铸造作为一种历史悠久的金属成型技术,在现代工业中依然扮演着举足轻重的角色。无论是航空航天、汽车制造还是机械工程领域,铸造件都是不可或缺的关键零部件。然而,在实际的铸造生产过程中,各种缺陷常常影响到铸件的质量和性能,甚至导致整个生产过程的失败。因此,对铸造生产过程中常见的缺陷进行深入分析,并提出有效的解决方案显得尤为重要。
常见缺陷分析
1.气孔
气孔是指在铸件内部或表面存在的孔洞。这类缺陷通常由气体溶解在熔融金属中未能及时排出所致。
成因:主要由于金属液中的气体含量过高;浇注系统设计不合理;型砂或涂料透气性差;浇注速度过快等。
影响:降低铸件的力学性能和耐腐蚀性,影响其外观质量。
2.缩孔与缩松
缩孔指的是铸件凝固过程中由于补缩不足而形成的空洞;缩松则是指这些空洞相互连接形成网络状分布的现象。
成因:合金成分不当;浇注温度控制不准确;冷却速度不均匀等。
影响:严重削弱了铸件的强度和致密性,降低了使用寿命。
3.砂眼
砂眼是指铸件表面或内部存在直径较小(一般小于5mm)的圆形或椭圆形孔洞。
成因:型砂强度不够;浇注时冲击力过大;金属液流动性差等。
影响:破坏铸件的整体美观度,并可能成为应力集中点,引发断裂。
4.裂纹
裂纹可以分为热裂纹和冷裂纹两大类,前者发生在高温状态下,后者则是在较低温度下形成。
成因:合金化学成分不合适;模具预热不足;浇注温度过高或过低;冷却速度控制不当等。
影响:极大地降低了铸件的安全性和可靠性。
解决方法探讨
针对上述各种铸造缺陷,我们可以从以下几个方面入手寻找相应的解决措施:
1.提高原材料质量
选择合适的合金材料,并严格控制其成分比例,确保金属液具有良好的流动性和充型能力。
2.改进工艺参数
合理设置浇注温度和速度,保证熔融金属平稳进入型腔,避免产生涡流和飞溅现象。同时,适当延长保温时间,促进气体逸出,减少气孔形成的机会。
3.优化浇注系统设计
采用科学合理的浇道布置方案,确保金属液能够均匀分配至各个部位,有效防止局部过热和凝固不良问题的发生。
4.加强模具维护
定期检查和清洁模具表面,确保其平整光滑无损伤。对于易磨损部位应及时更换新材料,以提高整体使用寿命。
5.应用先进检测手段
利用X射线探伤仪、超声波扫描仪等现代化设备对铸件进行全面检测,及时发现潜在缺陷并采取相应修复措施。
结论
铸造生产是一项复杂而精细的工作,任何一个环节出现失误都可能导致产品质量下降。通过本文对铸造过程中常见缺陷及其成因的详细分析,我们不难发现,只有不断优化生产工艺流程,提升操作人员技术水平,才能从根本上消除各类缺陷,生产出优质可靠的铸件产品。希望本文能为相关企业和技术人员提供有益参考,共同推动我国铸造行业向更高水平迈进!
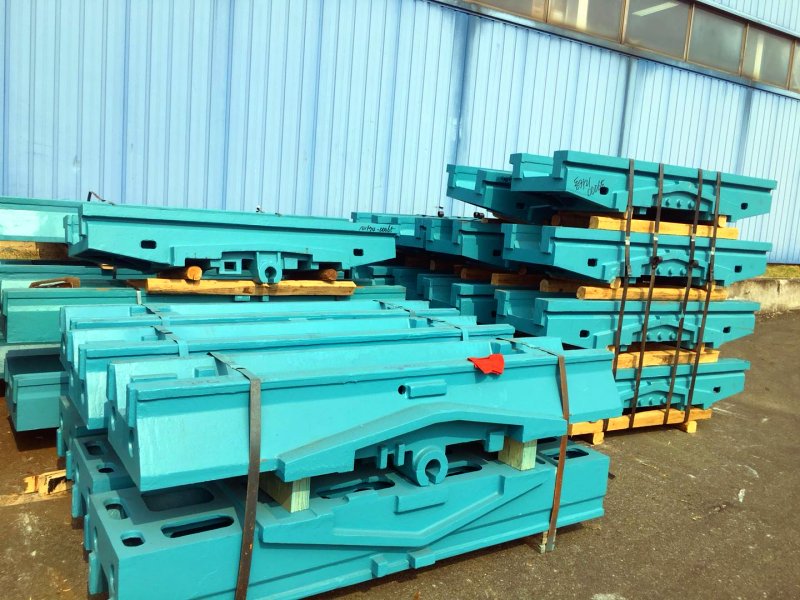
1.气孔
气孔是指在铸件内部或表面存在的孔洞。这类缺陷通常由气体溶解在熔融金属中未能及时排出所致。
成因:主要由于金属液中的气体含量过高;浇注系统设计不合理;型砂或涂料透气性差;浇注速度过快等。
影响:降低铸件的力学性能和耐腐蚀性,影响其外观质量。
2.缩孔与缩松
缩孔指的是铸件凝固过程中由于补缩不足而形成的空洞;缩松则是指这些空洞相互连接形成网络状分布的现象。
成因:合金成分不当;浇注温度控制不准确;冷却速度不均匀等。
影响:严重削弱了铸件的强度和致密性,降低了使用寿命。
3.砂眼
砂眼是指铸件表面或内部存在直径较小(一般小于5mm)的圆形或椭圆形孔洞。
成因:型砂强度不够;浇注时冲击力过大;金属液流动性差等。
影响:破坏铸件的整体美观度,并可能成为应力集中点,引发断裂。
4.裂纹
裂纹可以分为热裂纹和冷裂纹两大类,前者发生在高温状态下,后者则是在较低温度下形成。
成因:合金化学成分不合适;模具预热不足;浇注温度过高或过低;冷却速度控制不当等。
影响:极大地降低了铸件的安全性和可靠性。
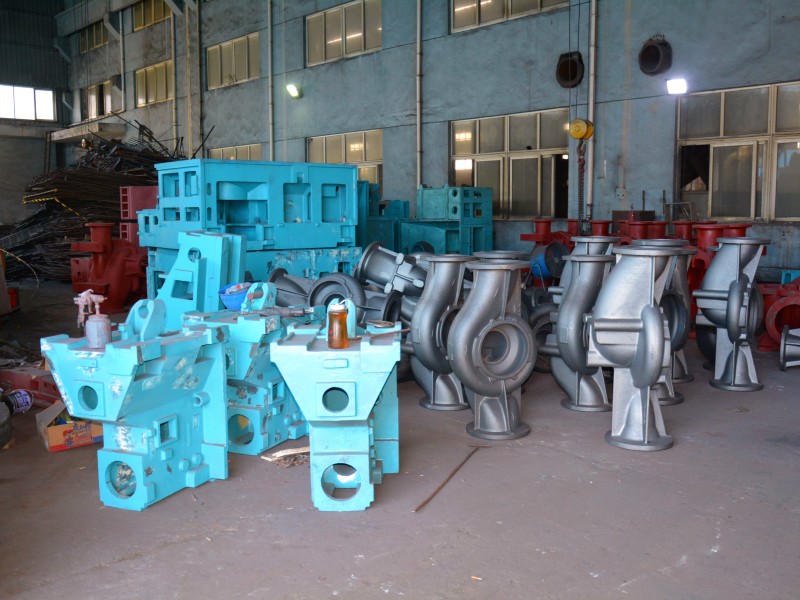
针对上述各种铸造缺陷,我们可以从以下几个方面入手寻找相应的解决措施:
1.提高原材料质量
选择合适的合金材料,并严格控制其成分比例,确保金属液具有良好的流动性和充型能力。
2.改进工艺参数
合理设置浇注温度和速度,保证熔融金属平稳进入型腔,避免产生涡流和飞溅现象。同时,适当延长保温时间,促进气体逸出,减少气孔形成的机会。
3.优化浇注系统设计
采用科学合理的浇道布置方案,确保金属液能够均匀分配至各个部位,有效防止局部过热和凝固不良问题的发生。
4.加强模具维护
定期检查和清洁模具表面,确保其平整光滑无损伤。对于易磨损部位应及时更换新材料,以提高整体使用寿命。
5.应用先进检测手段
利用X射线探伤仪、超声波扫描仪等现代化设备对铸件进行全面检测,及时发现潜在缺陷并采取相应修复措施。
结论
铸造生产是一项复杂而精细的工作,任何一个环节出现失误都可能导致产品质量下降。通过本文对铸造过程中常见缺陷及其成因的详细分析,我们不难发现,只有不断优化生产工艺流程,提升操作人员技术水平,才能从根本上消除各类缺陷,生产出优质可靠的铸件产品。希望本文能为相关企业和技术人员提供有益参考,共同推动我国铸造行业向更高水平迈进!