箱体铸件是机械制造业中非常重要的基础零件之一,广泛应用于各种机械设备中。其质量的好坏直接影响到整个机械设备的性能和寿命。那么,如何才能控制好箱体铸件的质量呢?本文将从原材料选择、铸造工艺、热处理、检测方法等多个方面详细解答这个问题,帮助读者全面了解并掌握箱体铸件质量控制的关键点。
一、原材料选择
1.材质选择
箱体铸件常用的材质包括灰铸铁、球墨铸铁、合金铸铁等。不同的材质具有不同的力学性能和适用范围。
灰铸铁:具有良好的减振性和耐磨性,适用于制造大型箱体和基础件。
球墨铸铁:具有较高的强度和韧性,适用于制造需要较高强度和韧性的箱体。
合金铸铁:具有更好的耐热性和耐磨性,适用于特殊工况下的应用。
2.原材料质量
原材料的质量直接影响到最终铸件的质量。优质的原材料不仅化学成分稳定,而且杂质含量低,能够保证铸件的性能和稳定性。
需要严格控制原材料中的有害元素(如硫、磷)含量,以减少铸件产生缺陷的可能性。
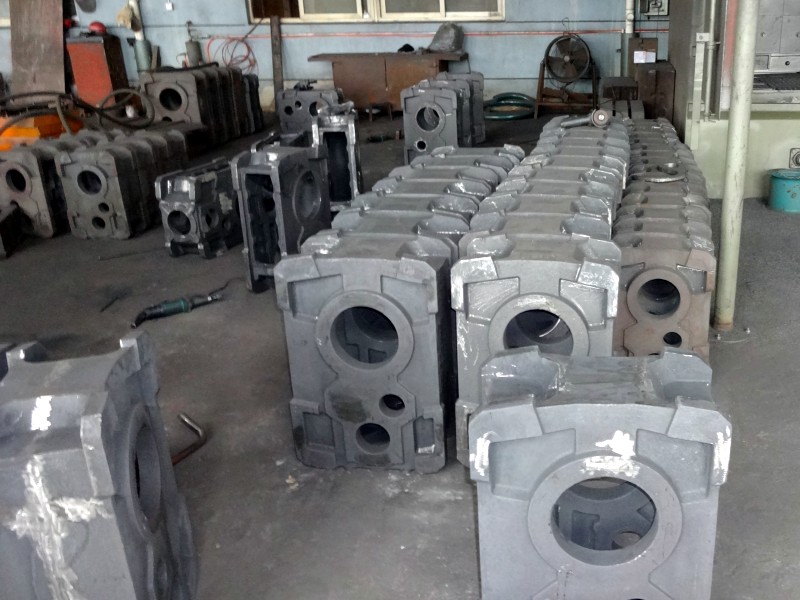
二、铸造工艺
1.熔炼工艺
熔炼工艺是铸造过程中的关键环节,主要包括熔炼温度、保温时间和浇注速度等因素。
熔炼温度:合适的熔炼温度可以保证金属液的流动性,减少气孔和缩孔等缺陷。
保温时间:合理的保温时间可以保证金属液的均匀性,避免成分偏析。
浇注速度:适当的浇注速度可以减少铸件中的夹杂和气孔。
2.模具设计
模具的设计直接关系到铸件的形状和尺寸精度。合理的设计可以有效避免铸件变形和裂纹等问题。
模具材料:需要选用具有良好导热性和耐磨性的材料,以保证铸件的质量。
模具尺寸:需要根据铸件的实际尺寸和收缩率精确计算,确保铸件尺寸准确。
3.浇注工艺
浇注工艺主要包括浇注温度、浇注速度和浇注方式等因素。
浇注温度:浇注温度过高或过低都会影响铸件的组织和性能。
浇注速度:合理的浇注速度可以保证金属液的平稳流动,减少气孔和夹杂。
浇注方式:正确的浇注方式可以减少铸件中的气孔和夹杂。
三、热处理
1.退火处理
退火处理是为了消除铸件中的内应力,改善铸件的力学性能。通过高温加热和缓慢冷却,可以使铸件内部组织均匀化,提高铸件的塑性和韧性。
退火温度:根据具体材质和铸件尺寸确定,一般在600700℃之间。
保温时间:根据铸件厚度确定,一般为每毫米12小时。
2.正火处理
正火处理是为了细化晶粒,提高铸件的硬度和耐磨性。通过加热至一定温度后快速冷却,可以使铸件内部组织变得细小均匀,从而提高铸件的整体性能。
正火温度:根据具体材质和铸件尺寸确定,一般在800900℃之间。
冷却速度:根据铸件厚度确定,一般采用水冷或油冷。
3.调质处理
调质处理是为了进一步提高铸件的综合性能。通过淬火加回火的方式,可以同时提高铸件的强度和韧性。
淬火温度:根据具体材质和铸件尺寸确定,一般在800900℃之间。
淬火介质:根据铸件厚度确定,一般采用水或油。
回火温度:根据具体材质和铸件尺寸确定,一般在500600℃之间。
四、检测方法
1.外观检测
外观检测是最基本的质量检测方法,主要检查铸件的表面缺陷,如裂纹、气孔、夹杂等。
目测:通过肉眼观察铸件表面是否有明显缺陷。
量具测量:使用游标卡尺、千分尺等工具测量铸件的尺寸和形位公差。
2.尺寸检测
尺寸检测是为了保证铸件的尺寸精度,主要使用游标卡尺、千分尺等精密量具进行测量。
游标卡尺:用于测量铸件的基本尺寸。
千分尺:用于测量铸件的精密尺寸。
三坐标测量仪:用于测量复杂铸件的尺寸和形位公差。
3.无损检测
无损检测是目前广泛应用的质量检测方法,主要包括磁粉探伤、渗透探伤、超声波探伤等。
磁粉探伤:可以检测铸件表面和近表面的裂纹等缺陷。
渗透探伤:可以检测铸件表面开口缺陷。
超声波探伤:可以检测铸件内部缺陷,如气孔、夹杂等。
4.力学性能检测
力学性能检测是为了验证铸件的力学性能是否符合标准要求,主要包括拉伸试验、弯曲试验、冲击试验等。
拉伸试验:用于测定铸件的抗拉强度、屈服强度等。
弯曲试验:用于测定铸件的弯曲强度和韧性。
冲击试验:用于测定铸件的冲击韧性。
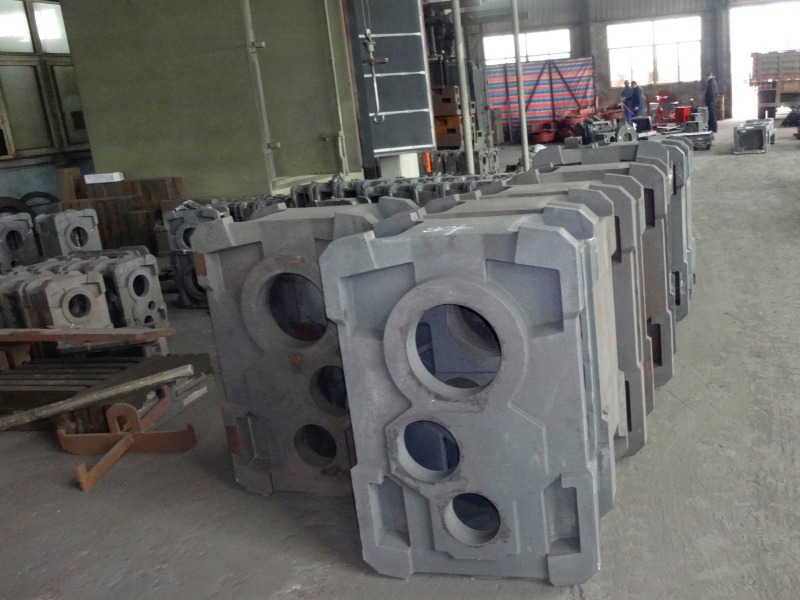
五、案例分析
为了更好地理解上述因素对箱体铸件质量的影响,我们来看几个实际案例:
1.案例一:某工厂生产的箱体铸件出现大量气孔
分析原因:该厂使用的原材料中含有较多的气体,导致熔炼过程中产生大量气泡;浇注工艺不合理,浇注速度过快,无法及时排出气泡。
解决方案:严格控制原材料质量,减少气体含量;调整浇注工艺,降低浇注速度,增加排气措施。
2.案例二:某工厂生产的箱体铸件出现裂纹
分析原因:该厂使用的模具设计不合理,铸件在冷却过程中产生较大的内应力;热处理工艺不当,铸件未充分消除内应力。
解决方案:重新设计模具,改善铸件的冷却条件;优化热处理工艺,充分消除内应力。
3.案例三:某工厂生产的箱体铸件尺寸超差
分析原因:该厂的模具精度不够,导致铸件尺寸不准确;检测方法不规范,未能及时发现尺寸偏差。
解决方案:提高模具精度,确保铸件尺寸准确;规范检测方法,加强尺寸检测,及时纠正偏差。
六、总结
箱体铸件的质量控制是一个系统工程,涉及原材料选择、铸造工艺、热处理和检测方法等多个方面。只有在各个环节都做到精细化管理,才能生产出高质量的箱体铸件。具体来说:
1.原材料选择:选择优质原材料,严格控制有害元素含量。
2.铸造工艺:优化熔炼工艺、模具设计和浇注工艺,减少铸件缺陷。
3.热处理:合理安排退火、正火和调质处理,提高铸件的综合性能。
4.检测方法:严格进行外观检测、尺寸检测、无损检测和力学性能检测,确保铸件质量。
希望本文能为广大读者提供参考,帮助大家更好地理解和掌握箱体铸件质量控制的关键点,从而提升生产水平和产品质量。如果您还有其他关于箱体铸件的问题,欢迎随时咨询相关专业人士。希望本文能对您有所帮助!
如果您需要进一步了解箱体铸件的具体应用和技术细节,可以查阅相关技术资料或联系专业的铸造厂家获取更多信息。希望本文能帮助您在实际生产中更好地控制箱体铸件的质量,提高生产效率和产品竞争力。
一、原材料选择
1.材质选择
箱体铸件常用的材质包括灰铸铁、球墨铸铁、合金铸铁等。不同的材质具有不同的力学性能和适用范围。
灰铸铁:具有良好的减振性和耐磨性,适用于制造大型箱体和基础件。
球墨铸铁:具有较高的强度和韧性,适用于制造需要较高强度和韧性的箱体。
合金铸铁:具有更好的耐热性和耐磨性,适用于特殊工况下的应用。
2.原材料质量
原材料的质量直接影响到最终铸件的质量。优质的原材料不仅化学成分稳定,而且杂质含量低,能够保证铸件的性能和稳定性。
需要严格控制原材料中的有害元素(如硫、磷)含量,以减少铸件产生缺陷的可能性。
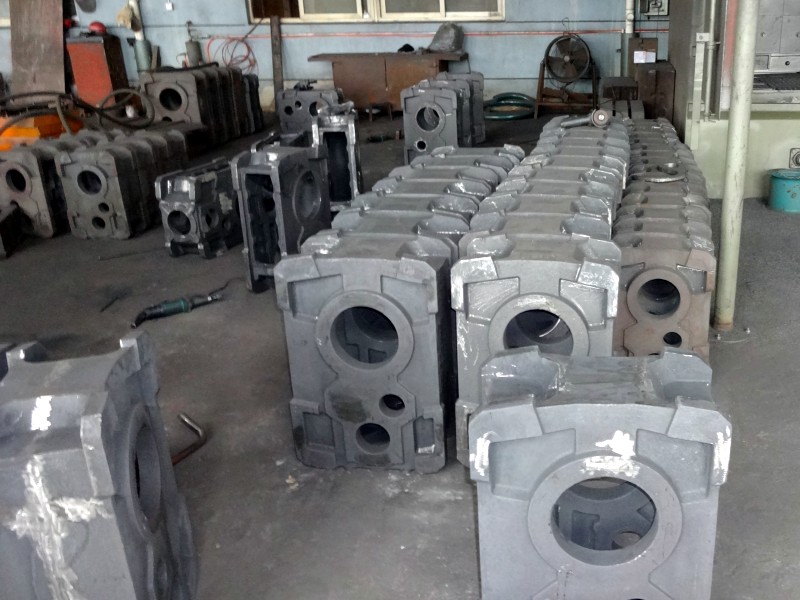
二、铸造工艺
1.熔炼工艺
熔炼工艺是铸造过程中的关键环节,主要包括熔炼温度、保温时间和浇注速度等因素。
熔炼温度:合适的熔炼温度可以保证金属液的流动性,减少气孔和缩孔等缺陷。
保温时间:合理的保温时间可以保证金属液的均匀性,避免成分偏析。
浇注速度:适当的浇注速度可以减少铸件中的夹杂和气孔。
2.模具设计
模具的设计直接关系到铸件的形状和尺寸精度。合理的设计可以有效避免铸件变形和裂纹等问题。
模具材料:需要选用具有良好导热性和耐磨性的材料,以保证铸件的质量。
模具尺寸:需要根据铸件的实际尺寸和收缩率精确计算,确保铸件尺寸准确。
3.浇注工艺
浇注工艺主要包括浇注温度、浇注速度和浇注方式等因素。
浇注温度:浇注温度过高或过低都会影响铸件的组织和性能。
浇注速度:合理的浇注速度可以保证金属液的平稳流动,减少气孔和夹杂。
浇注方式:正确的浇注方式可以减少铸件中的气孔和夹杂。
三、热处理
1.退火处理
退火处理是为了消除铸件中的内应力,改善铸件的力学性能。通过高温加热和缓慢冷却,可以使铸件内部组织均匀化,提高铸件的塑性和韧性。
退火温度:根据具体材质和铸件尺寸确定,一般在600700℃之间。
保温时间:根据铸件厚度确定,一般为每毫米12小时。
2.正火处理
正火处理是为了细化晶粒,提高铸件的硬度和耐磨性。通过加热至一定温度后快速冷却,可以使铸件内部组织变得细小均匀,从而提高铸件的整体性能。
正火温度:根据具体材质和铸件尺寸确定,一般在800900℃之间。
冷却速度:根据铸件厚度确定,一般采用水冷或油冷。
3.调质处理
调质处理是为了进一步提高铸件的综合性能。通过淬火加回火的方式,可以同时提高铸件的强度和韧性。
淬火温度:根据具体材质和铸件尺寸确定,一般在800900℃之间。
淬火介质:根据铸件厚度确定,一般采用水或油。
回火温度:根据具体材质和铸件尺寸确定,一般在500600℃之间。
四、检测方法
1.外观检测
外观检测是最基本的质量检测方法,主要检查铸件的表面缺陷,如裂纹、气孔、夹杂等。
目测:通过肉眼观察铸件表面是否有明显缺陷。
量具测量:使用游标卡尺、千分尺等工具测量铸件的尺寸和形位公差。
2.尺寸检测
尺寸检测是为了保证铸件的尺寸精度,主要使用游标卡尺、千分尺等精密量具进行测量。
游标卡尺:用于测量铸件的基本尺寸。
千分尺:用于测量铸件的精密尺寸。
三坐标测量仪:用于测量复杂铸件的尺寸和形位公差。
3.无损检测
无损检测是目前广泛应用的质量检测方法,主要包括磁粉探伤、渗透探伤、超声波探伤等。
磁粉探伤:可以检测铸件表面和近表面的裂纹等缺陷。
渗透探伤:可以检测铸件表面开口缺陷。
超声波探伤:可以检测铸件内部缺陷,如气孔、夹杂等。
4.力学性能检测
力学性能检测是为了验证铸件的力学性能是否符合标准要求,主要包括拉伸试验、弯曲试验、冲击试验等。
拉伸试验:用于测定铸件的抗拉强度、屈服强度等。
弯曲试验:用于测定铸件的弯曲强度和韧性。
冲击试验:用于测定铸件的冲击韧性。
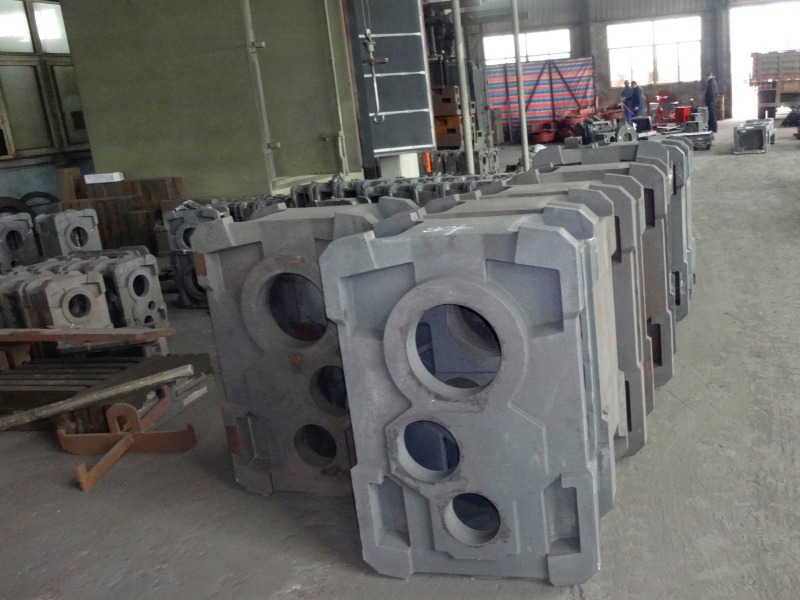
五、案例分析
为了更好地理解上述因素对箱体铸件质量的影响,我们来看几个实际案例:
1.案例一:某工厂生产的箱体铸件出现大量气孔
分析原因:该厂使用的原材料中含有较多的气体,导致熔炼过程中产生大量气泡;浇注工艺不合理,浇注速度过快,无法及时排出气泡。
解决方案:严格控制原材料质量,减少气体含量;调整浇注工艺,降低浇注速度,增加排气措施。
2.案例二:某工厂生产的箱体铸件出现裂纹
分析原因:该厂使用的模具设计不合理,铸件在冷却过程中产生较大的内应力;热处理工艺不当,铸件未充分消除内应力。
解决方案:重新设计模具,改善铸件的冷却条件;优化热处理工艺,充分消除内应力。
3.案例三:某工厂生产的箱体铸件尺寸超差
分析原因:该厂的模具精度不够,导致铸件尺寸不准确;检测方法不规范,未能及时发现尺寸偏差。
解决方案:提高模具精度,确保铸件尺寸准确;规范检测方法,加强尺寸检测,及时纠正偏差。
六、总结
箱体铸件的质量控制是一个系统工程,涉及原材料选择、铸造工艺、热处理和检测方法等多个方面。只有在各个环节都做到精细化管理,才能生产出高质量的箱体铸件。具体来说:
1.原材料选择:选择优质原材料,严格控制有害元素含量。
2.铸造工艺:优化熔炼工艺、模具设计和浇注工艺,减少铸件缺陷。
3.热处理:合理安排退火、正火和调质处理,提高铸件的综合性能。
4.检测方法:严格进行外观检测、尺寸检测、无损检测和力学性能检测,确保铸件质量。
希望本文能为广大读者提供参考,帮助大家更好地理解和掌握箱体铸件质量控制的关键点,从而提升生产水平和产品质量。如果您还有其他关于箱体铸件的问题,欢迎随时咨询相关专业人士。希望本文能对您有所帮助!
如果您需要进一步了解箱体铸件的具体应用和技术细节,可以查阅相关技术资料或联系专业的铸造厂家获取更多信息。希望本文能帮助您在实际生产中更好地控制箱体铸件的质量,提高生产效率和产品竞争力。