铸造行业人士都知道铸件的球化率直接决定了铸件的质量,今天给大家讲一下解决铸件球化率不高的三种办法,导致球化率过低的原因基本有三个方面:原铁水含硫量太高、球化元素的残留量低、铁液内含有过量的反球化元素或稀土量与反球化元素不平衡,接下去详细分析下这三个原因:
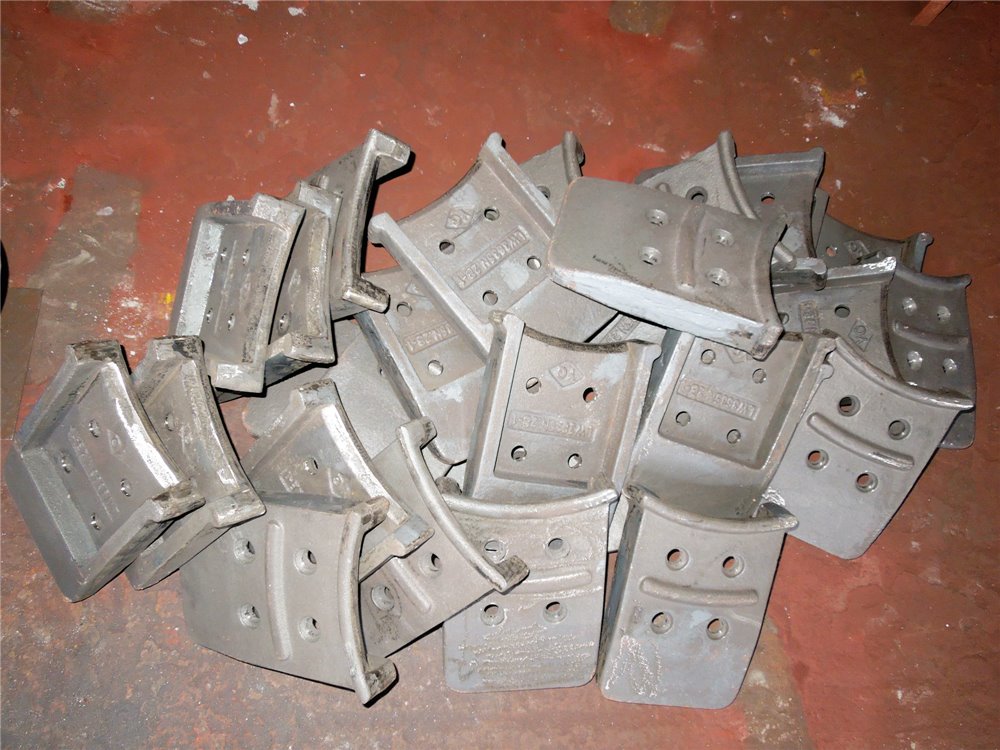
耐磨铸件
1、原铁水含硫量高
硫是反球化率元素,它与镁有很强的亲和力,反应生成MgS,而耗费了有用镁,因此导致球化不良,此刻需要多加球化剂才华确保球化,出产高品质的球铁,其原始铁液的含硫量,国外一般都控制在0.02%高于此量都有必要进行脱硫处理,这样既确保了充分的球化也减少了发作渣孔的风险,一同球化剂的参与量才得以安稳,也确保了残余镁量波动不大,我国的现实情况是,冲天炉的原铁水含硫量一般为0.05-0.06%或以上,中频炉铁水的含硫量一般为0.02-0.035%,但大多数厂家不做脱硫处理,而靠变动球化剂的量来确保球化,其参与量国内各厂不同很大,在0.8-1.8%大范围内波动,而残镁量的范围介于0.03-0.08%常常出现球化不良或过球化现象,含镁量过高构成了铸件渣孔,缩松,反白口缺点,含镁过高,石墨也会变坏,许多厂为了确保球化杰出往往在晶间出现水草状石墨。
要得到好的球化作用,还要留心Mg残/S残的份额适宜,壁厚少于15mm的小铸件,范围在2.7-4.0之间,易发作收缩的铸件(特别是热节处无补缩才干时)应控制在2.4-3.0%之间,壁厚在15-30mm之间的铸件,范围在3.0-4.5%之间,易缩件在2.7-3.5%之间,壁厚大于30mm的厚铸件,范围在3.5-5之间就是说薄铸件镁要低点防止发作白口,热节易生缩松的铸件,镁应低为好,厚铸件镁要高,以补偿镁蒸气逃逸损失,不至于使镁量下降而导致不球化。原始含硫量过低(<0.005%)也是不所期望的,因这样的原铁液会孕育不良,简略生成碳化物,去年河南某厂选用喂丝工艺出产球铁,原铁水含硫量已低于0.006%,参与的球化剂没减少,因此铸件发作了30%以上的渗碳体,实践证明,球铁原铁液中的硫对球铁铸件的石墨球数和石墨标准散布有很大影响,因为石墨球数随硫含量的增加而增加,所以在出产白口倾向较大的薄壁铸件时,选用较高的含硫量,是防止碳化物构成的有用办法。防止薄壁铸件发作白口有一个临界石墨球数,铸件越薄,石墨的球数应当越高,但原铁液含硫过高,会使石墨分出过早,石墨球数过多,且标准均匀,导致缩孔倾向增大,这种现象出现在厚断面铸件上,为了安稳得到相同的安稳的球数,应当维持各处理球铁的原铁液的含硫量一同,建议原始含硫量安稳在0.02-0.015%范围内。
2、球化元素的残留量低
为使石墨球化杰出,球铁中有必要含有一定量的镁和稀土,镁起首要球化作用,稀土起辅佐作用,镁残量低是构成球化不良的重要原因,依据铸件壁厚及浇注温度的高低,和浇注时间的长短以及原始含硫量及含碳量的多少,一般残留镁量控制在0.03-0.05%为好,特大件镁可至0.1%,一般薄壁件取低值,壁厚件取高值,但原则上,是只需确保球化杰出,残镁量越低越好。
至于构成残镁量过低的原因,大多数是炉工操作上失误引起的,其中包含:
a 球化剂称量禁绝,或者磅秤没定期校准,球化剂量参与低。
b 没有依据出炉温度高低,含硫量多少,铁水包温度来调整球化剂参与量,而出炉温度不该过高,铁水包接连出炉,温度过高时,应当用压缩空气将合金坑降温后才参与球化剂,且球化剂不要参与过早。
c 球化剂质量欠好,含MgO太高,夹杂物多,比重轻。
d 球化包结构不合理,其高/直径比应在1.5-2.0,合金坑标准应合理能容纳下全部合金。
e包坑内加上球化剂后,应当填平填实,然后顺次加上孕育剂和珍珠岩掩盖剂,最上面应参与干净干燥的球铁切屑,或碎钢板掩盖。
3、铁液内含有过量的反球化元素或稀土量与反球化元素不平衡
当反球化元素超出答应范围时,就会影响球化作用。这些反球化元素,首要来源于生铁和废钢,一般碳素钢是不会含反球化元素的,可是在合金钢里往往会掺杂一些反球化元素,配料时,最好少用或不必合金钢废料做炉料,过去很长一段时间内,我国出产的球铁的生铁质量很欠好,许多反球化元素超支,尤其是钛含量高,因此,改革开放曾经,各个大型企业出产球铁件时都指明要用本溪生铁,为处理生铁质量欠好,抵消反球化元素对球化质量的影响,我国推出了硅铁镁稀土球化剂,比较好地处理了其时我国没有好生铁出产球铁的问题,这几年我国已有好几家厂,可出产高纯生铁了,一同一般用的球铁生铁的质量也有了提高,因此,因反球化元素构成球化不良的质量问题现已底子上得到了处理,但在出产高端的球铁铸件时,仍要严格控制反球化的微量元素不该超支。
以上就是江苏沪东机械铸造有限公司整理的“导致球化率不良三个因素及解决办法”,希望对大家有所帮助。
以上就是江苏沪东机械铸造有限公司整理的“导致球化率不良三个因素及解决办法”,希望对大家有所帮助。