机床铸件是机械制造中的重要基础件之一,广泛应用于各种机械设备的制造中。其质量的好坏直接影响到整个机械设备的性能和寿命。那么,机床铸件的质量好坏究竟取决于哪些因素呢?本文将从原材料、铸造工艺、热处理、检测方法等方面详细分析,帮助读者全面了解影响机床铸件质量的关键因素。
一、原材料的选择
1.材质选择
机床铸件常用的材质包括灰铸铁、球墨铸铁、合金铸铁等。这些材质的选择直接关系到铸件的力学性能和抗疲劳能力。
灰铸铁具有良好的减振性和耐磨性,适用于制造大型机床床身;球墨铸铁则具有较高的强度和韧性,适用于制造需要较高强度的零部件;合金铸铁则具有更好的耐热性和耐磨性,适用于特殊工况下的应用。
2.原材料质量
原材料的质量直接影响到最终铸件的质量。优质的原材料不仅化学成分稳定,而且杂质含量低,能够保证铸件的性能和稳定性。
需要严格控制原材料中的有害元素(如硫、磷)含量,以减少铸件产生缺陷的可能性。
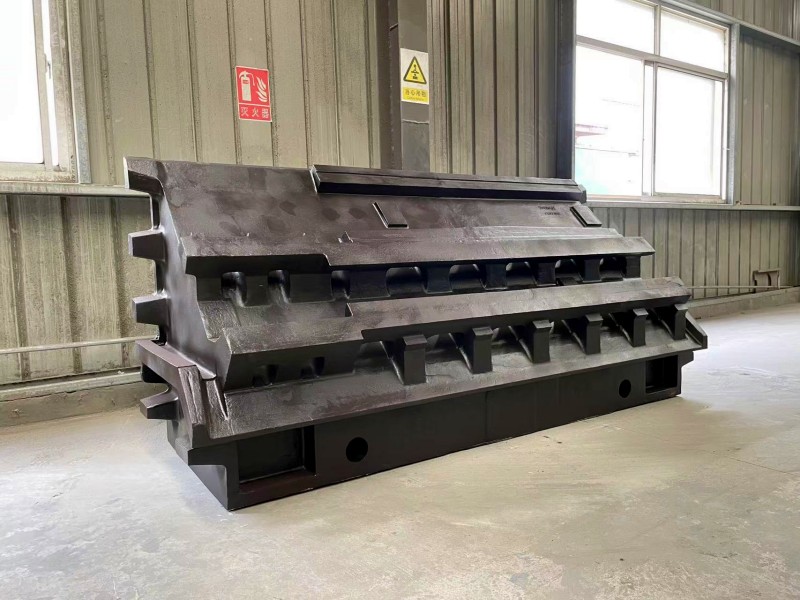
二、铸造工艺
1.熔炼工艺
熔炼工艺是铸造过程中的关键环节,主要包括熔炼温度、保温时间和浇注速度等因素。
合适的熔炼温度可以保证金属液的流动性,减少气孔和缩孔等缺陷;合理的保温时间可以保证金属液的均匀性;适当的浇注速度可以减少铸件中的夹杂和气孔。
2.模具设计
模具的设计直接关系到铸件的形状和尺寸精度。合理的设计可以有效避免铸件变形和裂纹等问题。
模具材料的选择也很重要,需要选用具有良好导热性和耐磨性的材料,以保证铸件的质量。
3.浇注工艺
浇注工艺主要包括浇注温度、浇注速度和浇注方式等因素。
浇注温度过高或过低都会影响铸件的组织和性能;合理的浇注速度可以保证金属液的平稳流动;正确的浇注方式可以减少铸件中的气孔和夹杂。
三、热处理
1.退火处理
退火处理是为了消除铸件中的内应力,改善铸件的力学性能。通过高温加热和缓慢冷却,可以使铸件内部组织均匀化,提高铸件的塑性和韧性。
退火温度和保温时间的选择需要根据具体材质和铸件尺寸来确定。
2.正火处理
正火处理是为了细化晶粒,提高铸件的硬度和耐磨性。通过加热至一定温度后快速冷却,可以使铸件内部组织变得细小均匀,从而提高铸件的整体性能。
正火温度和冷却速度的选择同样需要根据具体材质和铸件尺寸来确定。
3.调质处理
调质处理是为了进一步提高铸件的综合性能。通过淬火加回火的方式,可以同时提高铸件的强度和韧性。
淬火温度、淬火介质和回火温度的选择需要根据具体材质和铸件尺寸来确定。
四、检测方法
1.外观检测
外观检测是最基本的质量检测方法,主要检查铸件的表面缺陷,如裂纹、气孔、夹杂等。
通过目测和简单的量具测量,可以初步判断铸件的表面质量。
2.尺寸检测
尺寸检测是为了保证铸件的尺寸精度,主要使用游标卡尺、千分尺等精密量具进行测量。
尺寸检测可以发现铸件是否存在超差现象,从而保证铸件的加工余量。
3.无损检测
无损检测是目前广泛应用的质量检测方法,主要包括磁粉探伤、渗透探伤、超声波探伤等。
磁粉探伤可以检测铸件表面和近表面的裂纹等缺陷;渗透探伤可以检测铸件表面开口缺陷;超声波探伤可以检测铸件内部缺陷,如气孔、夹杂等。
4.力学性能检测
力学性能检测是为了验证铸件的力学性能是否符合标准要求,主要包括拉伸试验、弯曲试验、冲击试验等。
通过力学性能检测,可以全面评估铸件的强度、塑性和韧性等性能指标。
五、案例分析
为了更好地理解上述因素对机床铸件质量的影响,我们来看几个实际案例:
1.案例一:某机床厂生产的铸件出现大量气孔
分析原因:该厂使用的原材料中含有较多的气体,导致熔炼过程中产生大量气泡;浇注工艺不合理,浇注速度过快,无法及时排出气泡。
解决方案:严格控制原材料质量,减少气体含量;调整浇注工艺,降低浇注速度,增加排气措施。
2.案例二:某机床厂生产的铸件出现裂纹
分析原因:该厂使用的模具设计不合理,铸件在冷却过程中产生较大的内应力;热处理工艺不当,铸件未充分消除内应力。
解决方案:重新设计模具,改善铸件的冷却条件;优化热处理工艺,充分消除内应力。
3.案例三:某机床厂生产的铸件尺寸超差
分析原因:该厂的模具精度不够,导致铸件尺寸不准确;检测方法不规范,未能及时发现尺寸偏差。
解决方案:提高模具精度,确保铸件尺寸准确;规范检测方法,加强尺寸检测,及时纠正偏差。
六、总结
机床铸件的质量好坏取决于多个因素,包括原材料的选择、铸造工艺、热处理和检测方法等。只有在各个环节都做到精益求精,才能生产出高质量的机床铸件。希望本文能为广大读者提供参考,帮助大家更好地理解和掌握影响机床铸件质量的关键因素,从而提升生产水平和产品质量。
如果您还有其他关于机床铸件的问题,欢迎随时咨询相关专业人士。希望本文能对您有所帮助!
一、原材料的选择
1.材质选择
机床铸件常用的材质包括灰铸铁、球墨铸铁、合金铸铁等。这些材质的选择直接关系到铸件的力学性能和抗疲劳能力。
灰铸铁具有良好的减振性和耐磨性,适用于制造大型机床床身;球墨铸铁则具有较高的强度和韧性,适用于制造需要较高强度的零部件;合金铸铁则具有更好的耐热性和耐磨性,适用于特殊工况下的应用。
2.原材料质量
原材料的质量直接影响到最终铸件的质量。优质的原材料不仅化学成分稳定,而且杂质含量低,能够保证铸件的性能和稳定性。
需要严格控制原材料中的有害元素(如硫、磷)含量,以减少铸件产生缺陷的可能性。
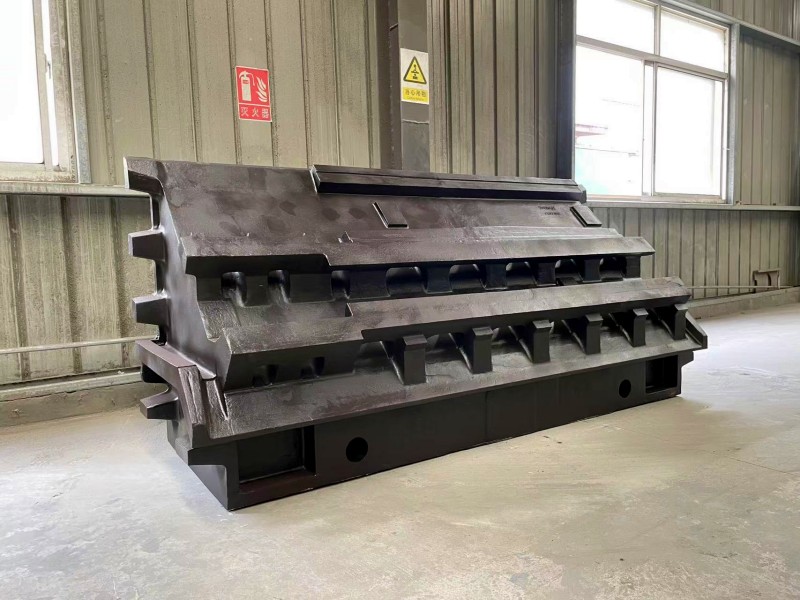
二、铸造工艺
1.熔炼工艺
熔炼工艺是铸造过程中的关键环节,主要包括熔炼温度、保温时间和浇注速度等因素。
合适的熔炼温度可以保证金属液的流动性,减少气孔和缩孔等缺陷;合理的保温时间可以保证金属液的均匀性;适当的浇注速度可以减少铸件中的夹杂和气孔。
2.模具设计
模具的设计直接关系到铸件的形状和尺寸精度。合理的设计可以有效避免铸件变形和裂纹等问题。
模具材料的选择也很重要,需要选用具有良好导热性和耐磨性的材料,以保证铸件的质量。
3.浇注工艺
浇注工艺主要包括浇注温度、浇注速度和浇注方式等因素。
浇注温度过高或过低都会影响铸件的组织和性能;合理的浇注速度可以保证金属液的平稳流动;正确的浇注方式可以减少铸件中的气孔和夹杂。
三、热处理
1.退火处理
退火处理是为了消除铸件中的内应力,改善铸件的力学性能。通过高温加热和缓慢冷却,可以使铸件内部组织均匀化,提高铸件的塑性和韧性。
退火温度和保温时间的选择需要根据具体材质和铸件尺寸来确定。
2.正火处理
正火处理是为了细化晶粒,提高铸件的硬度和耐磨性。通过加热至一定温度后快速冷却,可以使铸件内部组织变得细小均匀,从而提高铸件的整体性能。
正火温度和冷却速度的选择同样需要根据具体材质和铸件尺寸来确定。
3.调质处理
调质处理是为了进一步提高铸件的综合性能。通过淬火加回火的方式,可以同时提高铸件的强度和韧性。
淬火温度、淬火介质和回火温度的选择需要根据具体材质和铸件尺寸来确定。
四、检测方法
1.外观检测
外观检测是最基本的质量检测方法,主要检查铸件的表面缺陷,如裂纹、气孔、夹杂等。
通过目测和简单的量具测量,可以初步判断铸件的表面质量。
2.尺寸检测
尺寸检测是为了保证铸件的尺寸精度,主要使用游标卡尺、千分尺等精密量具进行测量。
尺寸检测可以发现铸件是否存在超差现象,从而保证铸件的加工余量。
3.无损检测
无损检测是目前广泛应用的质量检测方法,主要包括磁粉探伤、渗透探伤、超声波探伤等。
磁粉探伤可以检测铸件表面和近表面的裂纹等缺陷;渗透探伤可以检测铸件表面开口缺陷;超声波探伤可以检测铸件内部缺陷,如气孔、夹杂等。
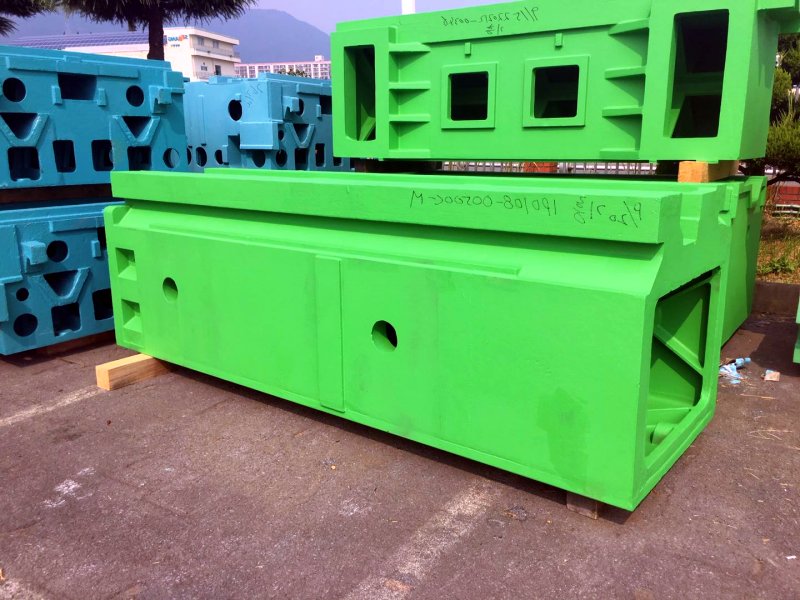
力学性能检测是为了验证铸件的力学性能是否符合标准要求,主要包括拉伸试验、弯曲试验、冲击试验等。
通过力学性能检测,可以全面评估铸件的强度、塑性和韧性等性能指标。
五、案例分析
为了更好地理解上述因素对机床铸件质量的影响,我们来看几个实际案例:
1.案例一:某机床厂生产的铸件出现大量气孔
分析原因:该厂使用的原材料中含有较多的气体,导致熔炼过程中产生大量气泡;浇注工艺不合理,浇注速度过快,无法及时排出气泡。
解决方案:严格控制原材料质量,减少气体含量;调整浇注工艺,降低浇注速度,增加排气措施。
2.案例二:某机床厂生产的铸件出现裂纹
分析原因:该厂使用的模具设计不合理,铸件在冷却过程中产生较大的内应力;热处理工艺不当,铸件未充分消除内应力。
解决方案:重新设计模具,改善铸件的冷却条件;优化热处理工艺,充分消除内应力。
3.案例三:某机床厂生产的铸件尺寸超差
分析原因:该厂的模具精度不够,导致铸件尺寸不准确;检测方法不规范,未能及时发现尺寸偏差。
解决方案:提高模具精度,确保铸件尺寸准确;规范检测方法,加强尺寸检测,及时纠正偏差。
六、总结
机床铸件的质量好坏取决于多个因素,包括原材料的选择、铸造工艺、热处理和检测方法等。只有在各个环节都做到精益求精,才能生产出高质量的机床铸件。希望本文能为广大读者提供参考,帮助大家更好地理解和掌握影响机床铸件质量的关键因素,从而提升生产水平和产品质量。
如果您还有其他关于机床铸件的问题,欢迎随时咨询相关专业人士。希望本文能对您有所帮助!