在传统铸造工艺中,制作原型所需的模具随着设计的变更也必须进行改变。进行变更所需的成本和时间也决定于这是一次怎样的变更,平均来说即使一个细微的变更也需要15%的模具制作成本和2周的时间。在Tech Cast公司的3D打印工艺中,3D打印模型将被用于制作新的原型,直接用于铸造。
Tech Cast公司通过3D打印工艺来创建的原型,可作为直接铸造用原型。在北美,这是常用的直接原型制作技术。有了3D打印原型,无需耗费时间来制作蜡模。如此一来,数天内就可以评估新设计,而不是数月。
Tech Cast公司通过3D打印工艺来创建的原型,可作为直接铸造用原型。在北美,这是常用的直接原型制作技术。有了3D打印原型,无需耗费时间来制作蜡模。如此一来,数天内就可以评估新设计,而不是数月。
3D打印原型只占传统模具制作成本的一小部分,并且一周内就能完成,所以在3周内完全加工泵轮是可行的。3D打印工艺制作的树脂原型内部是中空的,会有加温导致原型膨胀的风险。但是因为有蜂窝状的结构,避免了把模壳撑坏。这样最大程度地减少了原型所用的材料,另外可以说是几乎无残余的燃烧,也能够快速地完成铸造工序,而无需其他额外步骤。
3D打印滤镜的制造方法为可定制的滤镜孔,尺寸,形状和性能开辟了新的可能性。 该方法的一些优点是增加熔融金属的流速并减少熔融金属中陶瓷碎屑的夹杂。
3D打印滤镜的制造方法为可定制的滤镜孔,尺寸,形状和性能开辟了新的可能性。 该方法的一些优点是增加熔融金属的流速并减少熔融金属中陶瓷碎屑的夹杂。
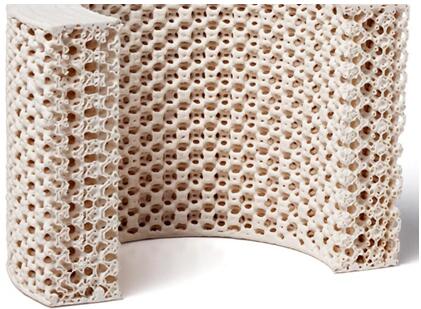
问:对于大型铸件,我们需要过滤熔融金属以消除杂质并降低清洁金属的成本,但是目前可用的过滤技术还不够。 主要是因为过滤材料在铸造过程中堵塞过快。 哪些产品可以解决此问题?
答:针对此问题,有几种不同的技术解决方案供您考虑。 第一种方法是通过浇口系统中的多个过滤器进行过滤,以确保铸造大型铸件所需的过滤能力。
另一种可能的解决方案是通过具有多个过滤器的组件进行过滤,或者通过表面积增大的过滤器(例如管道)进行过滤。
第三种选择是找到一种具有与传统过滤器相同的抗热震性的过滤器,但其设计目的是在提高过滤能力(容量)的同时仍消除那些杂质。
在这三种选择中,最容易实现且最具成本效益的是第三种选择。 在所有这些金属过滤技术中,您都需要找到具有此属性的过滤器。 现在,找到这种理想产品的最可能方法将是新兴的增材制造技术。 换句话说,它是“ 3D打印过滤器”。
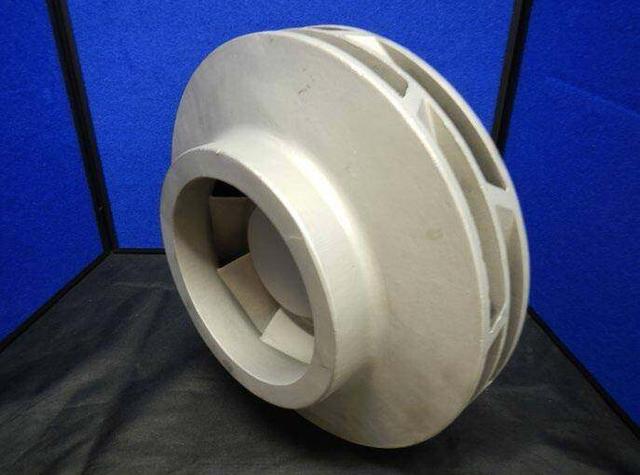
最近,ASK Chemicals(Ask Chemicals)推出了EXACTPORE 3D系列,它将解决您的所有问题。 该过滤器为钢铁铸造厂和铸造厂提供了新的更有效的过滤选项,以实现最高的铸造质量。 得益于其精心设计,EXACTPOORE 3D滤镜具有最高的结构完整性,因此使用安全高效。
熔融金属的纯度是铸造厂最重要的要求之一。 优选的熔融金属过滤器包括烧结的陶瓷泡沫过滤器,但是泡沫过滤器的特殊构造意味着这种形式的过滤器也有其局限性。 在陶瓷层的涂覆过程中以及在烧结过程中,可能在过滤器结构内部形成微小的颗粒,并且这些微小的颗粒仅与基质材料一起被轻微烧结。 熔融金属流经过滤器会导致颗粒从过滤器分离进入熔体,这会损害熔体的纯度并在铸件中造成夹杂物。
EXACTPOORE 3D过滤器的高结构完整性确保了没有松散的颗粒,从而防止了所谓的过滤器碎屑污染熔融金属并耗时费力。
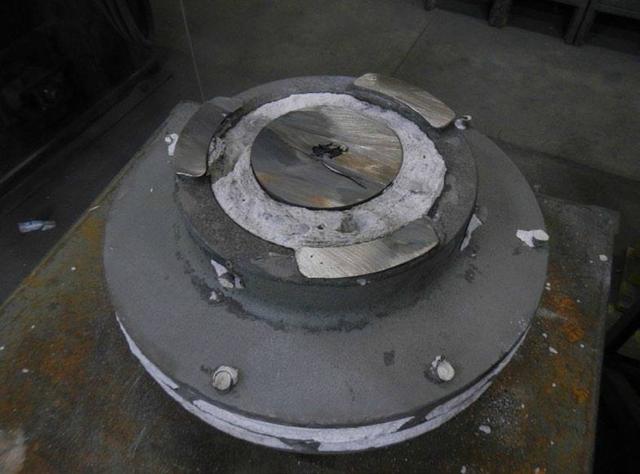
新一代过滤器的另一个优势是它们的流速更高。 由于过滤器设计的均匀性和一致的几何形状,EXACTPORE 3D过滤器比具有相同过滤器孔径的烧结陶瓷泡沫过滤器提供更高的流速,为创建者提供了进一步提高生产率的机会。
与传统解决方案相比,新的过滤器孔径设计的均匀性和结构完整性还显着降低了湍流,并显着防止了由于夹带空气而引起的熔融金属的再氧化。 实际上,几乎没有杂质进入模具,从而减少了返工,提高了表面质量并降低了废品率,最终提高了公司的盈利能力。
谈到新EXACTPOORE 3D滤镜的增材制造所带来的灵活性和可变性时,“我们的新滤镜的制造方式几乎可以无限制地进行铸造设计,” Bob市场经理Bob Gage说。
他强调说:“有了新的过滤器,我们可以为客户提供的孔设计几乎没有限制。” “我们可以生产具有恒定流量特性的几乎任何孔径,甚至是非常规孔径,以确保最佳的过滤质量。”
江苏铸造厂家www.hudongzhuzao.com,欢迎来电询价和参观铸造工厂
江苏铸造厂家www.hudongzhuzao.com,欢迎来电询价和参观铸造工厂