混砂机的辗盘边缘遗留一些粉料,这些粉料吸水后粘附在混砂机壁上,直到混辗后期或卸砂时才脱落下来,使型砂里含有混合不均匀的粘土或煤粉团块,恶化了型砂性能。同时干混时粉尘飞扬,劳动条件差。因此,有的工厂采用先在回用砂里加水混合,然后加粘土及煤粉混合均匀,最后再加少量水分调节到所需要的含水量的混砂工艺。试验结果表明,后面这种加料顺序可缩短混砂时间,提高型砂质量,改善劳动条件。
(6)调匀
型砂的调匀又称回性、渗匀,是指将混好的型砂在不失去水分的条件下放置一段时间,使水分均匀渗透到型砂中,让粘土充分吸水膨胀,以提高型砂的强度和透气性等性能。调匀时间主要根据粘土种类及加入量而定。型砂中粘土含量越多,原砂的颗粒越细,调匀时间越长。调匀时间应适当,否则型砂性能难以满足要注。单一砂一般为2—3小时,面砂为4—5小时。机械化铸造厂间型砂调匀是在型砂调匀斗里进行,非机械化的手工造型车间是将混好的型砂堆放在轩间地面上,并用湿麻袋覆盖进行调匀。
型砂经混辗和调匀后会被压实,有的被压成团块。如果采用这种型砂直接造型,型砂的坚实度不均匀,透气性等性能差。因此,调匀后的型砂必须经松砂或过筛才能使用。在机械化的铸造车间一般采用圆棒式或叶片式松砂机进行松砂处理。在百机械化的手工造型车间,常用移动式松砂机或用筛孔为5—8毫米的筛子过筛。