一、影响铸造表面光洁度常见原因
1.原材料,比如型砂的形状,分为圆形方形和三角形,最差的是三角形,缝隙特别大(如果是树脂砂造型,还会增加树脂的加入量,当然也会同时增加发气量,如果排气不好就容易形成气孔),最好的是圆形砂。如果是煤粉砂,砂的配比(砂子的强度和湿度)对外观的影响也很大。如果是二氧化碳的硬化砂,那就主要是看涂料了
2.材质,如果铸件的化学成分配比失调,比如锰低,容易产生疏松,表面材质粗大
3.浇铸系统,如果浇铸系统不合理,也容易造成铸件疏松,严重的会发生铸件浇不到的情况,甚至做不成完整的铸件。
憋渣系统不合理会使渣质进入型腔产生渣眼
4.造渣,如果铁水中的渣质没有清理干净或者浇铸时没有挡住渣质,使渣跑到型腔里,那必然会出现渣眼
5.人为,由于马虎大意,合箱时砂子没有清理干净或者掉进砂子,造型是砂子没有橦实,或是砂子配比不合理,砂子强度不够,铸件就会产生砂眼
6.硫磷超标,会使铸件产生裂纹在生产或指导生产时,这都是必须要注意的事项,才能保证铸件的质量。
上面讲到的原因也只是其中很小的一部分,由于铸造的生产千变万化,深奥异常,在生产时遇到的问题也会经常出现,有时出现一个问题很久都找不到原因。
二、影响灰铸铁粗糙度的三大因素
表面粗糙度作为灰铸铁表面质量的一项重要衡量指标,不仅直接决定了灰铸铁零件的外观精美程度,而且对机器的装备质量及灰铸铁零件的使用寿命都有着很大的影响。本文着重从机床、刀具、切削参数三方面分析如何提高灰铸铁零件的表面粗糙度。
1、机床对灰铸铁零件表面粗糙度的影响
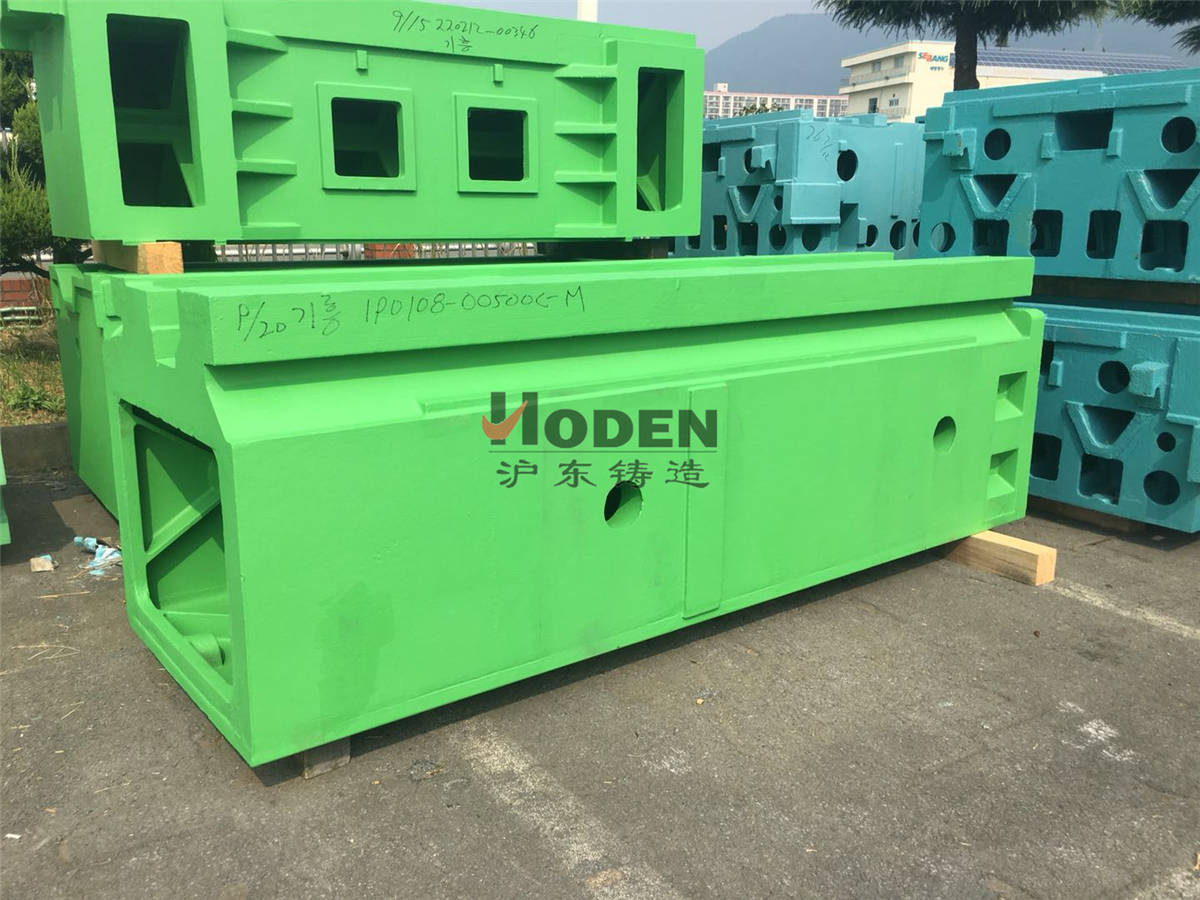
机床刚性差,主轴精度差,机床固定不牢固,机床各部件配合间隙较大等因素都会影响灰铸铁零件的表面粗糙度。
举个例子:如机床主轴跳动精度是0.002mm,也就是2微米跳动,那理论上是不可能加工出粗糙度会低于0.002mm粗糙度的工件,一般表面粗糙度Ra1.0的工件还可以加工出来。并且灰铸铁本身是铸造件,就不会像钢件一样轻松加工出较高的表面粗糙度,再加上机床自身的条件差,更难保证表面粗糙度。
机床刚性一般是出厂时就设置好的,无法修改,除了机床刚性外,还可调整主轴间隙,提高轴承精度等,使机床间隙变小,从而对灰铸铁零件在加工中获得较高的表面粗糙度得到一定保障。
2、切削刀具对灰铸铁零件表面粗糙度的影响
刀具材料的选择
当刀具材料与被加工材料金属分子亲和力大时,被加工材料容易与刀具粘结而生成积屑瘤和鳞刺,因此凡是粘结严重的,摩擦严重的,表面粗糙度就大,反之就小。同样加工灰铸铁零件,硬质合金刀片很难达到Ra1.6的表面粗糙度,即使达到了,其刀具寿命也大打折扣,而BNK30材质的CBN刀具则由于刀具材料摩擦系数低,优异的高温热稳定性和耐磨性,可在切削速度高出硬质合金几倍的条件下,轻松加工出Ra1.6的表面粗糙度,同时刀具寿命是硬质合金刀具的几十倍,表面亮度提高一个数量级。2. 2
刀具几何参数的选择
刀具几何参数中对表面粗糙度影响较大的是主偏角Kr、副偏角Kr'和刀尖圆弧半径re。当主、副偏角小时,已加工表面残留面积的高度亦小,因而可减小表面粗糙度;副偏角越小,表面粗糙度越低,但减小副偏角容易引起震动,故减小副偏角,要根据机床的刚性而定。刀尖圆弧半径re对表面粗糙度的影响:在刚度允许的情况下re增大时,表面粗糙度将降低,增大re是降低表面粗糙度的好方法。因此减少主偏角Kr、副偏角Kr’以及增大刀尖圆弧半径r,均可减小残留面积的高度,从而降低表面租糙度。
刀具工程师说过,“对于刀尖圆弧角的选择建议依据加工工件的刚性和粗糙度要求选择,如果刚性好,尽量选择大的圆弧角,不但可提高加工效率,亦可提高加工表面光洁度;但镗孔时或者切削细长轴或薄壁零件时因为系统刚性差,常选用较小的刀尖圆弧半径”。3. 3
刀具磨损
刀具的磨损分为三个阶段:初期磨损、正常磨损和剧烈磨损。当刀具进入剧烈磨损阶段,刀具后刀面磨损率急剧上升,系统又趋向于不稳定,振动随之增大,表面粗糙度的变化幅度也急剧上升。
在灰铸铁领域,很多零件都属于批量生产,对其产品质量的一致性和生产效率要求较高,因此很多机加工企业不等到刀具达到剧烈磨损第三阶段就选择换刀,也称之为强制换刀,机加工企业会对刀具进行反复测试,确定一个临界点,在保证灰铸铁表面粗糙度要求和尺寸精度的情况下,又不影响整体生产效率。
3、切削参数对灰铸铁零件表面粗糙度的影响
切削参数选择的不同,对表面粗糙度影响较大,应引起足够的重视。精加工是保证灰铸铁零件表面粗糙度的重要工序,因此精加工时,切削参数应以保证灰铸铁零件表面粗糙度为主,并兼顾生产率和必要的刀具寿命。精加工的吃刀深度是根据加工精度和表面粗糙度要求,由粗加工后留下的余量确定的,一般吃刀深度控制在0.5mm以内。同时在机床刚性条件许可的条件下,可充分发挥刀具的切削性能,采用较高的切削速度对灰铸铁零件进行高速加工。
4、其他因素对灰铸铁零件表面粗糙度的影响
如灰铸铁零件自身存在一些铸造缺陷,切削液选择不合理,加工方式的不同等都会影响灰铸铁零件的表现粗糙度。
刀具工程师说过,“除了机床,刀具,切削参数三大因素外,切削液,灰铸铁零件本身,加工方式等因素也对灰铸铁零件的表面粗糙度造成一定的影响,如车削、铣削、镗削灰铸铁零件时,在机床,切削参数等因素都许可的条件下,CBN刀具亦可加工出Ra0.8的表面粗糙度,但对刀具寿命会有所影响,具体需要根据实际加工情况判断”。
5、总结
鉴于表面粗糙度对机器零件使用性能有较为直接的影响,而实际生产中影响表面粗糙度的因素又是来自多方面的,因此应该全方面兼顾各种因素,对表面粗糙度根据需要提出比较经济适用的要求。
三、如何提高铸件表面光洁度(球墨铸铁件)
喷砂法
工艺:
汽油(120#)洗刷压缩空气吹干→喷砂→压缩空气吹净砂粒→装挂→弱腐蚀→流动冷水冲洗→电镀锌或硬铬。
弱腐蚀工艺:w(硫酸)=5%~10%,室温,5~10s。
浸蚀、洗刷法
当工件因精度或表面光洁度特殊要求而不允许采取喷砂处理时,只能采取浸蚀、洗刷的方法净化表面。
步骤:
①汽油洗刷(120#)。油多的工件或汽油用脏时洗后要用洁净的120#汽油再洗刷一遍。②压缩空气吹干。
③浸蚀。w(盐酸)=15%,w(氢氟酸)=5%,室温,锈迹除净为止。若锈迹过多、氧化皮过厚则应先用机械法刮去。浸蚀时间不宜过长,否则容易造成基体渗氢,而且使表面游离碳裸露过多,导致局部或全部镀不上镀层。④石灰浆擦刷可以将工件表面晶格充分暴露,获得结合力良好的镀层。⑤冲洗与揩擦。去除表面粘附的石灰。
⑥装挂。铸铁件导电性差,装挂时应接触牢固,接触点尽可能多设几处,工件与工件之间的间距与其它材质电镀件相比,略大0.3倍为好。⑦活化。活化的目的是除去在擦刷、装挂等工序中形成的氧化膜。配方与工艺条件:w(硫酸)=5%~10%,w(氢氟酸)=5%~7%,室温,5~10s。⑧流水冲洗。⑨电镀锌或硬铬。