在铸造行业中,铸铁件因其良好的机械性能和广泛的用途而备受青睐。然而,要生产出高质量的铸铁件,熔炼工艺是关键环节之一。本文将详细解析铸铁件熔炼工艺的具体步骤,帮助读者全面了解这一复杂而又重要的过程。
一、铸铁件熔炼工艺概述
铸铁件的熔炼工艺是指将生铁、废钢等原材料通过加热、熔化、精炼等一系列操作,最终得到符合质量要求的液态金属的过程。这个过程中,每一个步骤都至关重要,直接关系到铸铁件的化学成分、微观组织和力学性能。为了确保产品质量,铸造企业必须严格按照规范进行操作,并不断优化工艺参数。
二、铸铁件熔炼工艺的主要步骤
(一)原材料准备
1、选择优质原材料
生铁:生铁是铸铁件的主要原料之一,其品质直接影响到铸铁件的质量。应选择含碳量适中、杂质少的优质生铁,以保证熔炼过程中金属液的纯净度。
废钢:废钢作为补充材料,可以调节铸铁中的碳当量和其他合金元素含量。选用清洁、无油污、无锈蚀的废钢,有助于减少夹渣和气孔等缺陷。
合金添加剂:根据产品需求,适量添加锰、铬、镍等合金元素,以改善铸铁件的耐磨性、耐腐蚀性和强度等性能。
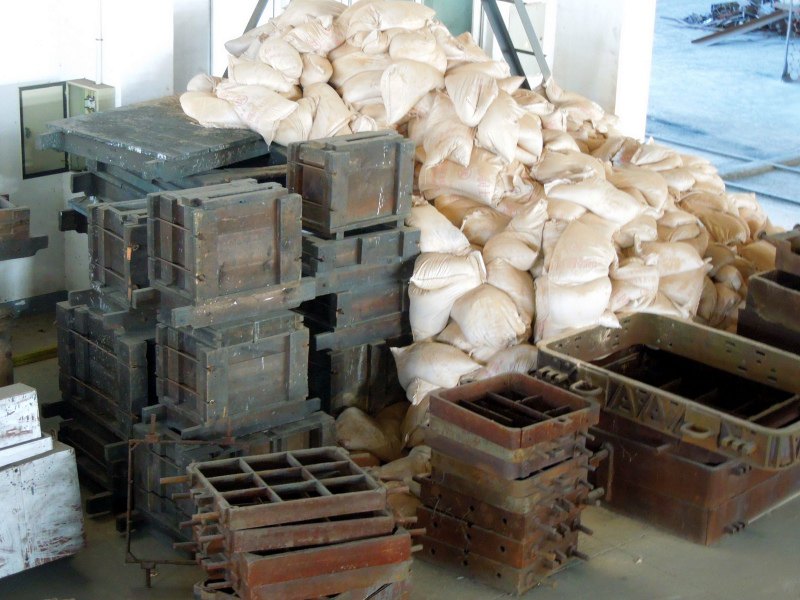
2、配料计算与混合
根据铸铁件的设计要求,精确计算各种原材料的比例,确保熔炼后的金属液化学成分符合标准。
使用自动配料系统或人工称重方式将各组分均匀混合,避免因比例失调而导致质量问题。
(二)熔炼设备选择与预热
1、熔炼设备类型
冲天炉:传统熔炼设备,适用于大批量生产普通灰铸铁件。具有成本低、操作简单的特点,但环保性能较差。
感应电炉:现代高效熔炼设备,广泛应用于中小型铸铁件生产。它通过电磁感应原理加热金属,具有升温快、温度均匀、能耗低等优点。
电阻炉:适合小批量、多品种铸铁件试制及科研实验。结构简单、操作方便,能够实现精准控温。
2、设备预热
在正式熔炼前,应对熔炼设备进行充分预热,确保炉膛内壁温度达到设定值。这不仅有利于提高熔炼效率,还能防止冷启动时对设备造成损害。
(三)熔化与保温
1、熔化过程
将准备好的原材料加入熔炼设备中,按照规定的程序进行加热熔化。熔化过程中应注意控制火焰强度和熔炼时间,确保金属液完全融化且成分均匀。
对于感应电炉,还需调整频率和功率,使金属液保持适当的搅拌状态,促进合金元素溶解和气体排出。
2、保温处理
熔化完成后,将金属液转入保温炉或浇包中,维持一定温度范围(一般为1350-1450℃),以便后续工序使用。
保温期间,定期取样分析金属液成分,及时调整配方,确保最终产品符合质量要求。
(四)精炼与除渣
1、精炼目的
精炼是为了去除金属液中的有害杂质(如硫、磷、氧化物等),并调整其化学成分,以获得纯净、稳定的液态金属。
精炼还可以改善金属液的流动性,减少缩孔、缩松等缺陷,提高铸件质量。
2、常用精炼方法
孕育处理:向金属液中加入少量孕育剂(如硅铁、稀土等),促进石墨化,细化晶粒,增强铸铁件的强度和韧性。
脱氧处理:采用铝、锰等还原剂去除金属液中的氧气,降低氧化夹杂物,提高金属液的纯净度。
扒渣操作:利用专用工具将浮在金属液表面的渣滓清除干净,防止其混入铸件内部形成夹渣。
(五)浇注与冷却
1、浇注准备
浇注前,需检查模具是否完好无损,清理型腔内的灰尘和杂物,确保浇道、冒口畅通无阻。
根据铸件形状和尺寸,合理布置浇注系统,选择合适的浇注速度和角度,保证金属液平稳、均匀地填充型腔。
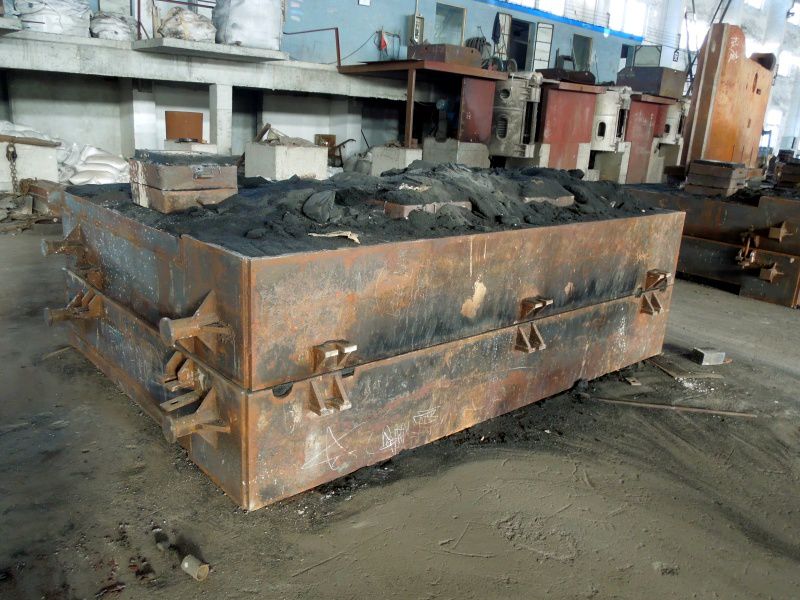
2、浇注过程
将保温炉中的金属液倒入浇包中,按照预定路线进行浇注。浇注时应注意保持稳定的速度和连续性,避免出现冷隔、未完全融合等问题。
对于大型或复杂铸件,可采用多点同时浇注的方式,确保铸件各部分受热均匀,减少变形和裂纹。
3、冷却定型
浇注完成后,铸件在模具中自然冷却凝固。冷却速度对铸件显微组织有重要影响,因此应根据不同铸件的需求,选择适当的冷却介质(如空气、水、油等)和冷却方式(如强制风冷、砂型自冷等)。
冷却过程中,注意监控铸件温度变化,及时采取措施防止开裂和变形。
(六)后处理与检测
1、清理铸件表面
铸件冷却后,需进行表面清理,去除粘附在其上的砂子、氧化皮等杂物。常用的清理方法包括抛丸、喷砂、打磨等。
表面清理不仅可以提高铸件外观质量,还有利于后续加工和涂装作业。
2、质量检测
对铸件进行严格的质量检测,包括尺寸精度、表面粗糙度、硬度、金相组织等方面的检查。
利用超声波探伤仪、磁粉探伤仪、X射线实时成像系统等无损检测设备,发现铸件内部潜在缺陷,确保产品质量合格。
最终合格的产品方可入库或交付客户使用。
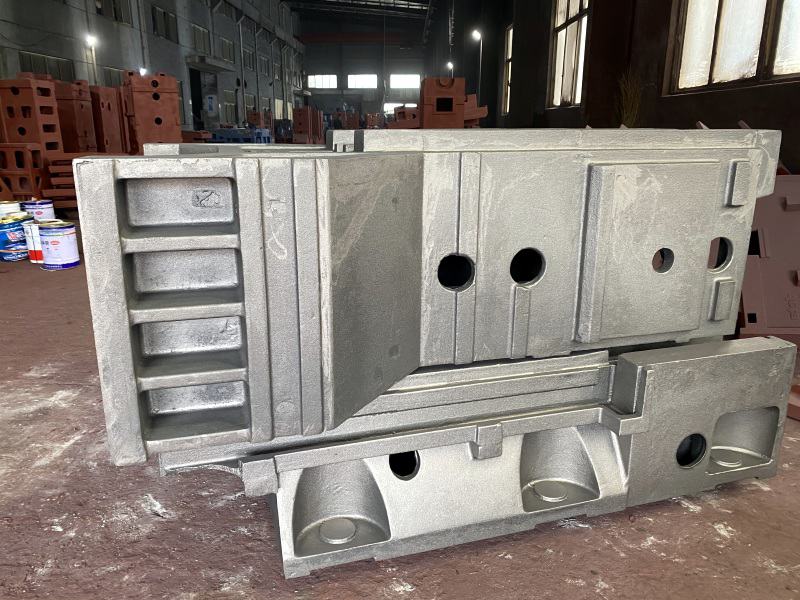
三、总结
铸铁件熔炼工艺是一个复杂而精细的过程,涵盖了从原材料准备到成品出炉的多个环节。每个步骤都需要严格把控,以确保最终产品的质量和性能。通过对熔炼工艺的深入了解,铸造企业可以更好地优化生产流程,提高生产效率,降低成本,从而在激烈的市场竞争中占据优势。希望本文提供的解析和建议能够为相关从业者提供有价值的参考,共同推动我国铸造行业的健康发展。
通过以上详细解析,相信读者对铸铁件熔炼工艺有了更全面的认识。如有任何疑问或需要进一步的技术支持,请随时联系我们。
一、铸铁件熔炼工艺概述
铸铁件的熔炼工艺是指将生铁、废钢等原材料通过加热、熔化、精炼等一系列操作,最终得到符合质量要求的液态金属的过程。这个过程中,每一个步骤都至关重要,直接关系到铸铁件的化学成分、微观组织和力学性能。为了确保产品质量,铸造企业必须严格按照规范进行操作,并不断优化工艺参数。
二、铸铁件熔炼工艺的主要步骤
(一)原材料准备
1、选择优质原材料
生铁:生铁是铸铁件的主要原料之一,其品质直接影响到铸铁件的质量。应选择含碳量适中、杂质少的优质生铁,以保证熔炼过程中金属液的纯净度。
废钢:废钢作为补充材料,可以调节铸铁中的碳当量和其他合金元素含量。选用清洁、无油污、无锈蚀的废钢,有助于减少夹渣和气孔等缺陷。
合金添加剂:根据产品需求,适量添加锰、铬、镍等合金元素,以改善铸铁件的耐磨性、耐腐蚀性和强度等性能。
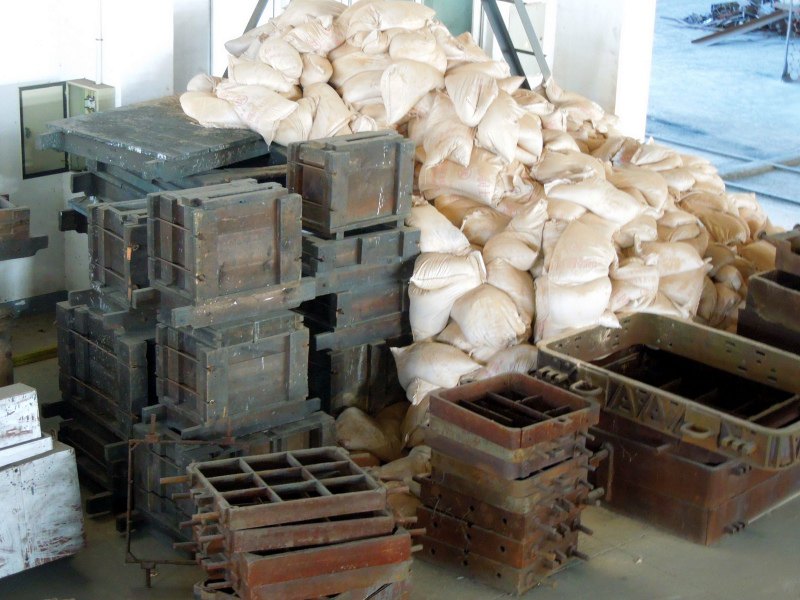
2、配料计算与混合
根据铸铁件的设计要求,精确计算各种原材料的比例,确保熔炼后的金属液化学成分符合标准。
使用自动配料系统或人工称重方式将各组分均匀混合,避免因比例失调而导致质量问题。
(二)熔炼设备选择与预热
1、熔炼设备类型
冲天炉:传统熔炼设备,适用于大批量生产普通灰铸铁件。具有成本低、操作简单的特点,但环保性能较差。
感应电炉:现代高效熔炼设备,广泛应用于中小型铸铁件生产。它通过电磁感应原理加热金属,具有升温快、温度均匀、能耗低等优点。
电阻炉:适合小批量、多品种铸铁件试制及科研实验。结构简单、操作方便,能够实现精准控温。
2、设备预热
在正式熔炼前,应对熔炼设备进行充分预热,确保炉膛内壁温度达到设定值。这不仅有利于提高熔炼效率,还能防止冷启动时对设备造成损害。
(三)熔化与保温
1、熔化过程
将准备好的原材料加入熔炼设备中,按照规定的程序进行加热熔化。熔化过程中应注意控制火焰强度和熔炼时间,确保金属液完全融化且成分均匀。
对于感应电炉,还需调整频率和功率,使金属液保持适当的搅拌状态,促进合金元素溶解和气体排出。
2、保温处理
熔化完成后,将金属液转入保温炉或浇包中,维持一定温度范围(一般为1350-1450℃),以便后续工序使用。
保温期间,定期取样分析金属液成分,及时调整配方,确保最终产品符合质量要求。
(四)精炼与除渣
1、精炼目的
精炼是为了去除金属液中的有害杂质(如硫、磷、氧化物等),并调整其化学成分,以获得纯净、稳定的液态金属。
精炼还可以改善金属液的流动性,减少缩孔、缩松等缺陷,提高铸件质量。
2、常用精炼方法
孕育处理:向金属液中加入少量孕育剂(如硅铁、稀土等),促进石墨化,细化晶粒,增强铸铁件的强度和韧性。
脱氧处理:采用铝、锰等还原剂去除金属液中的氧气,降低氧化夹杂物,提高金属液的纯净度。
扒渣操作:利用专用工具将浮在金属液表面的渣滓清除干净,防止其混入铸件内部形成夹渣。
(五)浇注与冷却
1、浇注准备
浇注前,需检查模具是否完好无损,清理型腔内的灰尘和杂物,确保浇道、冒口畅通无阻。
根据铸件形状和尺寸,合理布置浇注系统,选择合适的浇注速度和角度,保证金属液平稳、均匀地填充型腔。
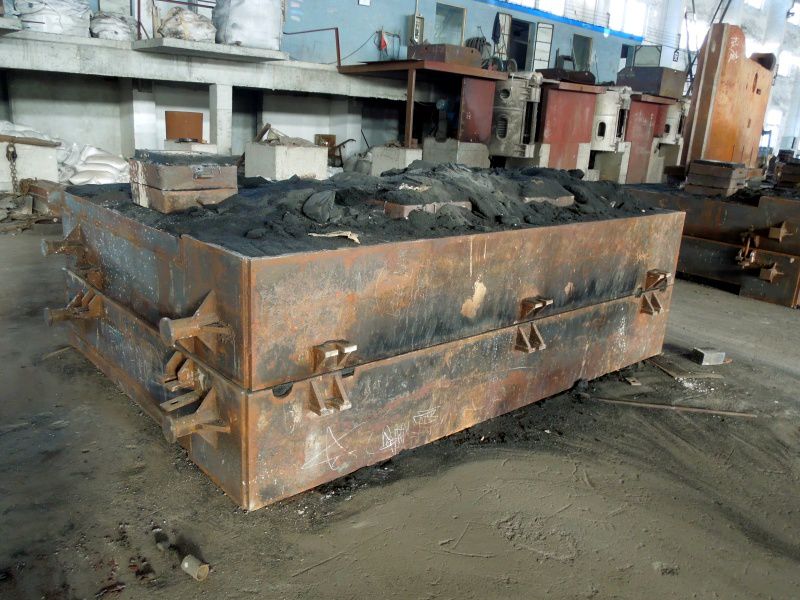
2、浇注过程
将保温炉中的金属液倒入浇包中,按照预定路线进行浇注。浇注时应注意保持稳定的速度和连续性,避免出现冷隔、未完全融合等问题。
对于大型或复杂铸件,可采用多点同时浇注的方式,确保铸件各部分受热均匀,减少变形和裂纹。
3、冷却定型
浇注完成后,铸件在模具中自然冷却凝固。冷却速度对铸件显微组织有重要影响,因此应根据不同铸件的需求,选择适当的冷却介质(如空气、水、油等)和冷却方式(如强制风冷、砂型自冷等)。
冷却过程中,注意监控铸件温度变化,及时采取措施防止开裂和变形。
(六)后处理与检测
1、清理铸件表面
铸件冷却后,需进行表面清理,去除粘附在其上的砂子、氧化皮等杂物。常用的清理方法包括抛丸、喷砂、打磨等。
表面清理不仅可以提高铸件外观质量,还有利于后续加工和涂装作业。
2、质量检测
对铸件进行严格的质量检测,包括尺寸精度、表面粗糙度、硬度、金相组织等方面的检查。
利用超声波探伤仪、磁粉探伤仪、X射线实时成像系统等无损检测设备,发现铸件内部潜在缺陷,确保产品质量合格。
最终合格的产品方可入库或交付客户使用。
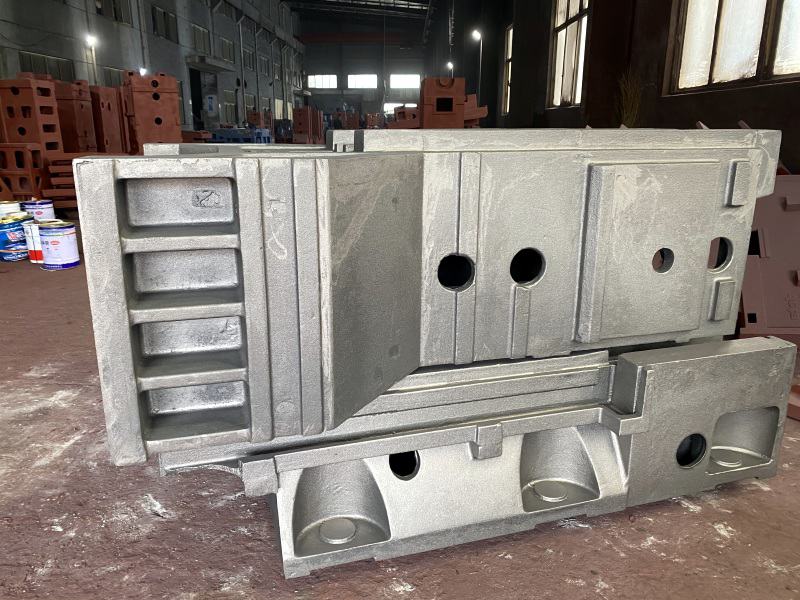
三、总结
铸铁件熔炼工艺是一个复杂而精细的过程,涵盖了从原材料准备到成品出炉的多个环节。每个步骤都需要严格把控,以确保最终产品的质量和性能。通过对熔炼工艺的深入了解,铸造企业可以更好地优化生产流程,提高生产效率,降低成本,从而在激烈的市场竞争中占据优势。希望本文提供的解析和建议能够为相关从业者提供有价值的参考,共同推动我国铸造行业的健康发展。
通过以上详细解析,相信读者对铸铁件熔炼工艺有了更全面的认识。如有任何疑问或需要进一步的技术支持,请随时联系我们。