在现代铸造行业中,树脂砂铸造因其高精度、高强度和良好的表面质量等优点,逐渐成为生产复杂结构铸件的重要方法。本文将详细解析树脂砂铸造的工艺过程,帮助读者全面了解这一先进铸造技术的具体步骤和关键要点。
一、树脂砂铸造工艺概述
树脂砂铸造是利用热固性或冷固性树脂作为粘结剂,将石英砂颗粒粘结在一起形成铸型的一种铸造方法。它具有以下显著特点:
高强度:树脂砂铸型具有较高的强度和硬度,能够承受高温金属液的压力而不变形。
高精度:树脂砂铸型的尺寸精度高,能够生产出复杂形状和精密结构的铸件。
良好透气性:树脂砂铸型透气性能好,有利于气体排出,减少气孔等缺陷。
易于脱模:铸件冷却后,树脂砂铸型容易破碎脱落,便于清理和后续加工。
二、树脂砂铸造的工艺过程
(一)原材料准备
1、选择优质原材料
生铁和废钢:生铁是铸铁件的主要原料之一,其品质直接影响到铸铁件的质量。应选择含碳量适中、杂质少的优质生铁,以保证熔炼过程中金属液的纯净度。废钢作为补充材料,可以调节铸铁中的碳当量和其他合金元素含量。选用清洁、无油污、无锈蚀的废钢,有助于减少夹渣和气孔等缺陷。
合金添加剂:根据产品需求,适量添加锰、铬、镍等合金元素,以改善铸铁件的耐磨性、耐腐蚀性和强度等性能。
2、配料计算与混合
根据铸铁件的设计要求,精确计算各种原材料的比例,确保熔炼后的金属液化学成分符合标准。使用自动配料系统或人工称重方式将各组分均匀混合,避免因比例失调而导致质量问题。
(二)制芯与制模
1、制芯设备选择
冷芯盒制芯机:适用于中小型铸件的生产,采用冷固化树脂,具有生产效率高、成本低的特点。通过压缩空气吹入树脂砂,使其快速固化成型。
热芯盒制芯机:适用于大型铸件或复杂结构铸件的生产,采用热固化树脂,具有更高的强度和尺寸精度。通过加热芯盒使树脂砂迅速固化成型。
2、模具设计与制造
模具材料的选择直接影响到铸件的尺寸精度和表面质量。选用具有良好导热性和耐磨性的模具材料(如高铬合金钢),可以有效提高铸件的成型质量和使用寿命。
对于大型或复杂铸件,采用分段式或组合式模具结构,既能保证整体精度,又能降低制造难度。利用数控机床、3D打印等先进技术进行模具加工,可以显著提高模具的精度和一致性。
(三)熔炼与浇注
1、熔炼设备选择
感应电炉:广泛应用于中小型铸铁件生产。它通过电磁感应原理加热金属,具有升温快、温度均匀、能耗低等优点。
电阻炉:适合小批量、多品种铸铁件试制及科研实验。结构简单、操作方便,能够实现精准控温。
2、熔炼工艺控制
精确控制化学成分:通过光谱分析仪等设备实时监测金属液成分,及时调整配方,确保每一批次铸件的化学成分稳定一致。
优化熔炼温度和时间:合理的温度和时间设置对铸件的质量至关重要。过高的温度会导致合金元素烧损,影响铸件性能;而过低的温度则可能使金属液流动性不足,造成浇注困难。
3、浇注系统设计
浇道的设计直接影响到金属液的填充效果和铸件的内部质量。科学合理地布置浇道,可以使金属液平稳、均匀地流入型腔,减少气孔、缩松等缺陷。
根据铸件的具体形状和壁厚分布,选择合适的浇道形式(如直浇道、横浇道、内浇道等),并优化其尺寸和位置。
4、浇注速度控制
浇注速度过快或过慢都会影响铸件的质量。过快的速度容易引发冷隔、未完全融合等问题;而过慢的速度则可能导致铸件内部出现疏松、缩孔等缺陷。通过引入自动化控制系统,实现对浇注速度的精确控制,确保每一件铸件都能获得最佳的成型效果。
(四)冷却与凝固
1、冷却介质选择
冷却介质的选择对铸件的显微组织和力学性能有重要影响。根据铸件的具体需求,选择适当的冷却介质(如空气、水、油等),调节冷却速度,使铸件各部分冷却均匀一致。
对于需要快速冷却的铸件,可采用强制风冷或喷水冷却等方式,确保铸件内部组织转变良好,达到预期的硬度和强度。
2、控制凝固顺序
合理安排铸件的凝固顺序,可以有效防止缩孔、缩松等缺陷的产生。通过设置冷铁、冒口等辅助装置,引导金属液从厚大部位向薄壁处流动,实现定向凝固。
利用计算机模拟技术,提前预测铸件的凝固过程,优化冷铁和冒口的布置方案,确保铸件内部无缺陷。
(五)清理与后处理
1、去除表面杂质
使用砂轮、刮刀等工具清除铸件表面的氧化皮、油污、锈蚀等杂质,确保焊补面干净平整。
打磨坡口,根据缺陷的大小和形状,适当打磨出适当的坡口角度(一般为30°-45°),以增加焊接面积,提高焊补质量。
2、表面修整与抛光
使用砂轮、锉刀等工具对焊缝进行打磨,使其与铸件表面平滑过渡,保证外观美观和尺寸精度。
对有特殊要求的铸件,可进行抛光处理,提高表面光洁度,增强耐磨性和抗腐蚀能力。
3、检测与验收
在生产线上安装在线检测设备(如超声波探伤仪、磁粉探伤仪等),可以实时监控铸件的质量状况,及时发现潜在问题,避免不合格品流入下一道工序。
配备高精度的测量工具(如三坐标测量机、激光测距仪等),对铸件的尺寸精度进行严格把关。定期校准测量仪器,确保其准确性,避免因测量误差导致的质量问题。
(六)包装与运输
1、防潮防锈措施
在包装前,对铸件进行防潮防锈处理,如涂覆防锈油、包裹塑料薄膜等,确保铸件在运输过程中不会受到潮湿和氧化的影响。
2、安全包装与标识
选择合适的包装材料(如木箱、纸箱等),确保铸件在运输过程中不受损坏。同时,在包装上标明产品名称、规格型号、生产日期、厂家信息等,便于客户识别和管理。
三、总结
树脂砂铸造作为一种先进的铸造工艺,涵盖了从原材料准备到成品出炉的多个环节。每个步骤都需要严格把控,以确保最终产品的质量和性能。通过对原材料选择、制芯与制模、熔炼与浇注、冷却与凝固、清理与后处理以及包装与运输等环节的深入理解,铸造企业可以全面提升产品质量,满足客户日益增长的需求。希望本文提供的解析和建议能够为相关从业者提供有价值的参考,共同推动我国铸造行业的健康发展。
通过以上详细解析,相信读者对树脂砂铸造的工艺过程有了更全面的认识。如有任何疑问或需要进一步的技术支持,请随时联系我们。
一、树脂砂铸造工艺概述
树脂砂铸造是利用热固性或冷固性树脂作为粘结剂,将石英砂颗粒粘结在一起形成铸型的一种铸造方法。它具有以下显著特点:
高强度:树脂砂铸型具有较高的强度和硬度,能够承受高温金属液的压力而不变形。
高精度:树脂砂铸型的尺寸精度高,能够生产出复杂形状和精密结构的铸件。
良好透气性:树脂砂铸型透气性能好,有利于气体排出,减少气孔等缺陷。
易于脱模:铸件冷却后,树脂砂铸型容易破碎脱落,便于清理和后续加工。
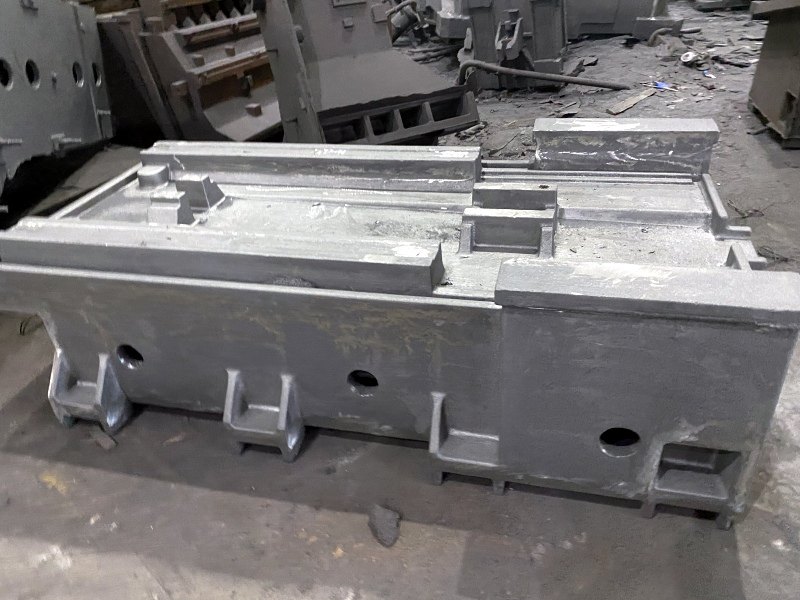
(一)原材料准备
1、选择优质原材料
生铁和废钢:生铁是铸铁件的主要原料之一,其品质直接影响到铸铁件的质量。应选择含碳量适中、杂质少的优质生铁,以保证熔炼过程中金属液的纯净度。废钢作为补充材料,可以调节铸铁中的碳当量和其他合金元素含量。选用清洁、无油污、无锈蚀的废钢,有助于减少夹渣和气孔等缺陷。
合金添加剂:根据产品需求,适量添加锰、铬、镍等合金元素,以改善铸铁件的耐磨性、耐腐蚀性和强度等性能。
2、配料计算与混合
根据铸铁件的设计要求,精确计算各种原材料的比例,确保熔炼后的金属液化学成分符合标准。使用自动配料系统或人工称重方式将各组分均匀混合,避免因比例失调而导致质量问题。
(二)制芯与制模
1、制芯设备选择
冷芯盒制芯机:适用于中小型铸件的生产,采用冷固化树脂,具有生产效率高、成本低的特点。通过压缩空气吹入树脂砂,使其快速固化成型。
热芯盒制芯机:适用于大型铸件或复杂结构铸件的生产,采用热固化树脂,具有更高的强度和尺寸精度。通过加热芯盒使树脂砂迅速固化成型。
2、模具设计与制造
模具材料的选择直接影响到铸件的尺寸精度和表面质量。选用具有良好导热性和耐磨性的模具材料(如高铬合金钢),可以有效提高铸件的成型质量和使用寿命。
对于大型或复杂铸件,采用分段式或组合式模具结构,既能保证整体精度,又能降低制造难度。利用数控机床、3D打印等先进技术进行模具加工,可以显著提高模具的精度和一致性。
(三)熔炼与浇注
1、熔炼设备选择
感应电炉:广泛应用于中小型铸铁件生产。它通过电磁感应原理加热金属,具有升温快、温度均匀、能耗低等优点。
电阻炉:适合小批量、多品种铸铁件试制及科研实验。结构简单、操作方便,能够实现精准控温。
2、熔炼工艺控制
精确控制化学成分:通过光谱分析仪等设备实时监测金属液成分,及时调整配方,确保每一批次铸件的化学成分稳定一致。
优化熔炼温度和时间:合理的温度和时间设置对铸件的质量至关重要。过高的温度会导致合金元素烧损,影响铸件性能;而过低的温度则可能使金属液流动性不足,造成浇注困难。
3、浇注系统设计
浇道的设计直接影响到金属液的填充效果和铸件的内部质量。科学合理地布置浇道,可以使金属液平稳、均匀地流入型腔,减少气孔、缩松等缺陷。
根据铸件的具体形状和壁厚分布,选择合适的浇道形式(如直浇道、横浇道、内浇道等),并优化其尺寸和位置。
4、浇注速度控制
浇注速度过快或过慢都会影响铸件的质量。过快的速度容易引发冷隔、未完全融合等问题;而过慢的速度则可能导致铸件内部出现疏松、缩孔等缺陷。通过引入自动化控制系统,实现对浇注速度的精确控制,确保每一件铸件都能获得最佳的成型效果。
(四)冷却与凝固
1、冷却介质选择
冷却介质的选择对铸件的显微组织和力学性能有重要影响。根据铸件的具体需求,选择适当的冷却介质(如空气、水、油等),调节冷却速度,使铸件各部分冷却均匀一致。
对于需要快速冷却的铸件,可采用强制风冷或喷水冷却等方式,确保铸件内部组织转变良好,达到预期的硬度和强度。
2、控制凝固顺序
合理安排铸件的凝固顺序,可以有效防止缩孔、缩松等缺陷的产生。通过设置冷铁、冒口等辅助装置,引导金属液从厚大部位向薄壁处流动,实现定向凝固。
利用计算机模拟技术,提前预测铸件的凝固过程,优化冷铁和冒口的布置方案,确保铸件内部无缺陷。
(五)清理与后处理
1、去除表面杂质
使用砂轮、刮刀等工具清除铸件表面的氧化皮、油污、锈蚀等杂质,确保焊补面干净平整。
打磨坡口,根据缺陷的大小和形状,适当打磨出适当的坡口角度(一般为30°-45°),以增加焊接面积,提高焊补质量。
2、表面修整与抛光
使用砂轮、锉刀等工具对焊缝进行打磨,使其与铸件表面平滑过渡,保证外观美观和尺寸精度。
对有特殊要求的铸件,可进行抛光处理,提高表面光洁度,增强耐磨性和抗腐蚀能力。
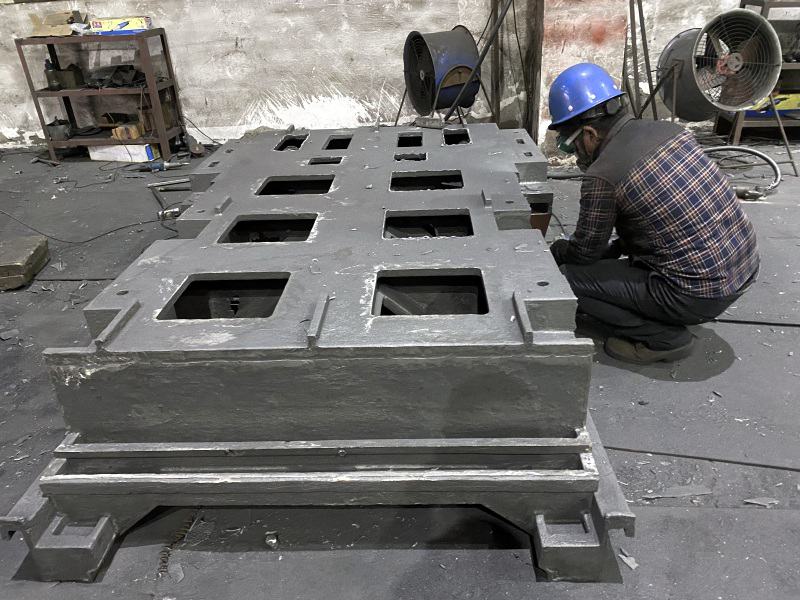
在生产线上安装在线检测设备(如超声波探伤仪、磁粉探伤仪等),可以实时监控铸件的质量状况,及时发现潜在问题,避免不合格品流入下一道工序。
配备高精度的测量工具(如三坐标测量机、激光测距仪等),对铸件的尺寸精度进行严格把关。定期校准测量仪器,确保其准确性,避免因测量误差导致的质量问题。
(六)包装与运输
1、防潮防锈措施
在包装前,对铸件进行防潮防锈处理,如涂覆防锈油、包裹塑料薄膜等,确保铸件在运输过程中不会受到潮湿和氧化的影响。
2、安全包装与标识
选择合适的包装材料(如木箱、纸箱等),确保铸件在运输过程中不受损坏。同时,在包装上标明产品名称、规格型号、生产日期、厂家信息等,便于客户识别和管理。
三、总结
树脂砂铸造作为一种先进的铸造工艺,涵盖了从原材料准备到成品出炉的多个环节。每个步骤都需要严格把控,以确保最终产品的质量和性能。通过对原材料选择、制芯与制模、熔炼与浇注、冷却与凝固、清理与后处理以及包装与运输等环节的深入理解,铸造企业可以全面提升产品质量,满足客户日益增长的需求。希望本文提供的解析和建议能够为相关从业者提供有价值的参考,共同推动我国铸造行业的健康发展。
通过以上详细解析,相信读者对树脂砂铸造的工艺过程有了更全面的认识。如有任何疑问或需要进一步的技术支持,请随时联系我们。